As the only superpower in the world, the United States announced a batch of defense R&D contracts on August 19, 2022. Among them, the most prominent ones are the "Next Generation Adaptive Propulsion Program" (NGAP) R&D contracts awarded to General Electric, Pratt & Whitney, Boeing, Lockheed Martin and Northrop Grumman, which clearly require them to be used for future air superiority platforms. The generous terms of the contract are jaw-dropping. The funds are capped at US$975 million. There are no specific engine delivery quantities and deadlines, but the R&D work must be completed before July 11, 2032. This shows that the US military has decided to adopt "adaptive engines" on the next generation of fighter jets. Interestingly, the "adaptive engine" or "variable cycle engine" is not a new thing. Its concept appeared as early as the 1960s. The exploration of related theories and technologies in the aviation industry can even be traced back to the time when the jet engine just appeared before the concept of "variable cycle engine" was proposed.
The first variable cycle engine - Pratt & Whitney J58 with external assistance
In 1959, a year before Powers was shot down by the Soviet Union in the U-2 reconnaissance plane, the US Air Force and the Central Intelligence Agency learned that the Soviet Union had been equipped with surface-to-air missiles. They had a premonition that it was only a matter of time before the U-2 broke its wings, and they urgently needed the next generation of high-altitude and high-speed reconnaissance aircraft to take over. This new model later evolved into the SR-71 "Blackbird", and its development work was again handed over to Lockheed, the developer of the U-2, and undertaken by Kelly Johnson, the director of the "Skunk Works". After Johnson failed in his early attempts at liquid hydrogen-powered engines, he finally chose the Pratt & Whitney J58 engine. The J58 was originally designed for the Navy’s Martin P6M The turbojet engine developed for the four-engine seaplane jet bomber uses an 8-stage compressor and a 2-stage turbine with an afterburner. With the cancellation of the P6M project, the J58 was also abandoned by the Navy.
Pratt & Whitney has completely transformed the J58, redesigned the compressor using nickel-based high-temperature alloys, and ingeniously added 6 bypass air ducts directly to the afterburner at the 4th stage of the compressor. In addition, the SR-71’s engine nacelle also adopts a special design. The air inlet, the regulating cone, the front and rear air flow bypass valves of the air inlet, and the nozzle together with the J58 engine itself form a complex and ingenious "propulsion system". Through the adjustment of the engine’s peripheral components, the engine’s cyclic working state is changed.
As the speed increases, the afterburner of the J58 draws more and more compressor 4th stage air from the 6 bypass air ducts, and the proportion of thrust provided by the engine becomes smaller and smaller. When the flight speed reaches At Mach 3.2, the huge pressure difference before and after the intake cone provides 54% of the thrust; the engine itself only provides 17%; and the thrust provided by the nozzle is more than the engine body, reaching 29%! At this time, the "Blackbird" can be said to be pushed by the engine nacelle!
