When you approach your beloved car, the car’s Bluetooth system senses the electronic key in your pocket, and the car automatically unlocks with a "click". You sit in the driver’s seat elegantly and gently press the "START/STOP" button. An electronic signal is sent to the EEC--electronic ignition and engine control computer at a speed of milliseconds. The EEC evaluates the information input from the engine and environmental sensors hundreds of times per second to ensure that the engine operates in the optimal efficiency range. Sensors deployed in various locations will monitor the health of the engine in real time. If a problem is detected, it will be displayed on the front dashboard or the central control screen.
Like cars, modern civil aircraft also use similar electronic control methods. Not only does it improve reliability, but it can also optimize fuel efficiency and earn more profits for airlines. Of course, modern aircraft engines are much more complex than car engines. Therefore, in order to manage the start and stop operation of the engine more safely and efficiently, engineers need to "transfer" some authority from the pilot to the computer. This is the most powerful brain of modern aviation engines - FADEC, the full authority digital engine control system.
FADEC can control the engine to operate in the optimal efficiency range in real time according to the speed and altitude planned by the aircraft brain - the flight management computer (FMS) combined with the atmospheric temperature, humidity, aircraft attitude, weight and other information obtained by the environmental sensor, and can detect sudden changes in the external environment at a rate of more than 70 times per second. For example, when the aircraft enters the cloud layer, the atmospheric density changes, heavy rain, or encounters wind shear, it can quickly and accurately adjust the engine’s fuel injection, adjustable stator blade angle, bleed valve and other components, dynamically adjust the engine thrust, and ensure the safe flight of the aircraft. Just like the ABS anti-lock braking system of a car, when the vehicle slips, the driver only needs to step on the brake, the ABS system will automatically activate, detect the grip of each tire in real time, and independently control the brakes of each tire. All this does not require and cannot be intervened by the driver.
For a long time at the beginning of the birth of aircraft, the control system of aircraft engines was not so complicated. The original piston-powered propeller aircraft adjusted the engine thrust completely by the throttle lever in the hands of the pilot. Pushing the throttle, the speed increased, and closing the throttle, the speed decreased. The principle is exactly the same as stepping on the throttle when driving a car. But frequently controlling the engine thrust by retracting and releasing the throttle is both troublesome and uneconomical. How to keep the piston engine in the most efficient speed range while controlling the propeller thrust? British aviation engineer Leslie Everett Baines proposed a solution for propeller torque conversion in 1921. After starting the engine, the thrust size is achieved by the pilot manipulating the torque converter. Of course, the pilot can still adjust the engine speed, or output power, by retracting and releasing the throttle, and cooperate with the torque converter to obtain the best fuel efficiency and power response in different flight environments.
