Modern aviation turbine engines are mainly composed of three major components: compressor, combustion chamber and turbine. The fuel burns and expands in the combustion chamber, driving the turbine to rotate. The compressor located in front of the combustion chamber, which is fixed on the same shaft as the turbine, rotates accordingly, sucking more air into the combustion chamber continuously, and the combustion and expansion drive the turbine again, and so on. This is the working principle of the turbine engine. However, in order to achieve higher fuel efficiency and greater thrust, most modern aviation engines have chosen a two- or three-rotor structure, that is, two or three sets of compressor and turbine systems. So, how many rotors are needed for aviation engines?
Long before the Wright brothers invented the airplane, humans had already conducted research and exploration on "turbines". However, the first turbojet engine that was truly installed and flown was the Heinkel HeS 3 centrifugal turbojet engine installed on the German He 178 aircraft in 1939. This engine has only one rotor system, using a two-stage compressor wheel and a one-stage turbine wheel, with a total pressure ratio of 2.8:1 and a maximum thrust of about 500 kg. The rotor blades of the HeS 3 engine are designed centrifugally, and the structure is similar to the turbocharger used in modern cars. It has the characteristics of short axial length and large diameter, and the airflow needs to turn a corner inside the engine.
At the same time, Dr. Anselm Franz of Germany tried to design an axial flow compressor. This design has a smaller engine cross-section and is very suitable for fighter jets that pursue high-speed flight. The Jumo 004 was born. It became the world’s first mass-produced and combat-tested turbojet engine and was widely used in military aircraft such as the Me 262 fighter and the Ar234 bomber. The single-rotor engine has the characteristics of simple structure and fast response speed, but the problem of the single-rotor engine is also obvious-the compression ratio is too low to produce greater thrust.
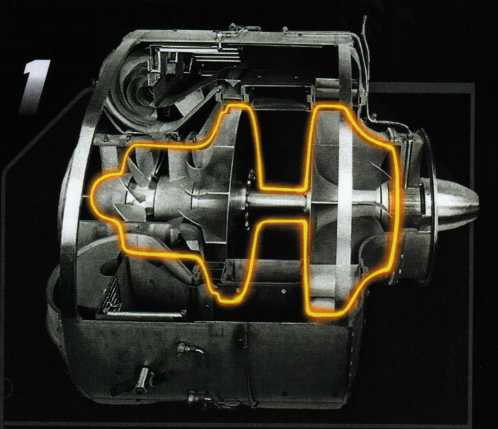
In order to obtain a higher compression ratio, engineers began to try to increase the number of compressor stages, but problems soon emerged and the compressor surged. Surge is an abnormal working state caused by the mismatch between the actual air flow of the compressor and the designed flow. This is a fatal fault, which may cause the engine to stop in the air or even cause fatal damage in severe cases. In order to solve the surge, designers tried to change the diameter of the intake duct and increase the bleed valve, but they could not solve it perfectly. Because the speed of each compressor disc on a single rotor is the same, the more stages there are, the less the compressor disc at the rear can handle the pressurized air, and the use of bleed valves will reduce the efficiency of the engine. The single-rotor engine has reached a technical bottleneck in order to achieve a breakthrough.