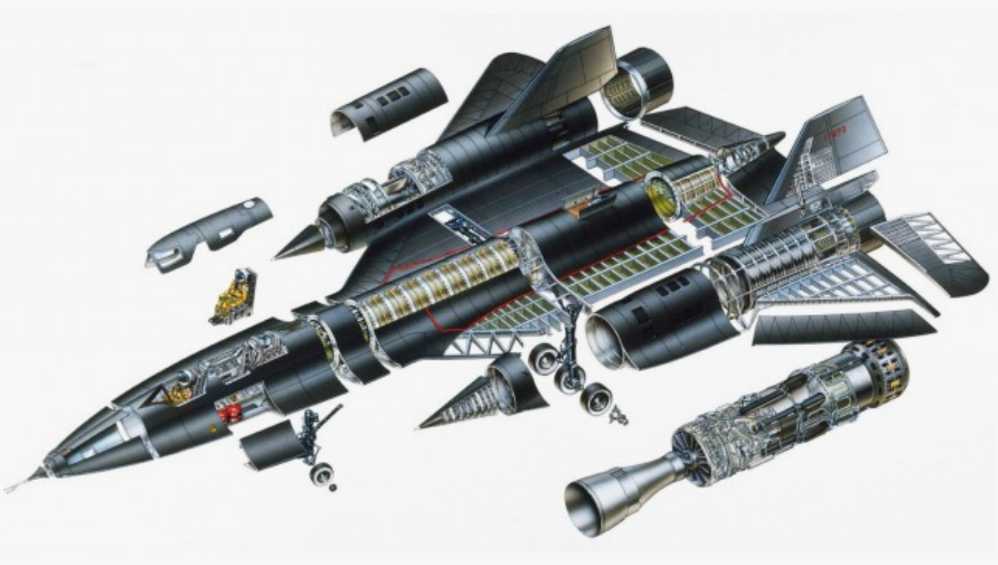
In order to keep the fuel stable under the high temperature of aerodynamic heating and avoid self-ignition before being injected into the combustion chamber for ignition, the J58 chose a low-volatility, high-molecular-weight JP-7 mixed fuel with a boiling point of more than 280 degrees Celsius. Its formula is still highly confidential. Johnson’s favorite student participated in the design of Ben Rich, who worked on the SR-71’s propulsion system, described it in his book Skunk Works: "Strike a match, throw in a bucket of JP-7, the JP-7 won’t light, the match goes out." Conventional jet engine ignition nozzles cannot ignite such inert JP-7, and triethylborane, a dangerous chemical that can spontaneously ignite in air at room temperature, needs to be injected into the combustion chamber at the same time to help with combustion. Therefore, every time the SR-71 is refueled, the relevant personnel must be fully armed and wear protective clothing. Although the J58 achieved a terrifying afterburner thrust of 150 kilonewtons as early as the late 1950s, even from the technical perspective of the time, the J58 is still an outdated engine, with a total weight of more than 2.7 tons, a thrust-to-weight ratio of only 5.23, and a total pressure ratio of only 8.8; the "magic modified bypass air duct does not have any adjustment and control accessories, and it relies entirely on the specially designed engine compartment and special fuel to carry it; when the flight speed exceeds the speed of sound, the pilot almost has to monitor and manually adjust the various components of the "propulsion system" without taking care of other things. Only when it reaches Mach 3.2 supercruise can he breathe a sigh of relief, because at this time there is nothing to adjust... These restrictions mean that the J58 is not a true variable cycle engine and can only be used in highly specialized The variable cycle engine that can be truly applied to the main military aircraft on the SR-71 "Blackbird" strategic reconnaissance aircraft has to be developed from scratch.
