Aviation engines are the core components of various powered aircraft. They must output as much power as possible with the smallest possible volume and maintain extremely high reliability, so they are known as the "crown jewel of industry"
The aviation engines currently used include piston engines with the same principles as automobile engines, as well as turbojets, turbofans, turboprops, turboshafts and propfans: they also include ramjets, rocket engines and even electric motors. These aviation engines have different working principles, but except for electric motors, they generally work externally through combustion, converting the chemical energy in the fuel into mechanical energy output. Next, let us delve into the world of aviation engines and simply get to know these elegant machines that represent human wisdom.
The family of piston engines
The piston engine is a typical internal combustion engine. As the name suggests, it works by exploding fuel inside the cylinder and pushing the piston to work. The first practical four-stroke engine was invented by German engineer Otto in 1876 based on the research of his predecessors. In order to commemorate his great creation, people in later generations named the cycle process of the four-stroke ignition piston engine the Otto cycle.
The Otto cycle mainly includes four links: intake, compression, combustion and exhaust. First, the piston installed on the crankshaft moves down from the highest point to near the lowest point, and the aerosol fuel and air are sucked into the cylinder through the intake valve; then the intake valve is closed, the piston moves upward to compress the mixed gas, and the pressure and temperature in the cylinder increase; when the piston runs to near the highest point, the mixed gas is ignited, and the high-temperature and high-pressure gas rapidly expands in the cylinder to do work, pushing the piston down to near the lowest point; finally, as the exhaust valve opens, the piston returns from the lowest point to the highest point, and the exhaust gas is discharged from the cylinder. In 1897, another German engineer, Diesel, further invented a diesel internal combustion engine that does not require spark plug ignition and generates high-temperature ignition fuel by rapidly compressing gas. His name was also used by later generations to name the cycle process of the compression ignition engine.
In 1903, the Wright brothers installed an 8.8-kilowatt water-cooled gasoline engine on the world’s first aircraft, the Flyer One, and successfully flew it off the ground. World War I and World War II greatly promoted the development of aviation piston engines, giving birth to improved designs such as sodium-filled cooling exhaust valves, cylinder water injection system fuel direct injection system, and power recovery turbine. The most important of these is the widespread use of superchargers, which can make the cylinder intake pressure higher than the atmospheric pressure at the location, thereby greatly improving the efficiency and high-altitude performance of the piston engine.
According to the different cylinder arrangements, aviation piston engines can be roughly divided into two categories: in-line and star-shaped arrangements. The cylinders of an in-line engine are staggered on both sides of a crankshaft. The front area of the engine is small but the length is long. Therefore, it is widely used in land-based fighters that pursue faster flight speeds and smaller missile-damaged areas. The cylinders of a star-shaped engine are evenly distributed on the circumference, and the relatively short crankshaft is located at the center of the circle. Cylinders are usually arranged in one row, but in some high-power engines, they can be designed in multiple rows to increase the number of cylinders. This type of engine has a large front area but a short length. It mostly adopts a simple and reliable air-cooled design, relying on high-speed airflow during flight and cooling fins on the cylinders for cooling. This type of engine is often used in bombers and transport aircraft that pursue higher take-off weights, as well as carrier-based aircraft that pursue higher reliability and smaller fuselage sizes.
The piston propeller aircraft that are still in production today are mostly small aircraft or drones. Piston engines are more than enough for these aircraft. Compared with turboprop engines, they have the advantages of low cost, simple maintenance, and fast operational response.
Turbine engine family
Unlike piston engines that use gas in the cylinder to drive the piston to reciprocate, the turbine engines used in the aviation industry use gas to drive the turbine to rotate continuously to generate power. This is the case with turboprop, turbofan, turbojet, turboshaft and propfan engines commonly used in modern large and medium-sized aircraft and helicopters, as well as gas turbines used in some vehicles, ships and power stations.
