Modern aircraft engines are known as the "crown jewel of industry", or perhaps the "diamond of the crown" is more appropriate. Because of its "three highs" harsh working environment of high temperature, high pressure and high-speed rotation, it is intuitively felt that only a diamond-like temperament can persist in working for a long time. Among all kinds of weapons and equipment, aircraft engines are most dependent on materials and manufacturing technologies. The harsh operating conditions of high speed and high temperature of aircraft engines and the working requirements of long life and high reliability have pushed the requirements for materials and manufacturing technologies to the limit. The development of materials and process technologies has promoted the replacement of engines. For example, the main structural parts of the first and second generation engines are all made of metal materials, the third generation engines began to use composite materials, and the fourth generation engines widely used composite materials and advanced process technologies, which fully reflected the characteristics of a new generation of materials and a new generation of engines.
The technical indicators of aircraft engines are moving towards high temperature, high pressure ratio, high Reliability is developing, and its structure is moving towards lightweight, integration, and composite. Improving the overall performance of the engine depends half on materials.
Cornerstone--Nickel-based high-temperature alloys
High-temperature alloys have high comprehensive properties such as high temperature resistance, fatigue resistance, and fracture toughness resistance. They are widely used in aviation, aerospace, petroleum, chemical industry, ships, etc., especially in the engine field
A notable feature of advanced aircraft engines is that the working environment temperature of the turbine is very high. Increasing the temperature before the turbine is one of the important means to increase the thrust of the engine. One of the conditions that determine the temperature before the turbine is the high temperature resistance level of the turbine blades, so to some extent, the material determines the performance of the engine.
In various advanced engines currently in service, nickel-based high-temperature alloys are used in large quantities, and their usage accounts for 10% of the total weight of the engine. 55%-65%. Therefore, high-temperature alloys are also known as the "cornerstone of modern aircraft engines." Among them, single-crystal nickel-based high-temperature alloys are widely used to manufacture turbine blades, guide blades, inner and outer rings of blades, nozzle fan segments, etc. Since the first generation of single-crystal alloys were used in the JT9D-7R4 engine in the United States in 1982, the production volume of single-crystal blades has exceeded millions. In 1989, the second generation of single crystals was used in the Pratt & Whitney PW2037 engine. The third generation of single crystal alloys is currently widely used in the engines of wide-body aircraft such as Boeing 777 aircraft and A330. The latest fourth-generation single crystal high-temperature alloy was first developed by GE, Pratt & Whitney and NASA, and is currently also being used in engineering. With each generation of single-crystal alloys, its heat resistance increases by about 30°C. The maximum operating temperature of the second-generation single-crystal turbine blades is about 1170℃, and the third generation has exceeded 1200℃.
Thanks to the excellent performance of high-temperature alloys, engineers want to apply them to many parts of aircraft engines, but they still encounter difficulties in the processing of large-scale parts. Therefore, powder high-temperature alloys were introduced into the field of aircraft engine manufacturing. The use of high-temperature alloys prepared by powder metallurgy is similar to that of partially aging-strengthened high-temperature alloys, and is mainly used for disc-shaft forgings in aircraft engines. The preparation of high-temperature alloys by powder metallurgy technology is a revolutionary technological breakthrough in this field. With the continuous increase in part size and the increasing complexity of high-temperature alloy composition, powder metallurgy high-temperature alloys have shown more advantages.
Perfect material-titanium alloy
Compared with high-temperature alloys, titanium alloys have low density and high strength, so they are called the perfect material of light weight and strength. At the same time, the corrosion resistance and wide operating temperature range of titanium alloys make them very suitable for the design requirements of aircraft engines. The working temperature range of titanium alloy can range from about 20℃ at the air inlet to nearly 600℃. In 1954, Pratt & Whitney of the United States began to use titanium alloy in the compressor parts of the J57 engine. Today, the use of titanium alloy in advanced engines is second only to high-temperature alloys, accounting for 25%-40% of the total weight of the engine, which plays a key role in reducing engine weight and improving thrust-to-weight ratio.