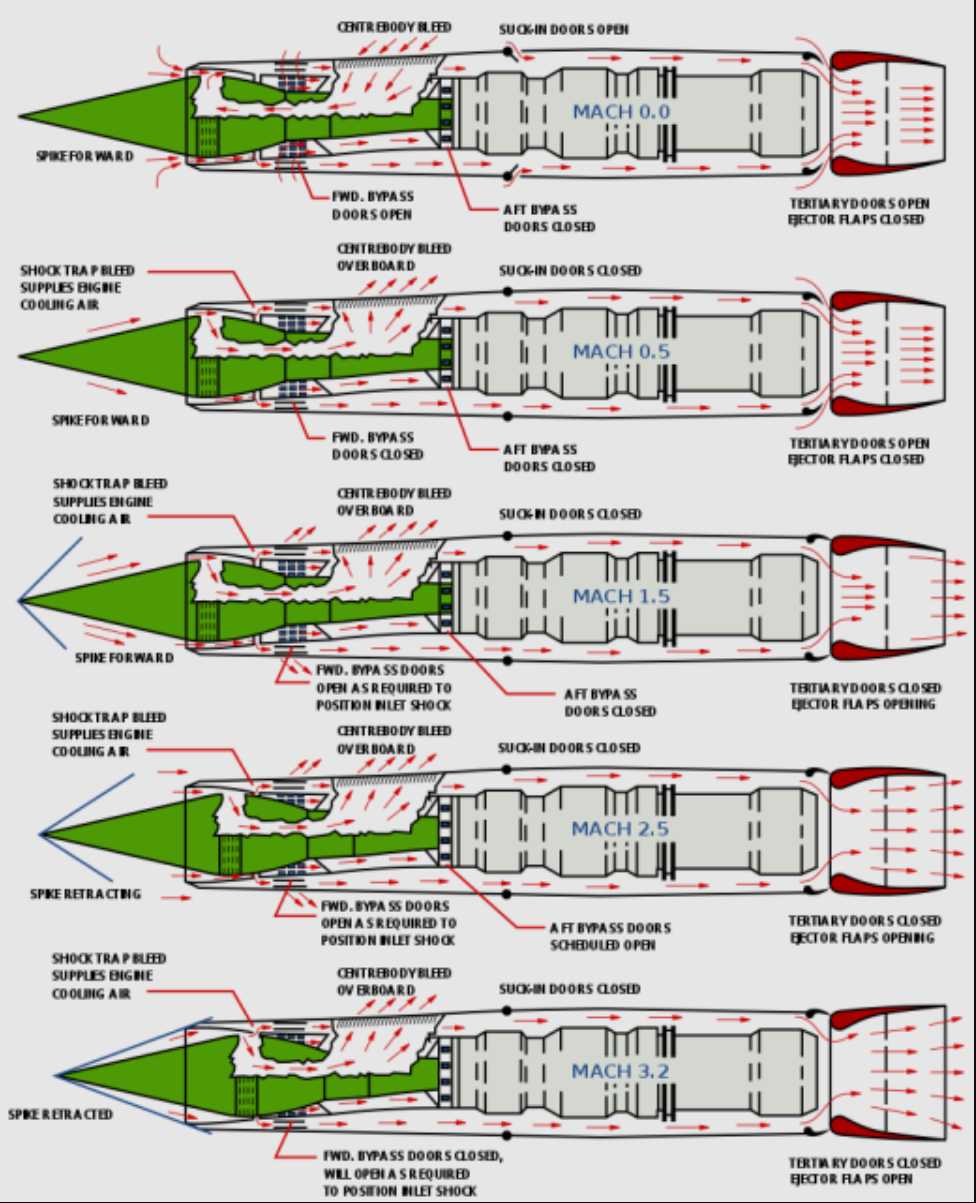
The development of variable cycle - from YJ101 to GE21
In the late 1940s, jet engines had just become practical. The aviation industry generally recognizes that the thermal cycle characteristics of conventional engines are fixed and can only achieve optimal performance within a certain speed and altitude range. With the expansion of the flight envelope, the speed is getting faster and the altitude is getting higher, and the contradiction between low-speed fuel saving and high-speed high thrust cannot be taken into account. More and more prominent. In addition to using the air intake adjustment system to make limited adjustments to the compressor intake, military aircraft can only make some choices in engine design according to actual needs. It is not uncommon for aircraft to be scrapped due to engine development failures.
As early as In 1944, the National Advisory Committee for Aeronautics (NACA) found that by adjusting the angle of the compressor casing stator vanes, the total pressure ratio can be significantly increased without much increase in speed, thereby improving the compressor efficiency of the turbojet engine. Based on this conclusion, General Electric decided to focus on the development of the "variable stator compressor" VSC technology in 1950, which was expected to increase the total pressure ratio of the new engine to 12:1, which was a very amazing number. At that time, the total pressure ratio of the General Electric J47 engine, which had just been put into service, was only 5.25. The reason why General Electric has such confidence is that the company has a noble person, the German genius designer Gerhard Neumann.