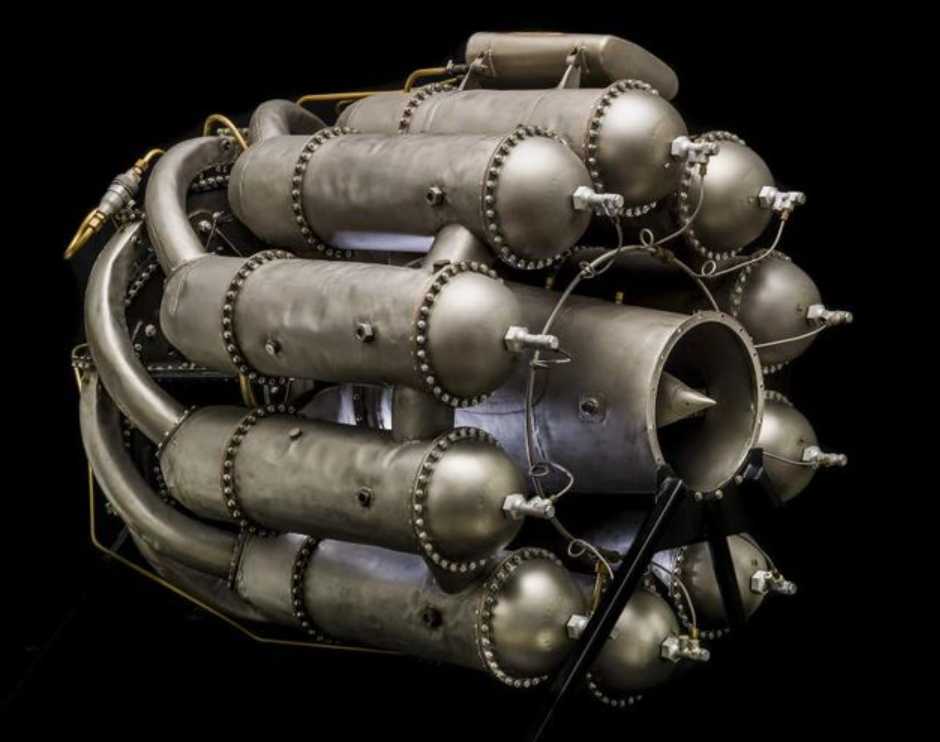
Various gas turbine engines contain three core components: a coaxially mounted compressor, a power turbine, and a combustion chamber between the two. First, a large amount of air is adiabatically compressed by the compressor, enters the combustion chamber and mixes with the fuel mist before being ignited, thereby producing high-temperature and high-pressure gas. These gases adiabatically expand and work, driving the power turbine to rotate at high speed, which in turn provides power for the compressor, thereby achieving continuous operation. This cycle is called the "Brayton cycle", and the core engine is the whole composed of the "three major components". If various power output components are further added to it, various types of turbine engines belonging to the same series are born. Compared with piston engines, turbine engines have higher thermal efficiency and higher power-to-weight ratio at high power, and are more adaptable to fuel and have less operating vibration.
If the power turbine is only used to drive the compressor, and the exhaust gas with high pressure and temperature is directly ejected backward at high speed, a turbojet engine is created. This engine can directly provide thrust for the aircraft. Compared with traditional propeller power, it has stronger power and higher efficiency under high-altitude and high-speed conditions. In order to further increase the thrust of the turbojet engine, improve the acceleration performance of the aircraft and break the "sound barrier", an afterburner can be installed after the final turbine. The fuel nozzle directly sprays oil mist into the high-temperature gas and is ignited by the igniter to generate additional thrust, but this device consumes a lot of fuel and should not be turned on for a long time.
The first practical turbojet engine was successfully manufactured by British Air Force Major Whittle in 1937. The aircraft used a centrifugal compressor. In 1938, the German Ohain successfully manufactured the world’s first turbojet engine HeS3 using an axial compressor. The latter was installed on a Heinkel He-178 aircraft and successfully flew into the blue sky on August 27, 1939. The aircraft became the first turbojet-powered aircraft in history. In 1944, the Messerschmitt Me-262 developed by the Germans became the first practical jet fighter. It used two Junkers Jumo 004B turbojet engines and proved the powerful performance of jet power in the subsequent war.
