It is a consensus in the industry that the difficulty in developing modern aircraft engines lies in their "three highs", namely high speed, high pressure and high temperature. It is indeed very difficult to solve the problems caused by the "three highs".
High speed
The speed of modern aircraft engines varies according to different models. The speed of the low-pressure rotor of a commercial high-bypass ratio engine is generally about a few dry revolutions per minute, and the speed of the high-pressure rotor is between 10,000 and 15,000 revolutions per minute. For example, in the CFM56 series engine, the maximum speed of the low-pressure compressor rotor is a little more than 5,000 revolutions per minute, and the maximum speed of the high-pressure turbine can reach 15,000 revolutions per minute. For military low-bypass ratio turbofan engines, such as the F119 engine, the low-pressure rotor speed is generally around 10,000 revolutions per minute, and the high-pressure rotor speed is around 16,000 revolutions per minute. For the engine to work reliably at such a high speed, extremely stringent requirements are placed on materials, design, and manufacturing.
High temperature
Increasing the temperature of the gas before the turbine is an effective measure to increase the thrust of the engine. For every 50 degrees Celsius increase in the temperature of the gas before the turbine, the engine thrust can be increased by 7%-8%. The gas temperature before the turbine of the fourth-generation aircraft engine has reached more than 1800 degrees Celsius, close to the limit that metal materials can withstand.
High pressure
The concept of total pressure ratio (also called total pressure ratio) is often used to measure engine performance, that is, the ratio of the outlet pressure of the last compressor to the inlet pressure of the first compressor (fan), which is equivalent to the pressure ratio in a turbojet engine. A high total pressure ratio means that the engine thrust is large and generally more fuel-efficient. At present, the total pressure ratio of the afterburner turbofan engine is 25-35, and the total pressure ratio of the high bypass ratio turbofan engine is as high as 35-45. In the future, the total pressure ratio of the high bypass ratio turbofan engine may be increased to 50-100. Such a high internal pressure obviously poses a severe test to all aspects of aircraft engines.
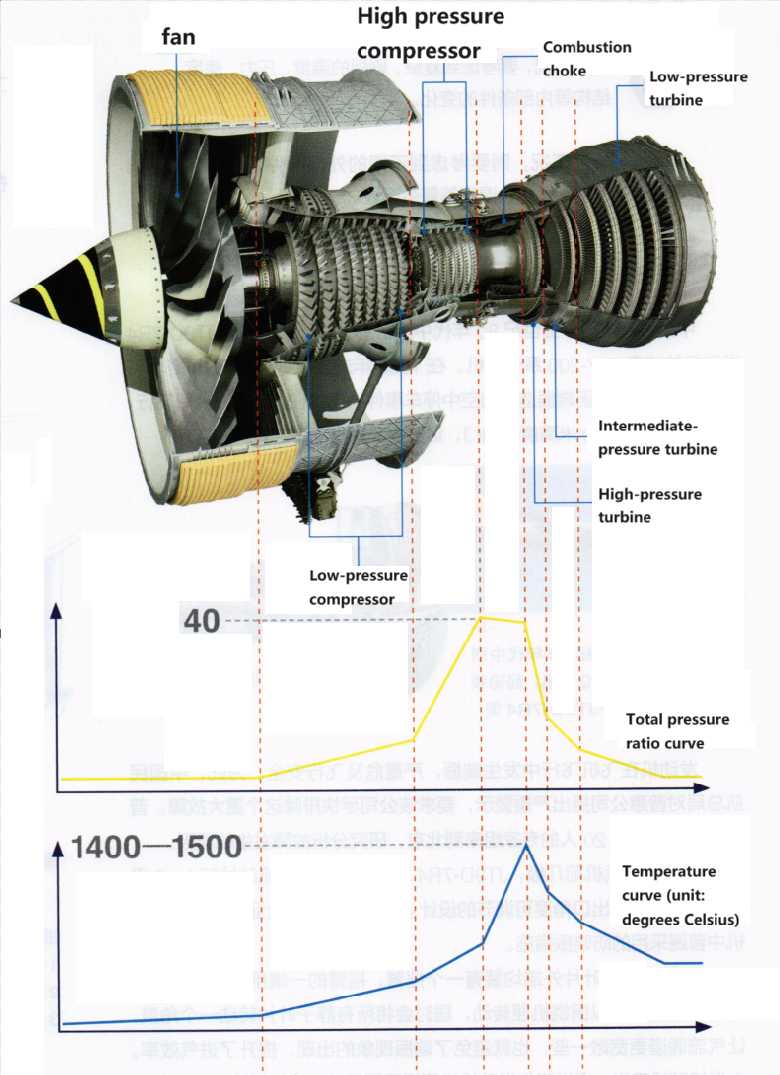
Let’s take the Rolls-Royce Trent 800 engine as an example to see the changes in the two highs - total pressure ratio and temperature (above).