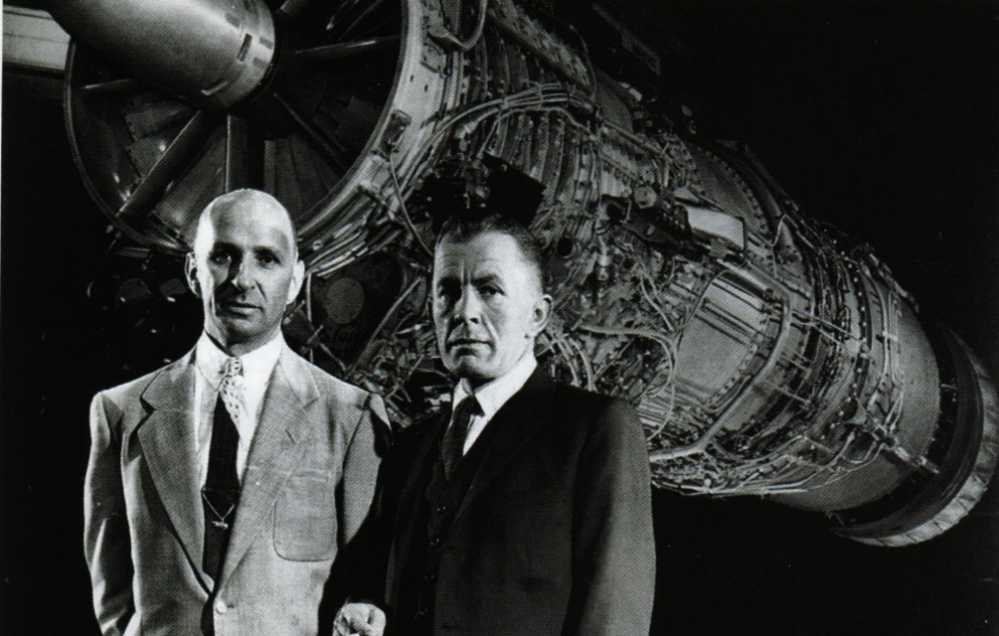
As a Jew, Neumann was born in 1938. He fled Germany in 1940 and joined the "Flying Tigers" during his exile in China. He became famous for successfully repairing a captured Zero fighter. After World War II, Neumann became a naturalized American citizen and joined General Electric in March 1948. Three years later, he became the leader of General Electric’s aeroengine research and development team. In 1955, he successfully developed the J79 turbojet engine with variable inlet guide vanes and a 6-stage variable stator structure, with a total pressure ratio of up to 13.5. The engine was produced for 30 years, with a total output of more than 17,000 units. It was widely used by the second-generation fighters of the United States, such as the F-4 and F-104. It can be said that it single-handedly supported the sky of the second-generation aircraft of the US military.
Since 1961, Neumann has served as the deputy director of General Electric’s aeroengine business. Under his leadership, General Electric rose rapidly and eventually competed with Pratt & Whitney in the field of commercial and military jet engines. At this time, the emergence of turbofan engines marked the beginning of a new stage in the technological development of aeroengines.
Based on the successful experience of J79, Neumann proposed the concept of "variable cycle engine". On the basis of conventional turbofan engine, by changing the position of some components, changing some key indicators of engine thermal cycle, such as bypass ratio, air flow, total pressure ratio, etc., the thermal cycle mode of the engine is changed, so that it can be in the best state in a larger speed/altitude range, so as to make the carrier aircraft obtain ideal performance.