After the war, the United States, the Soviet Union and other countries obtained a large amount of information on turbojet engines by purchasing patents, reverse engineering and dividing the technological heritage of Nazi Germany. On this basis, they developed various turbojet engines with more powerful performance and installed them on aircraft for various purposes. As a result, the aviation industry basically entered the jet age.
In order to improve the compression ratio of the compressor and thus improve the engine performance, the impellers of multiple compressors can be connected in series, which is particularly common in axial flow compressors. However, the optimal operating speeds of compressor impellers at different levels are not the same. For this reason, engineers designed a concentric double-layer main shaft: the inner slender main shaft connects the low-pressure compressor impeller and the low-pressure stage turbine to form a low-speed low-pressure rotor, and the outer thicker and shorter main shaft connects the high-pressure compressor impeller and the high-pressure stage turbine to form a high-speed high-pressure rotor. This structure of the engine was first mass-produced by the American Pratt & Whitney Company (hereinafter referred to as "Pratt & Whitney") and installed on the J57 (the civilian version is the JT-3C ) turbojet engine. In order to make full use of the internal energy of exhaust gas, improve fuel efficiency and engine thrust, engineers installed more turbines on the basis of turbojet engine and directly connected the main shaft and ducted fan, and invented the turbofan engine. Compared with turbojet engine, turbofan engine can make more full use of the internal energy of exhaust gas and convert it into additional thrust, so it has greater thrust and better fuel economy. However, under high-altitude and high-speed working conditions, due to the thin atmosphere and the air resistance of the fan itself, the thrust of the turbofan engine is greatly attenuated.
The world’s first practical turbofan engine was the "Conway" engine launched by Rolls-Royce in the 1950s. The engine was successively installed on VC-10, Boeing 707, Douglas DC-8 and other models. Today’s turbofan engine is advancing in two technical routes: military engines with small bypass ratio and afterburner and civil aviation engines with large bypass ratio: Pratt & Whitney’s F135 military engine designed for the F-35 fighter, the latest improved version has a thrust of up to 200 kN or more, and the GE-9X designed by General Electric for the Boeing 777-9X passenger aircraft has created an amazing record of 579.4 kN in the test.
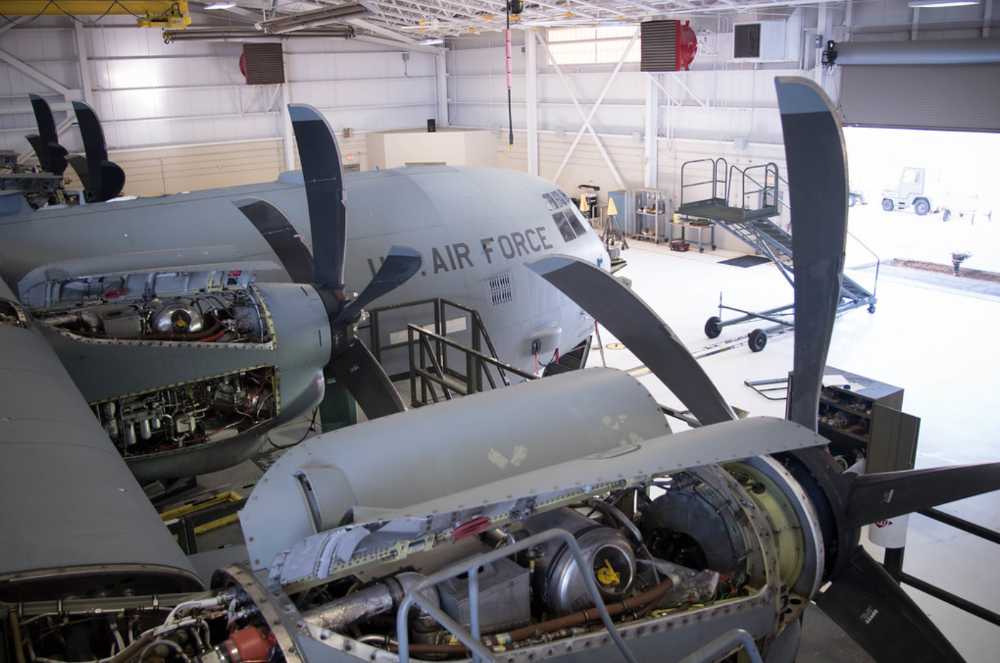
On the basis of the twin-rotor turbofan engine, the intermediate pressure compressor impeller, intermediate pressure turbine and corresponding intermediate main shaft can be further added to form a three-rotor structure to further improve the working efficiency of the engine. The first mass-produced three-rotor aircraft engine was the RB211 turbofan engine produced by Rolls-Royce in the United Kingdom. The development process of the engine was very bumpy. It was finally put into commercial operation for the first time in 1972 with the Lockheed L-1011 passenger aircraft. The famous Trent series turbofan engine is the RB211 The direct descendant of the propfan engine.