The above is the working environment of modern aircraft engines. In such a harsh environment, aircraft engines must not only meet performance requirements, but also ensure reliable operation. In particular, commercial engines must also meet specific requirements such as fuel saving and environmental protection. Do you think it is difficult?
Engine operating conditions will change suddenly!
The world’s most powerful engine companies GE, Rolls-Royce, and Pratt & Whitney not only strive for excellence in design when developing engines, but also conduct a large number of ground and high-altitude performance tests, and take into account the use of the field, and conduct performance, strength, vibration, durability and reliability tests, as well as component and complete machine tests, covering all aspects. But even so, their engines still had many serious failures. Why? The working conditions of aviation engines are harsh and changeable, and the use conditions are extremely complex. They often face sudden changes in internal and external working conditions.
As long as the pilot pushes the throttle lever, the engine immediately rises from 6,000 to 13,000 to 14,000 revolutions per minute, and the change range is very drastic. As the speed increases, the temperature of each part and component of the engine from front to back also rises, but the increase value is different. In this way, due to the different temperature increases of adjacent components and the difference in thermal expansion coefficients, the original good matching relationship is destroyed, causing the gap at the matching to increase and gas leakage. It is not good if the gap at the matching is too small. If it is stuck too tightly, friction will occur under high-speed operation and damage parts.
In addition, the engine usually starts at a lower speed on the ground. After takeoff, often in a flash, the aircraft has to climb from the ground to an altitude of more than ten kilometers, and the engine instantly reaches the maximum speed. At this time, for the engine, not only the working environment has changed greatly, but also the working conditions of the engine itself have changed greatly. Related components that originally matched well may face unexpected difficulties.
For this reason, when designing an engine, it is necessary to fully consider similar problems that may occur during use and take corresponding measures. However, there are always some shortcomings in the design. Once a failure occurs, it may affect the development progress of the engine, and some may even affect the safe flight of the aircraft.
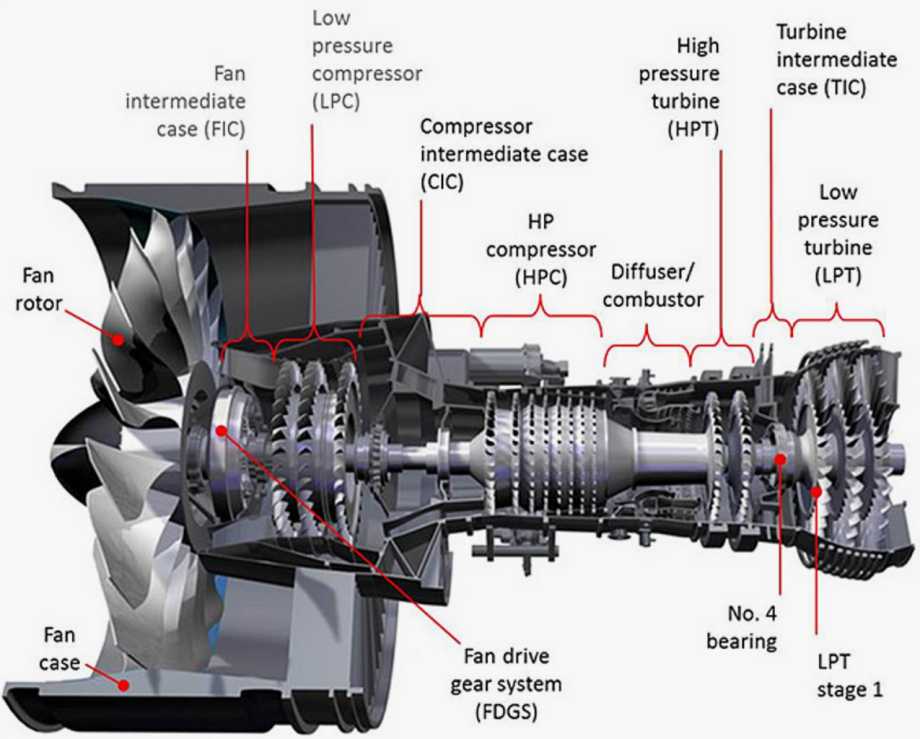
Engine surge
The Civil Aviation Administration of China introduced the Boeing 747-200 series passenger aircraft equipped with Pratt & Whitney JT9D-7R4 engines in the mid-1980s. In the severe winter season from late 1985 to early 1986, 15 mid-air parking incidents caused by surge occurred. The aircraft flew early in the morning on the day of the accident, climbed to an altitude of 600-1500 meters, and closed the throttle. At this time, the fault occurred.