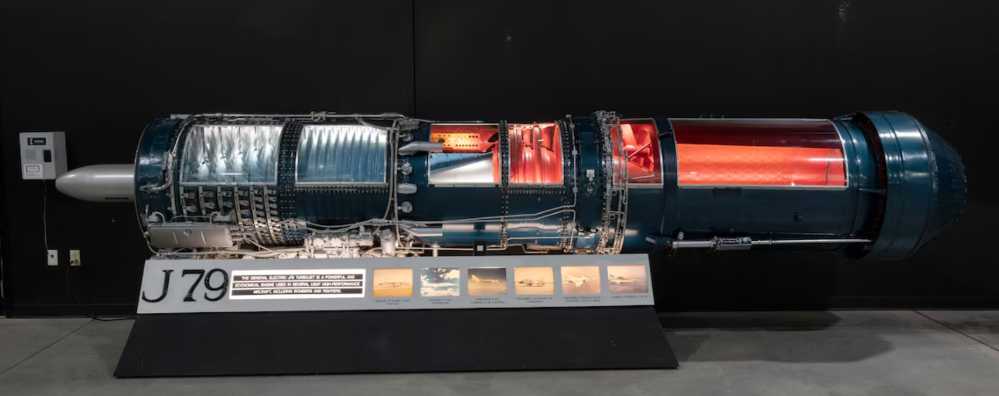
J79TECHNICAL NOTES:
Model: J79-GE-15 Compressor: 17-stage axial Turbine: three-stage axial Maximum takeoff: 17,000 lbs. thrust (with afterburner) Military power rating: 10,900 lbs. Weight: 3,850 lbs. Length: 17 ft. 5 in. Diameter: 3 ft. 2 in.
Specifically, the adjustable stator of the J79 was greatly modified, moved from the core engine casing of the turbofan engine to the fan duct, and the deflection angle of the blades was increased to control the air flow in the duct. This mechanism was called the "Adjustable Area Duct Injector (VABI). This idea eventually evolved into the YJ101 turbofan engine, which was used to match the Northrop YF-17 fighter jet that bid for the 1971 "Light Fighter Program" (LWF).
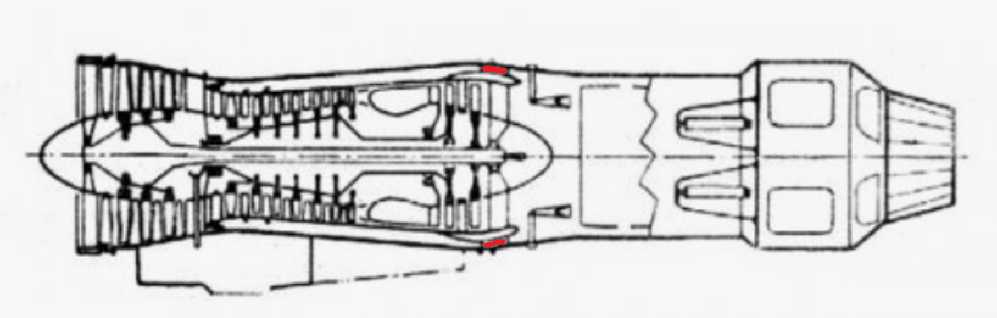
The biggest feature of the YJ101 is the so-called "continuous bypass exhaust structure", adding a VABI (red part in the figure on the next page) in the fan outer duct in front of the afterburner, and adding several stages of exhaust valves outside the compressor of the core engine. At low speeds, the VABI and exhaust valves open at larger angles to increase the flow of the outer duct; at high speeds, the VABI and exhaust valves open at smaller angles to increase the amount of core air. At this time, the engine runs in a turbojet state. The small amount of airflow in the outer duct does not provide thrust, but is only used to cool the casing and afterburner. This engine is therefore called "the world’s first self-cooling turbojet engine". Due to its slightly rudimentary design, the YJ101 is often jokingly called a "turbojet engine with continuous air leakage". Soon General Electric launched the second-generation variable cycle engine based on the YJ101, the more complex GE21. GE21 abandoned the compressor exhaust valve of YJ101, and instead added a high-pressure fan (CDFS) driven by the core engine between the original low-pressure fan and the compressor, connecting the low-pressure outer duct of the low-pressure fan through a short high-pressure inner duct, forming a unique "double-rotor double-duct" configuration. The airflow control between the inner and outer ducts is achieved by adding a set of VABIs - in other words, GE21 is simply a nesting doll with a large duct inside a small duct, and the small duct connected to the core engine. According to the design, GE21 will open both ducts during subsonic flight, reducing fuel consumption by 15% compared to conventional turbofan engines; at supersonic speeds, it is similar to YJ101, with the front and rear VABIs all closed, and the airflow of the low-pressure fan, except for a very small amount flowing through the outer duct to cool the engine and nozzle, is all sent to the core engine to obtain greater thrust with a turbojet configuration. After continuous improvement, GE21 evolved into GE23, GE33 and GE37. GE37 is the predecessor of the famous "king of failure" YF120.