On the basis of the turbofan engine, the main fan is replaced with multiple wide-chord, thin-bladed swept propeller blades, which is the basic principle of the propfan engine. This engine can not only propel the aircraft to cruise at high subsonic speeds like a turbofan engine, but also has higher fuel efficiency in theory. Therefore, it was deeply studied by Europe, the United States and the Soviet Union from the 1970s to the 1990s. Because the propfan engine’s blades rotate very fast and often do not have the same duct protection structure as the turbofan engine, this engine not only has a very high working noise, but also when the blade breaks, the fragments are more likely to penetrate the fuselage skin, causing serious safety problems. These two fatal defects have greatly limited the application of propfan engines. In addition to the above-mentioned gas turbine engines that directly eject high-speed airflow, engineers have also created turboprop engines, gas turbines and turboshaft engines by connecting the turbine main shaft to the generator, propeller reducer or helicopter rotor reducer.
The world’s first turboprop engine, CS-1, was invented by Hungarian engineer Jacob Jandraske in 1937. The theoretical power of the engine reached 294 kilowatts. Unfortunately, the outbreak of World War II interrupted the development process and the engine was not actually installed on the aircraft. Compared with traditional piston engines, turboprop engines have the advantages of high power and good high-altitude performance, and better fuel economy than turbojet engines. Therefore, this engine has been widely used in large aircraft after World War II. One of the most representative models is the NK12 engine developed by the Soviet Union in the 1950s. This engine has extremely high output power and uses huge counter-rotating propellers. It is used in the Tu-95 strategic bomber and the An-22 strategic transport aircraft. The improved version has a power of an astonishing 11,186 kilowatts, which has not been surpassed by other turboprop engines so far.
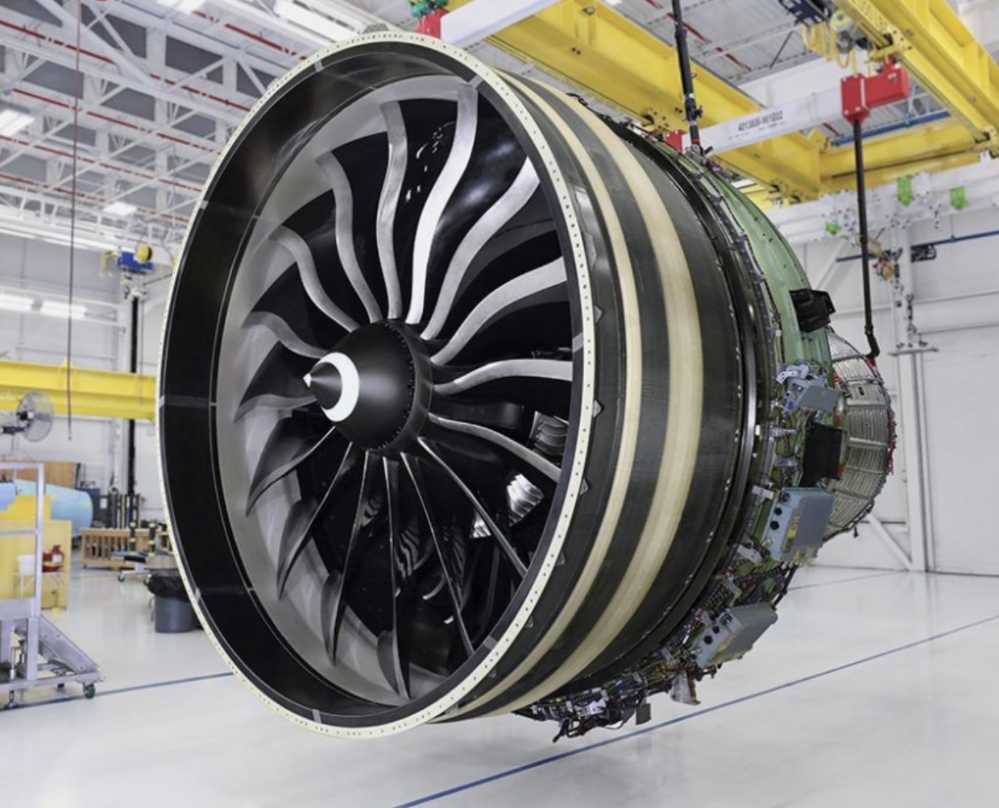
The world’s first practical turboshaft engine was invented by the French company Turbomeca: In 1950, the company’s Agusta| turboshaft engine was successfully installed and flew for the first time. Since then, more and more helicopters have begun to use this powerful, compact and lightweight engine.