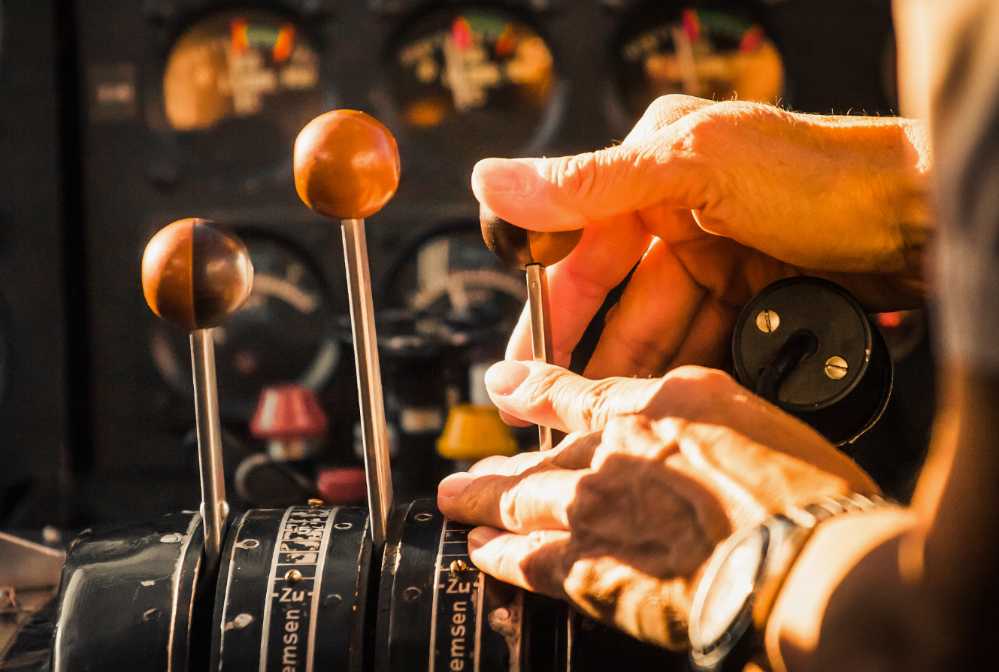
With the development of technology, the control of aircraft engines has become more and more complicated. Throttle, torque, speed, oil-gas mixture ratio, carburetor temperature, fuel tank selection, etc. All engine controls are connected to the engine through hydraulic mechanical means. Aircraft before the 1950s mainly used piston propeller engines. Although the control system was complicated, it could barely be operated by one or two pilots. In the 1950s, turbojet engines began to become the standard for high-performance aircraft, but the difficulty of operation increased significantly, especially for large military and civilian aircraft equipped with 4 or more turbo engines. One or more air mechanics are required to monitor or even independently control the various indicators of the engine and other aircraft systems.
In the late 1950s, analog electronic signal technology developed rapidly, and the integrated control of aircraft engines gradually entered the hydraulic mechanical + analog control. The aircraft cockpit, including the engine control console, was full of large and small instruments and red and green indicator lights. At this time, aircraft engines have gradually entered the jet age, and pilots need to monitor more and more engine parameters, such as fuel pump pressure, temperature, lubricating oil temperature, turbine case cooling valve opening and closing! High and low pressure rotor speed, etc., and fuel pumps have several types such as plunger pumps and centrifugal pumps. Pilots can monitor the information of each important system and change the electrical signal through switches and knobs to convey the expected settings to the engine. Although analog control is better than hydraulic mechanical control, its disadvantages are also obvious, such as common electronic noise interference and reliability problems.
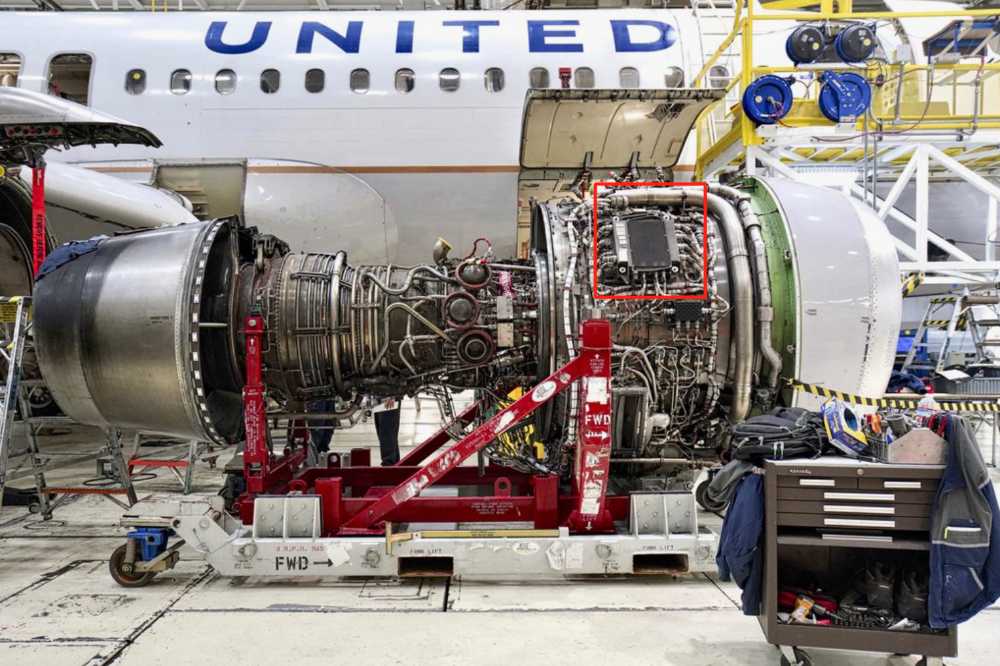
In the pursuit of higher and faster aviation, engineers will certainly not be satisfied with the current configuration. In the 1960s, humans had successfully entered space and were working tirelessly towards a more distant goal-the moon. While serving the Cold War arms race, electronic computer technology also began to be quietly applied in the aviation field. In order to achieve supersonic flight, the Concorde aircraft adopted a fly-by-wire flight control system, becoming the world’s first commercial passenger aircraft to adopt a hydraulic + fly-by-wire avionics system, although this fly-by-wire is still an analog signal. In order to allow the four Olympus 593 turbojet engines to have stable performance in transonic flight, the engine design team developed the world’s first analog signal fly-by-wire thrust control system for it. This system is interconnected with the aircraft’s fly-by-wire flight control system and is regarded as the prototype of today’s FADEC.