Advanced aircraft engines mainly refer to the fourth-generation and new-generation military turbofan/turboshaft engines with higher thrust-to-weight ratio/power-to-weight ratio, as well as the new-generation high-bypass turbofan engines for trunk airliners. In addition to having higher performance indicators, these advanced engines must also fully meet the requirements of reliability, safety, economy, airworthiness, and environmental protection. New development requirements for materials and processes have been put forward, mainly including:
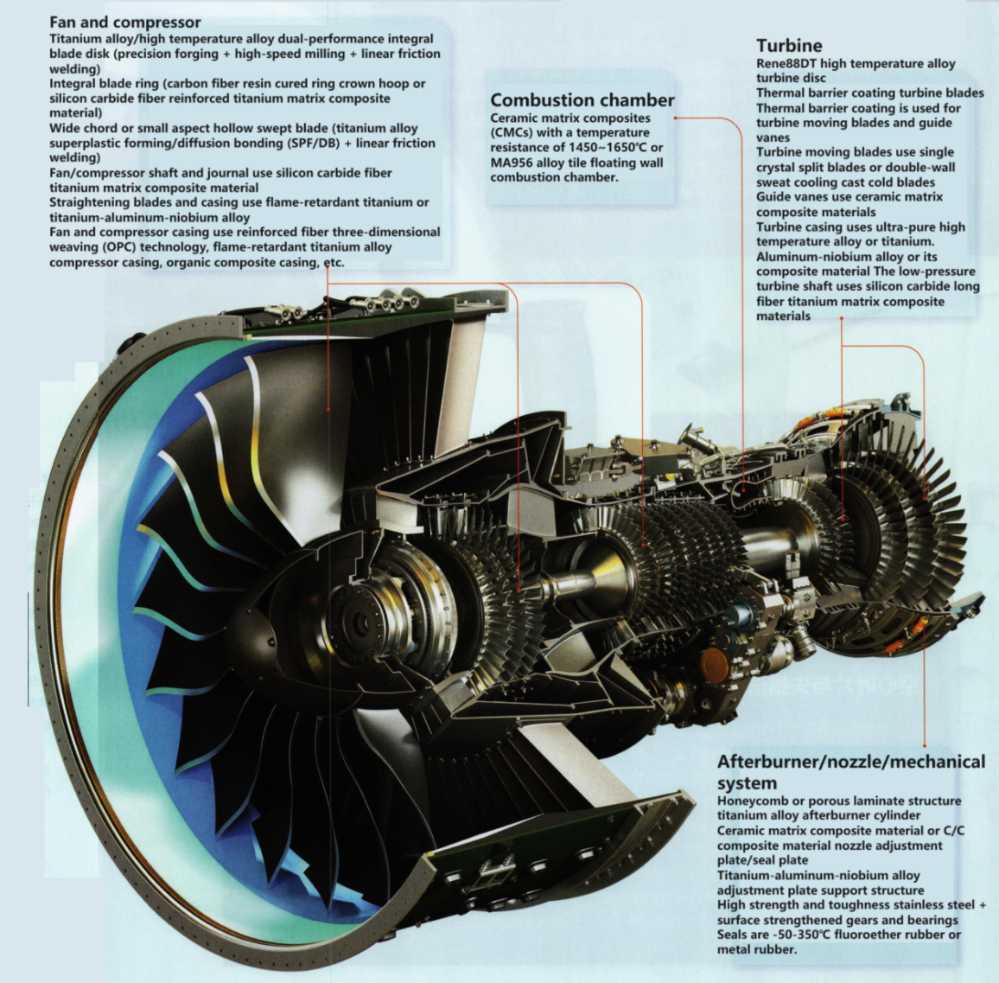
The stacked blades and blades in the engine turbine are key components of aircraft engines. In the early 1940s, the first generation of turbojet engines used stainless steel blades with an operating temperature of about 700-750℃. As the aviation industry’s demand for thrust continues to rise, the materials and structures of turbine blades have been continuously adjusted and improved, and the operating temperature has gradually increased to above 1000℃.
To rotate at high speed in a temperature environment of 1000℃, and at the same time be squeezed by forces from all directions, the blades can confidently say that they work in the worst environment. Moreover, the designers are not satisfied with this working temperature and are deliberately trying to increase the temperature again.