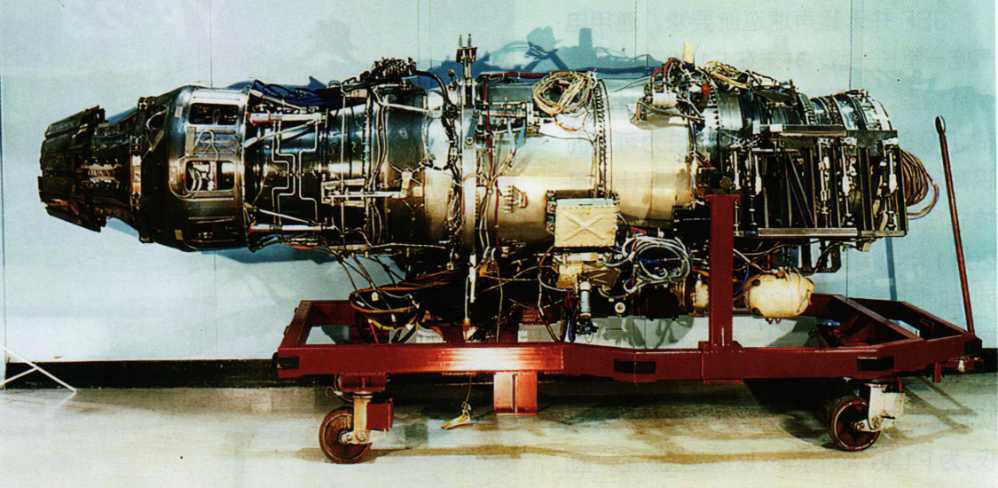
Variable cycle engine put into practical use - although failed, the glorious YF120
In 1977, when the Cold War was at its peak, a U.S. spy satellite discovered two unidentified fighter jets with a completely new aerodynamic layout at the Raminskoye test base (now Zhukovsky Airport) in the southeastern suburbs of Moscow. They were given the code names "Ramin-K" and "Ramin-L", which later became the Su-27 and MiG-29. This showed that the Soviet Union was catching up in the field of third-generation fighter jets, narrowing the gap with the United States and even having the possibility of overtaking it.
In response, in June 1981, the U.S. Air Force issued a tender for the Advanced Tactical Fighter (ATF) to replace the F-15, which had just been put into service. As a fourth-generation aircraft, the ATF clearly requires the ability to cruise at supersonic speeds, which means that the engine used with it needs to have a stronger thrust.
ATF also focuses on requiring the fuselage and engine to have higher reliability and maintainability, because the U.S. Air Force was struggling with the engine at that time. In order to reduce the logistical burden, both the F-15 and F-16 use the Pratt & Whitney F100 turbofan engine. The F100 unilaterally pursues high indicators, but frequently breaks out serious defects such as flameout in the air, compressor surge, and blade breakage. The attendance rate of the twin-engine F-15 was once only 20%, while the single-engine F-16 crashed an average of three every two months... The desperate U.S. Air Force cooperated with General Electric to develop the F110, which has greater thrust and is more reliable. The result of this famous "engine war" was a win-win for all three parties. Pratt & Whitney was forced to improve its design, GE gained market share, the U.S. Air Force got a satisfactory engine, and avoided the situation where one company dominated the market and bullied its customers.