The engine surged during the flight of the aircraft, seriously endangering flight safety. For this reason, the Civil Aviation Administration of China issued a serious warning to Pratt & Whitney, requiring the company to eliminate this major fault as soon as possible. Pratt & Whitney then sent a team of nearly 20 experts to Beijing to study and analyze the cause of the fault. In the first few stages of the high-pressure compressor, the inlet guide vanes and the 1-3 stator blades of the JT9D-7R4 engine adopt an adjustable outlet angle design. This is also a common anti-surge measure used in most high-bypass turbofan engines.
A rocker arm is installed at the outer end of each stator blade, and one end of the rocker arm is inserted into the control ring with a pin. The control ring can rotate around the casing, and then all the stator blades will be rotated to an angle to make the airflow channel wider, thus avoiding the occurrence of surge and improving the intake efficiency. In order to maintain smooth operation, a certain gap needs to be maintained between the control ring and the engine casing. After a comprehensive investigation and analysis, the expert group of Pratt & Whitney found that the gap between the control ring and the casing specified in the original design was not enough. Why? The temperature in Beijing in the deep winter was much lower than it is now, and it was common to have temperatures of more than ten degrees below zero Celsius. The plane stayed overnight at the field, and the engine was frozen for most of the night, and all external and internal parts were at extremely low temperatures. The next day, the crew performed the first flight. The pilot started the engine and pushed the throttle to the take-off state. As the speed increased, the temperature inside the engine rose sharply, and the casing was heated and began to expand outward. The control ring made of composite materials remained at a relatively low temperature outside the engine casing. Although it also expanded, it did not expand as much as the casing. As a result, the control ring was blocked by the expanding casing and could not rotate, and several rows of stationary blades could not adjust the exit angle, causing the engine to surge.
In the end, Pratt & Whitney experts greatly increased the original design gap, taking into account Beijing’s cold climate and leaving enough space for thermal expansion, which solved the problem of causing surge. As can be seen from the table, the amount of change is still large, indicating that the amount of casing expansion is quite large when the engine is working.
Vibration aftermath
A certain type of turbojet engine in China had a major fault of excessive engine vibration during development, which seriously affected the development progress. The development unit was unable to eliminate the fault and had to mobilize experts from the entire industry to help solve it. Including relevant professors from Nanjing University of Aeronautics and Astronautics, Northwestern Polytechnical University and Beihang University, they gathered together to hold a special meeting on vibration issues. After summarizing the opinions of the experts, the meeting proposed troubleshooting measures. After several months of hard work, they were implemented, but once the engine was started, the vibration of the engine was still too large. So a second expert meeting was held, and some modification opinions were proposed. After several months of hard work, the engine was started again, and the result was the same. Where exactly did the problem lie?
Just as the experts were racking their brains and trying every possible way to find a breakthrough, a technician suddenly discovered traces of friction on one end face of the rotor when hoisting the turbine rotor! This trace showed that when the engine was working, there was a collision between the rotor and the stator, which caused excessive vibration in the entire engine.
It turned out that when the engine was designed, the axial spacing between the rotor and the stator was small. When working, the rotor was heated and the expansion was greater than the design value, and the axial friction with the stator occurred, causing excessive vibration. After finding the cause of the excessive vibration, the designers increased the axial spacing between the stator and the rotor, solving the "big problem" that had not been solved for nearly a year.
Uneven heating
At the beginning of this century, Pratt & Whitney developed the geared turbofan engine (GTF). The first model of GTF, PW1000G, is used on many types of aircraft, but many faults occurred in the early days of its use. For example, two engine failures occurred on the A320neo aircraft that had just been put into operation in early 2016, one of which was the "thermal bending" of the high-pressure rotor. If the engine is stopped in a state of slow running for a short time, the cooling may not be sufficient. After stopping, the inside of the engine is still in a high-temperature state, but at this time, the hot air rises, and the temperature of the upper part of the rotor is higher than that of the lower part, resulting in a temperature difference. This causes the deformation amplitude of the upper and lower parts of the high-pressure rotor to be inconsistent, resulting in bending.