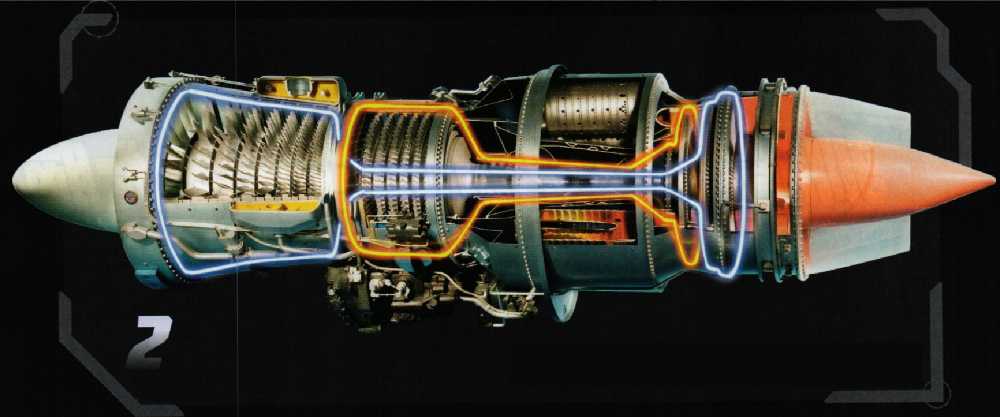
In order to improve the working efficiency of the compressor and increase the engine surge margin, in the 1950s, Pratt & Whitney used a dual-rotor structure for the first time on its J57 turbojet engine. It is equivalent to nesting two sets of single-rotor engines together. The different speeds of the high and low pressure rotors enable each level of compressor to work in the most ideal efficiency range, and the total pressure ratio reaches more than 12. The J57 series engines have been widely used in many jet airliners, fighters, and bombers such as Boeing 707, B-52KC-135, and DC-8. Since then, aviation turbine engines have officially entered the dual-rotor era. In order to meet the requirements of large transport aircraft for engines with high thrust, low fuel consumption, low noise and exhaust pollution, and easy maintenance, in the 1960s, the British Rolls-Royce Engine Company began to study the three-rotor solution. Compared with the dual-rotor structure, the three-rotor structure allows the fan, low-pressure compressor, and high-pressure compressor to use one rotor each, thereby further exerting their respective optimal efficiency. In the mid-1960s, Rolls-Royce successfully developed the twin-rotor RB178, the three-rotor RB203 and the RB207. In 1965, Rolls-Royce developed the world’s first commercial three-rotor turbofan engine RB178-51 based on the RB178 engine, and applied it on the L-1011 passenger aircraft. After decades of development, Rolls-Royce has carried forward the three-rotor engine design experience gained from the RB211, and has generously used the three-rotor structure in the design of all series of engines in the successor model "Trent" family. Its design and production technology have become Rolls-Royce’s secret recipe. Compared with the twin-rotor, the three-rotor has many advantages, including fewer stages and adjustable stator blades, good rotor rigidity, good starting and acceleration performance, low operating temperature of high-pressure turbine blades, and low landing approach noise. But the disadvantages are also obvious. The complex structure brings a series of design difficulties to the rotor support, force transmission and lubrication. Fortunately, the engineers of Rolls-Royce have solved these difficulties one by one. Rolls-Royce’s "Trent" series three-rotor engines have been installed on Boeing 747, 757, 767, 777, 787, Airbus A330 and other models, and have achieved great success in the commercial market.
Almost at the same time, the Soviets also came up with a solution for the design of three-rotor engines. The D-36 was installed in the Yak-42 in an anti-regular way of "engine giving birth to aircraft". The subsequent improved D-436 engine was also widely used in models such as An-72/74 and Be-200 seaplanes. In the 1980s, the three-rotor engine D-18T with larger size and thrust was installed on the An-124 and An-225 heavy strategic transport aircraft, becoming a classic of the generation. In the field of military engines, the three-rotor engine NK-32 with a small bypass ratio and high thrust developed by the Kuznetsov Design Bureau, installed on the Tu-160 and Tu-22M3 Tu-160, became the core power of the Soviet strategic air force.
Careful readers may find that the three-rotor engine does not appear in the product list of the American aviation engine company. This is indeed the case. Neither GE nor Pratt & Whitney has a three-rotor design. Compared with the three-rotor, the dual-rotor reduces the design difficulty of the rotor support structure and the lubricating oil system. However, although the structure is simple, it puts higher requirements on the working efficiency of the low-pressure system. Thanks to the strong industrial and technological foundation, the United States has greater technical advantages in the core technology of aviation engines. For example, the US military aviation engine F101, based on which, eventually derived and developed the classic CFM-56 series of engines. Pratt & Whitney benefited from the great success of the JT8 series of engines and developed a series of successful dual-rotor models such as the high-bypass ratio JT9D and the subsequent PW2000/4000. In the field of military engines, Pratt & Whitney’s F-119, F-22, and F-135 all use a dual-rotor structure. Thanks to the most advanced technology, the latter has a terrifying compression ratio of 28:1, which is difficult for other competitors to achieve.