In the late 1960s, the digital control system FADEC began to enter the historical stage. In 1968, Rolls-Royce and Elliott Automation jointly established the Gas Turbine Research Institute, developed a digital engine control system, and completed hundreds of hours of testing on a Rolls-Royce Olympus Mk 320. In the late 1970s, NASA and Pratt & Whitney began testing the first experimental digital FADEC system, installing it on a highly modified Pratt & Whitney TF30 engine and testing it on an F-111 bomber. Subsequently, Pratt & Whitney tested FADEC on the F100 and PW2000 engines for more than 1 million flight hours, with a failure-free interval exceeding 20,000 hours, and reliability far exceeding initial expectations. This test made the F100 and the HP PW2000 the first military and civilian engines equipped with FADEC, respectively. Subsequently, FADEC began to be widely used in military and civilian engines of major engine manufacturers around the world. In order to further improve reliability, in 1984, Pratt & Whitney installed two sets of FADEC for the PW4000 high bypass ratio turbofan engine, making it the world’s first commercial engine to adopt the "dual FADEC" system. Time has come to the 21st century. Today, in the field of aviation manufacturing, we often see the term "fly-engine integration". The so-called "fly-engine integration design" refers to the cross-linking design between the engine and the aircraft structure and system. The aircraft designed in this way will have better flight performance and more economical fuel efficiency. However, due to the increasing demand for the number of sensors, the weight of engine cables, wiring, sensors and actuators in the engine control system accounts for a large proportion. The future engine control system will adopt fiber-optic communication and distributed control systems, and the existing hydraulic mechanical actuators will tend to be simple, reliable and universal. The development of microelectronics technology will also reduce the size of the FADEC system while giving it more powerful computing power. As aircraft communication systems tend to use a bus, the FADEC system will be a node on the bus. Combined with the application of new sensors and actuator structures, the system reliability will be further improved.
The military aviation engine field has a higher demand for FADEC systems. Future engines will not only have fuel control and variable geometry control, but also anti-surge control, thrust vector nozzle control and other functions. At the same time, engine control must be integrated with the engine status monitoring system, and must also be cross-linked with the flight control system and fire control system. The FADEC system enables the engine to achieve different control modes, complex control plans, adaptive control, performance optimization control and various advanced control laws and algorithms within the full envelope, and will also greatly accelerate the development of the engine integrated control system.
If the aircraft is likened to a continuously evolving species, FADEC is the "sub-brain" that grows from nothing to something, from weak to strong, on the "aircraft evolution" according to local needs (power system). With the continuous evolution, in the future, this "sub-brain" will be gradually absorbed and become part of the "main brain", escorting flight safety in a more intelligent and integrated form.