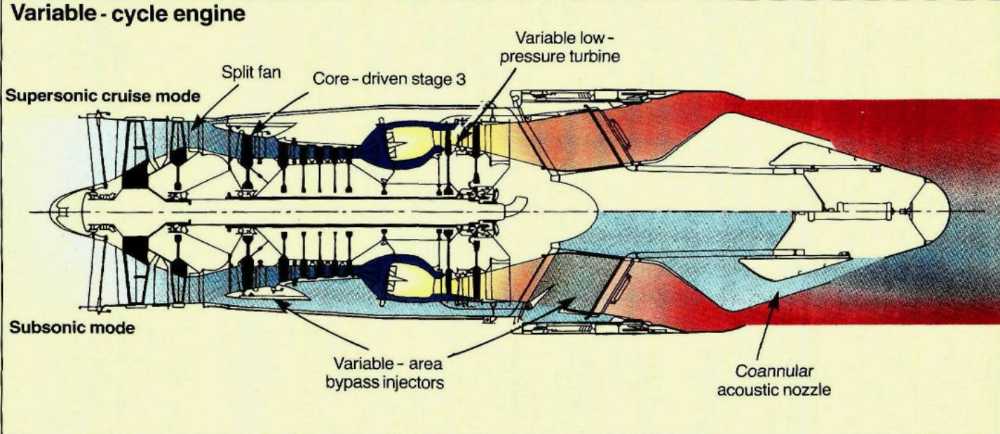
In order to suppress its old enemy Pratt & Whitney again, GE once again used its ancestral variable cycle skills in the development of the ATF engine. The XF120, codenamed GE37 within the company, further optimized the original variable cycle layout and simplified the front VAB mechanism of GE21 to a passive bypass valve. When the turbofan mode switches to a turbojet, the VABI after closing down causes the outer duct pressure to increase, forcing the passive bypass valve to close without manual or engine control system intervention. Although the variable cycle system increases the number of parts, GE also uses integrated turbine disc technology in the fan and compressor, which greatly reduces the number of engine parts, even 40% less than its own F110! As the ATF project progresses, the total weight of the aircraft has soared from 22.7 tons to 27.2 tons, and the corresponding engine thrust has to increase by 20%, from 133 kN to 156 kN. After the XF120 prototype successfully passed the ground bench test, GE enlarged the fan size by 12% to increase the thrust, and the new engine YF120 soon showed obvious performance advantages. The No. 1 YF-22 equipped with the YF120 flew at a supercruise speed of Mach 1.58, while the No. 2 equipped with the Pratt & Whitney YF-119 could only fly to Mach 1.43. Similarly, the No. 1 YF-23 equipped with the YF119 could only fly to Mach 1.43 supercruise, while the No. 2 YF120 could reach Mach 1.6.
Although the YF120 was quite powerful, the US Air Force tended to be conservative and chose the Pratt & Whitney YF119. The YF119 had one more fan and one more compressor than the YF120, and used titanium alloy blades, defeating the more technologically sophisticated YF120 with a simple and crude stacking method
After the ATF dust settled, the United States proposed the Joint Advanced Strike Technology (JAST) in the early 1990s, which evolved into the Joint Strike Fighter (JSF), which is now the F-35 fighter. The F135 engine used by the F-35 is actually a modified and enhanced version of the F119, and the US Air Force, in view of the lessons learned from the last "engine war", entrusted General Electric to develop the F136 as a backup.
JSF does not require supersonic cruise. GE learned from its mistakes and did not use the variable cycle configuration on the F136. Instead, it simplified the design of the YF120, re-used the J79’s static stator structure, improved it to an adjustable area high-pressure turbine guide vane, and designed the F136 into a conventional turbofan engine with a controllable total pressure ratio. The project had completed 80% of its progress by 2011, and 6 prototypes had been tested for 1,200 hours in two years. However, the US Congress ordered the project to be terminated at this time for a simple reason: "no money." In order to prevent the F135 from causing the F-35 fleet to be grounded due to problems, the Obama administration even had to use the presidential veto to forcibly extend the life of the F136. This American version of the "dispute between the government and the legislature" ended with Congress winning.
It is quite ironic that Pratt & Whitney has returned to its old ways on the F135, and the failures are still repeated, but this time the F-35 has no spare engines to replace. Two "engine wars" within 30 years, but the results are completely opposite. As the Western sage Hegel said, "Historical events will happen twice, the first time is a drama, and the second time is a farce." So the ancients are not deceiving us!