After the PW1000G engine has the phenomenon of rotor thermal bending, if it is started again in a short time, not only will the vibration increase, but the tip of the 8th stage working blade will also rub against the casing, and the change in speed will reduce the engine efficiency. For this reason, Pratt & Whitney has lengthened the time between the two working times of the engine and increased the starting time to 7 minutes, so that the engine temperature can be gradually increased to eliminate the thermal bending effect. However, these measures are time-consuming and fuel-consuming, causing dissatisfaction among users. Finally, Pratt & Whitney took three improvement measures to finally solve the thermal bending problem.
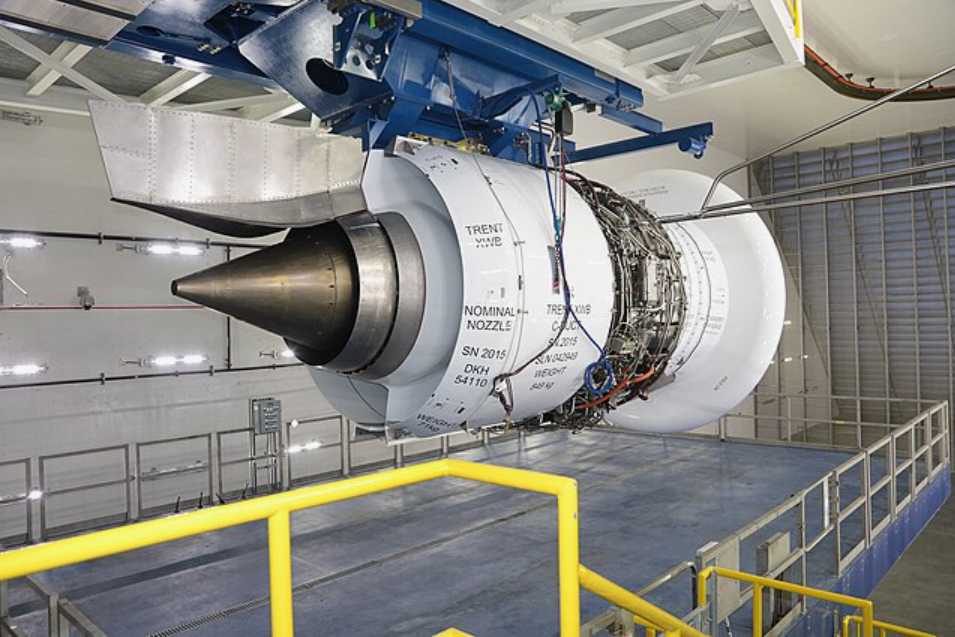
Blade insulation layer falling off
The Trent 1000 is an engine developed by Rolls-Royce for the Boeing 787. In October 2011, the Boeing 787 carried out its first passenger operation, but soon after operation, the engine continued to have problems with the thermal insulation coating of the intermediate pressure turbine working blades falling off. The thermal insulation coating has a different expansion coefficient from the blade material. Under high temperature conditions, the thermal insulation coating expands and dissolves, exposing the corresponding position of the lower turbine blade directly to the high-temperature combustion gas, allowing the sulfide in the combustion gas to corrode the blade, and even causing the blade to break. On August 10, 2019, a Norwegian Air Boeing 787-8 aircraft carried out the DY7115 flight mission from Rome to Los Angeles. Two adjacent working blades on the intermediate pressure turbine of an engine broke due to corrosion, and the resulting fragments flowed backwards. The fragments continued to impact backwards one level at a time, and more and more fragments broke the low-pressure turbine blades. The accumulated fragments amounted to hundreds of pieces, and finally rushed out of the engine and fell to the ground. Fortunately, no one was injured or killed on the ground. The crew used the remaining engine to return to the departure airport safely.
Because Rolls-Royce did not have so many spare parts for intermediate and low-pressure turbine blades, the Boeing 787 stayed on the assembly line and no engine could be installed for a long time. Its far-reaching impact and economic losses are even more difficult to estimate.
Summary
The above accidents all originated from "thermal expansion and contraction", but "thermal expansion and contraction" is only one of the sudden changes in engine working conditions. It can be seen how difficult it is to develop aircraft engines. There are many cases corresponding to the changes in working conditions, and many of them have become stumbling blocks to the smooth development of engines.
The development of aircraft engines needs to go through design, manufacturing, testing, use, failure modification, and retesting... until a satisfactory engine appears. Even so, the engine must be tested during use, especially under various working conditions, to expose problems, solve problems, continuously improve, and constantly explore.