The working position of the turbine blade is located behind the combustion chamber. The temperature of the gas before it enters the turbine after it is ejected from the combustion chamber is called the "turbine pre-temperature". The thrust of an aircraft engine is closely related to the turbine pre-temperature. For every 100K increase in temperature, the thrust increases by 15%. Therefore, this places high demands on the high temperature resistance of the turbine blades. In addition, while the turbine blades are subjected to high temperatures, they are also subject to centrifugal overload caused by high-speed rotation. Therefore, among the many systems and components of aircraft engines, turbine blades have become the most severe working conditions and the most difficult to develop. Their performance determines the thrust of the engine.
The turbine blades that have been in service for a long time in the harsh environment of high temperature, high pressure and high speed are the first key parts of engine manufacturing. The temperature bearing capacity of the turbine blades determines the thrust of the entire engine.
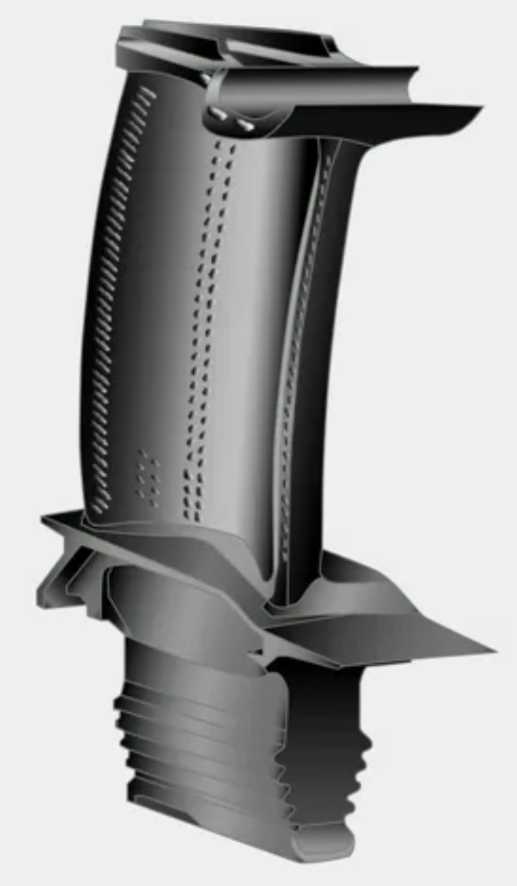
Hollow blades and lost wax method
To improve the temperature bearing capacity of turbine blades, there are two main direct paths: one is to explore high-temperature alloys with better performance, and the other is to improve the cooling system of the blades. At present, due to the physical limitations of the melting point of metals, it is becoming increasingly difficult to break through the heat resistance temperature of alloys. Engineers have begun to look for breakthroughs in heat dissipation and heat protection and improved cooling systems. Improving the cooling system means passing cold air through the blades to cool them down. It is called efficient air cooling technology. In order to improve the cooling efficiency, engineers have achieved a large degree of cooling by making the blades hollow and constructing complex cooling pipes in the hollow cavity. At the same time, the hollow design can also greatly reduce the weight, which can be said to kill two birds with one stone!
Complex hollow blades are difficult to manufacture by traditional machining and forging, but a clever method is adopted. The investment casting process of hollow engine blades is to make a ceramic core, which is the inner cavity of the hollow blade, and then wrap a layer of wax outside the core to accurately replicate the shape of the blade, and then coat several layers of refractory material, which is the shell, outside the wax: then remove the wax, inject the molten metal, and remove the core and shell after cooling to obtain the hollow blade.
Thermal barrier coating
As the operating temperature and environmental conditions of the engine become more and more severe, the two direct paths of high temperature resistance and cooling have basically been explored to the extreme. Designers feel that it is far from enough to only aim at self-improvement and improvement, and they have to find another way. When people encounter temperature changes, cold or hot, they will adjust their body temperature by adding or removing clothes. So can the engine do the same? In fact, most of the various parts inside the engine are coated with coatings with certain functions, such as anti-oxidation and anti-corrosion coatings laid on the inner cavity, wear-resistant coatings to prevent excessive wear of the blade tip on the inner cavity, and sealing coatings to fill small gaps. What coating can protect the blades from "melting" under ultra-high temperature conditions? The scientific name of this protective layer is called thermal barrier coating, which is a ceramic material with excellent thermal insulation properties.
In more than half a century of research and development, high-temperature protective coatings have undergone several iterations, from the first generation of aluminide coatings, the second generation of modified aluminide coatings, to the third generation of coatings, and now the fourth generation of thermal barrier coatings has been developed.