Turbine engines provide a strong, efficient and reliable power source for these machines and facilities. A series of advanced technologies such as gear-driven turbofan engines, adaptive variable cycle turbofan engines, carbon fiber composite fans, new ceramic composite turbine casings, 3D printed fuel injectors and intelligent control technology for fuel mixers are also expected to be put into use in the near future.
Pulse engines, ramjets and electric propulsion technologies
The well-known aviation jet engines generally refer to turbojet engines and turbofan engines, but in fact, there are two other engines with simpler structures that also belong to this category, namely pulse engines and ramjet engines.
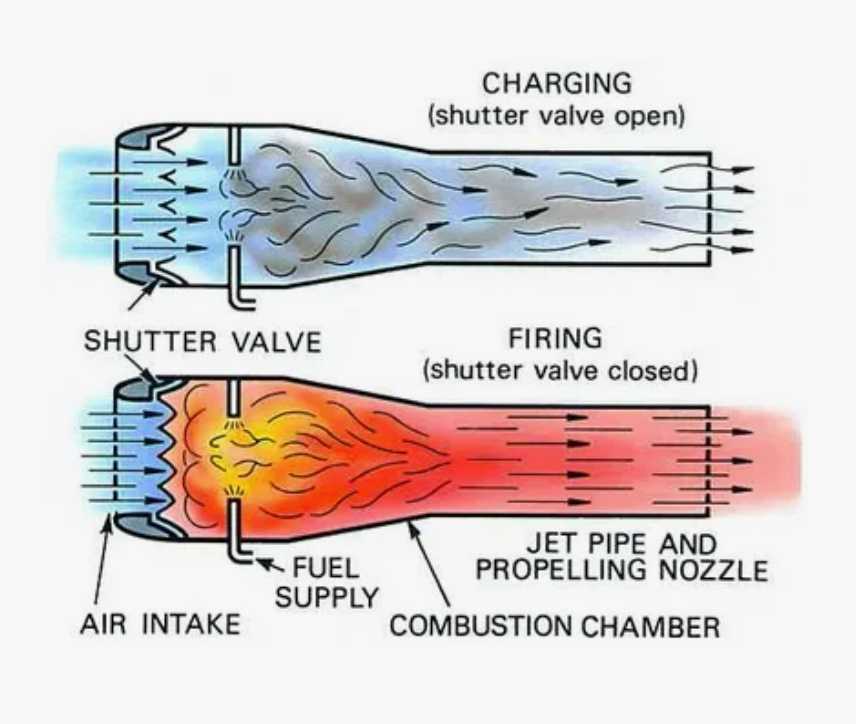
The main component of a pulse engine is just a pipe with a one-way valve installed inside, a fuel injector installed in the front section of the valve, and a spark plug installed in the combustion chamber after the valve. When working, the air first enters the fuel injector section, mixes with the oil mist to form a combustible gas and enters the combustion chamber along the opening direction of the one-way valve. Then the spark plug ignites, and the high-temperature and high-pressure gas generated by the deflagration pushes the one-way valve to close, and is ejected backward from the nozzle at high speed, generating a forward reverse thrust. Due to the internal waves and gas inertia, the air pressure in the combustion chamber will be lower than the atmosphere, and new air is sucked into the engine to achieve continuous operation. Although this engine is inefficient, noisy and vibrating, it is widely used in model aircraft, target aircraft and even missiles due to its simple structure and low cost. In fact, the V1 cruise missile that Nazi Germany first put into actual combat in 1944 used this type of engine.