However, Pratt & Whitney has been looking for solutions to further improve the efficiency of the low-pressure rotor. Since the three-rotor solution is difficult, Pratt & Whitney finally chose to install a reduction gear in front of the low-pressure rotor. After the failure of the PW8000 exploration, Pratt & Whitney finally successfully came up with the GTF Pure Power PW1000G series of high-bypass turbofan engines in the early 21st century, solving the problem of low efficiency of the low-pressure rotor of the dual-rotor engine in the high-bypass turbofan engine.
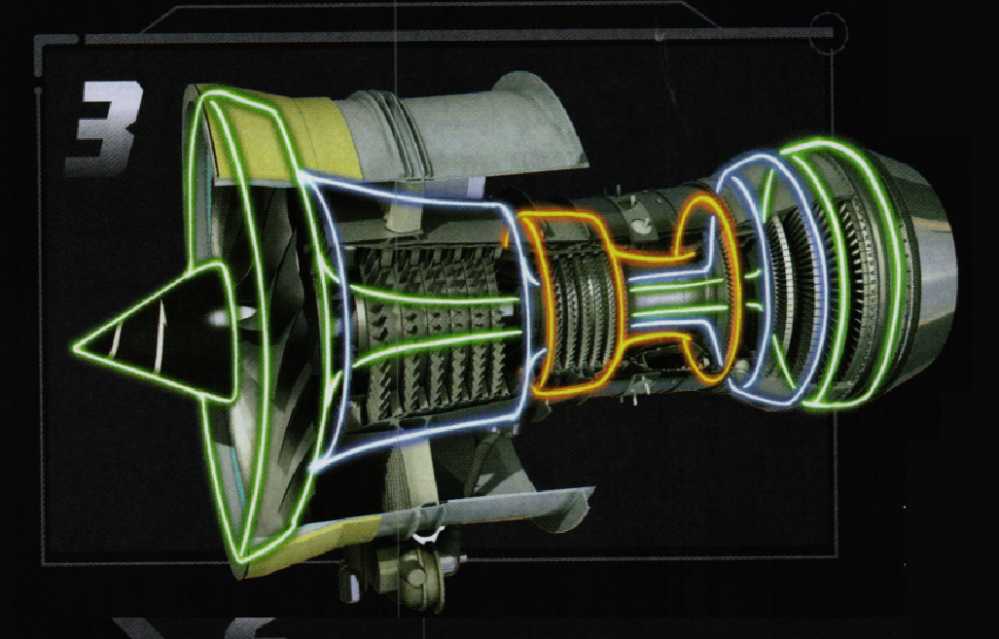
Back to the original question, how many rotors does an aircraft engine need?
Theoretically, if there are no restrictions on structure, bearings, etc., the most ideal state is of course that each stage of the turbine-compressor is an independent rotor, each working in the most efficient speed range. However, aircraft engine manufacturing is not theoretical mechanics, and it is necessary to face every practical engineering problem. Therefore, three rotors are the most acceptable rotor solution in current engineering. The gear-driven fan is the best solution to enable the dual-rotor structure to obtain three-stage speed. If you want to further improve the speed efficiency, an extreme idea is to add a planetary reduction gear to the front end of the three-rotor structure of the Rolls-Royce engine, and then use the most advanced ultra-high pressure ratio core engine, variable external bypass nozzle, advanced carbon fiber composite fan, TAPSI combustion chamber and other new technologies of the LEAP series engine, integrating the advantages of each company. However, engineering design is a process of trade-offs. In the design of aircraft engines, whether blindly "stacking" can achieve maximum efficiency is another topic.