Thermal barrier coatings are formed by depositing and bonding a layer of material with a low heat transfer coefficient on the surface of the part, using its low heat transfer characteristics to form a temperature difference between the inner and outer surfaces of the part, thereby reducing the working temperature of the part surface. Data show that thermal barrier coatings can achieve a cooling effect of 50K to 150K. Thermal barrier coatings can not only reduce the surface temperature of the blades, but also reduce the damage to the internal tissues of the blades caused by work fatigue.
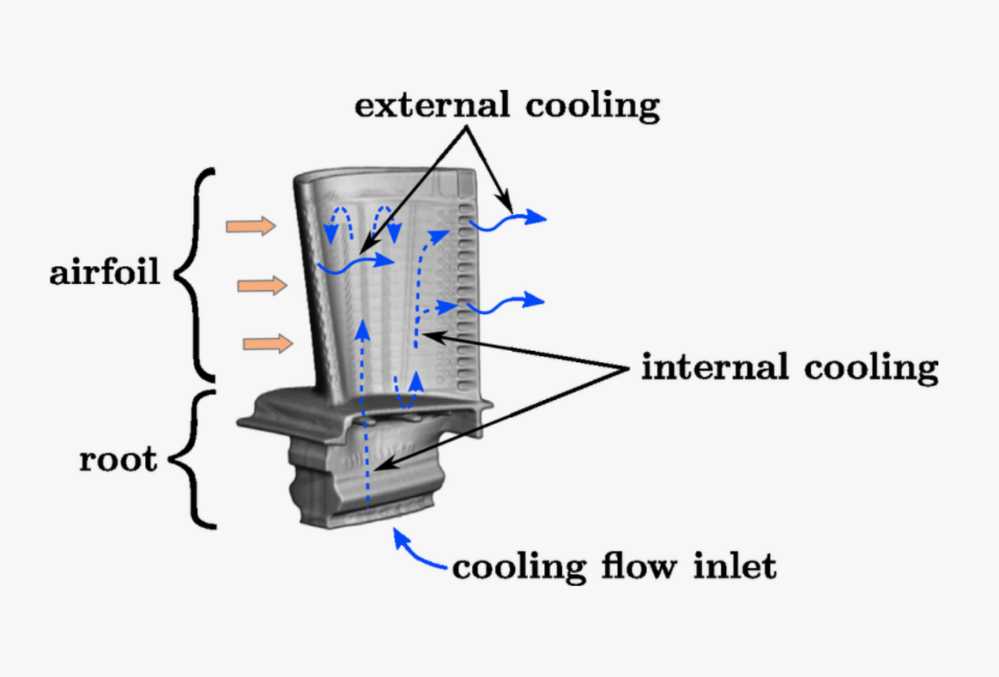
Currently, thermal barrier coatings actually used in turbine engines are two-layer structures: the outer ceramic layer mainly plays a role in heat preservation, and also plays a role in corrosion resistance, scouring and erosion; the inner metal bonding layer mainly plays a role in improving the physical compatibility between the metal matrix and the ceramic layer, and enhancing the high-temperature oxidation resistance of the coating. The design concept of advanced materials is "the advantages of each material complement and promote each other". Therefore, the concept of thermal barrier coatings is to take into account the excellent high temperature resistance and low thermal conductivity of ceramic materials. It should be noted that this is very consistent with the purpose of high temperature protective coatings to resist high temperature oxidation. However, due to its poor toughness and inability to adhere well to the surface (low bonding strength), it is necessary to add a layer of "adhesive" (metal bonding layer) between the ceramic layer and the substrate surface, thus forming a double-layer structural system of ceramic layer-metal bonding layer-substrate alloy from the outside to the inside.
The preparation of thermal barrier coatings is not simply stacking one layer on top of another, but refining the material for preparing the coating into particles with a diameter of micrometers, and then coating these particles on the surface of the material with extremely high energy. After years of practical research, the more commonly used method is to inject certain gases that meet the use conditions into the electrode cavity, and heat the gas through arc heating to thermally ionize it into a balanced mixture of electrons and ions to form plasma. The temperature of the plasma is very high and it is in a highly compressed state, which forms an extremely high energy source. This high energy is then used to carry the particles to the surface of the material, which is plasma spraying.
In engineering technology, the practice of temperature resistance is endless.