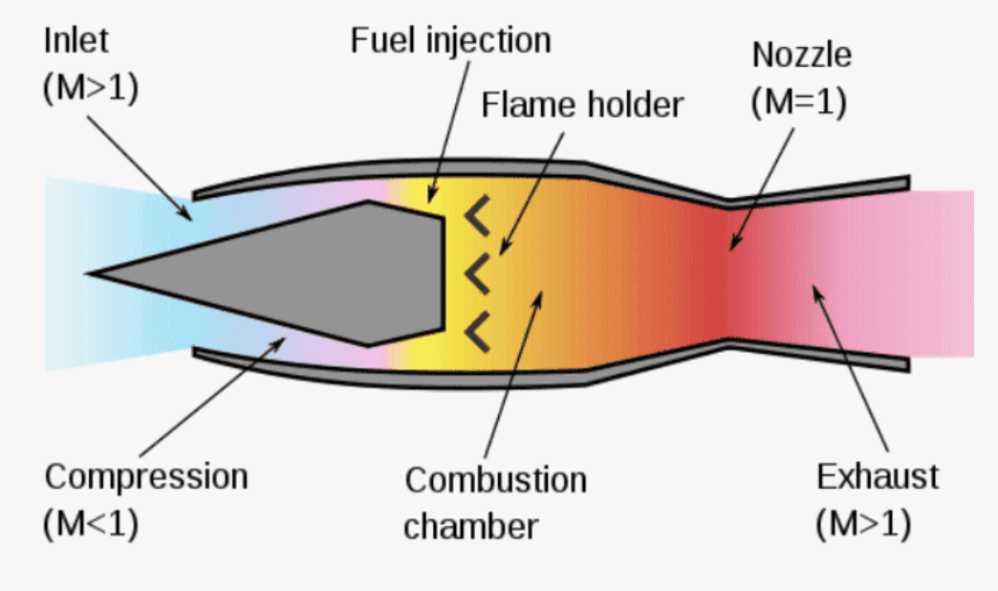
The structure of the ramjet engine is simpler, consisting of only a combustion chamber and a special air intake and nozzle. When flying at high speed, the ramjet airflow reduces the flow rate and increases the air pressure through the cleverly designed air intake, and air compression can be achieved without a compressor. Subsequently, the high-pressure airflow enters the combustion chamber and is mixed with the fuel and ignited. The high-temperature and high-pressure gas is decompressed and accelerated in the nozzle and ejected backward, generating a forward reverse thrust. The biggest disadvantage of the ramjet engine is that it cannot work at rest and at low speed, so it often requires a rocket or other power source to give it a certain initial velocity before it can operate normally. Compared with other traditional aircraft engines, ramjet engines have incomparable advantages such as simple structure, light weight, and small size, and can be used for disposable aircraft such as missiles and target drones. Of course, the most cutting-edge and well-known use of this engine is as a power source for hypersonic vehicles in the atmosphere, because it does not need to carry oxidizers like rocket engines, is more efficient, and is easy to reuse.
The electric drive system widely used in road vehicles, electric locomotives and EMUs can also be installed on aircraft as aviation power. In recent years, with the rapid development of high-power motors, battery technology and high-voltage electric control technology, as well as the pursuit of zero carbon emissions in environmental protection, more and more manufacturers have begun to try this.
From 1903 to 2023, after 120 years of development, aviation engines have become quite mature, and they provide solid power guarantee for the research and development and application of various aircraft. In the future, aviation engines will develop in a safer, more reliable, smarter and more environmentally friendly direction, promote the emergence and evolution of more aircraft with different purposes, and provide a more solid guarantee for economic construction and national defense security.