Adaptive engine debut-XA100/101
In 2007, the US Air Force and the Navy jointly launched the "Adaptive Multifunctional Engine Technology" (ADVENT) program to develop adaptive variable cycle engines. The program evolved into the "Adaptive Engine Transition" (AETP) program in 2016, aiming to develop adaptive engines for the sixth-generation fighter and replace the F135 turbofan engines of the existing F-35 fleet. AETP requires a 25% reduction in fuel consumption and a 10% increase in thrust (reaching more than 200 kN) on the basis of the current F135.
Under strict confidentiality, General Electric completed the preliminary test of the XA100 adaptive engine prototype in May 2021, and it is expected to be put into practical use as early as 2027. At present, General Electric has revealed very little information about the XA100. In addition to the use of a 3-stage adaptive fan and the extensive use of ceramic and polymer materials, there is only one airflow distribution demonstration diagram. The XA100 still retains the three airflows of the outer duct-inner duct-core engine commonly used in general variable cycle engines, and uses a 7-stage compressor, a 2-stage high-pressure turbine and a 2-stage low-pressure turbine.
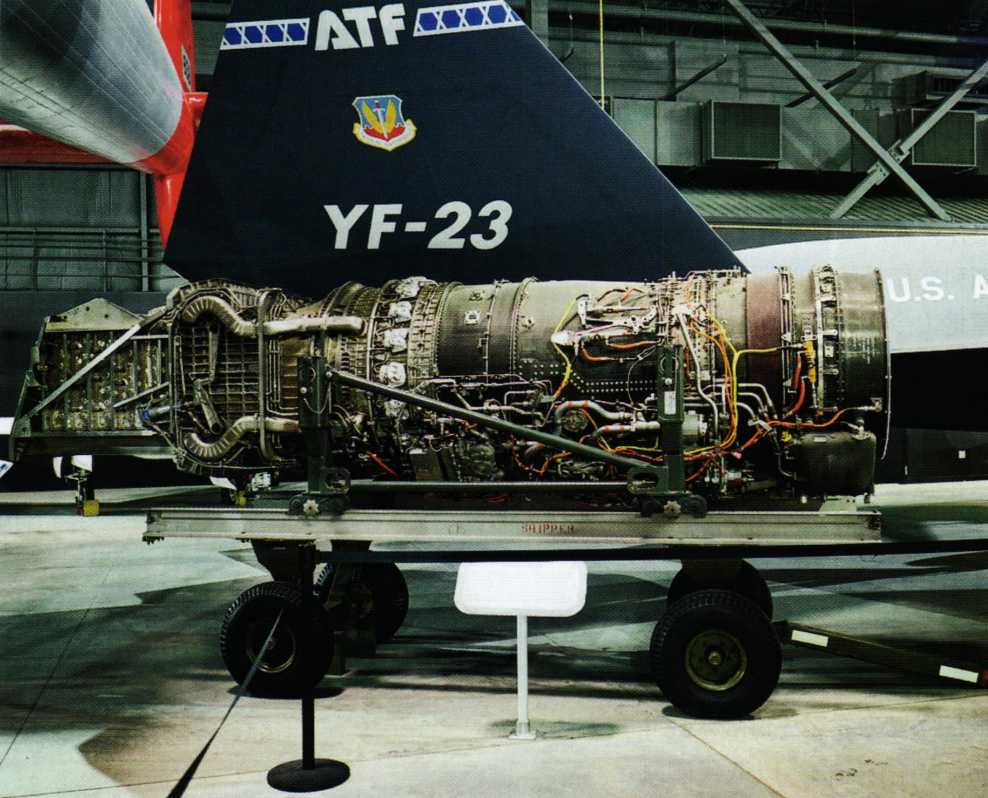
General Electric’s old enemy Pratt & Whitney also participated in the AETP program, and its XA101 engine prototype also completed ground testing in the second half of 2021. The only known information at present is that the XA101 also uses three-stream airflow distribution. As for other further information, it is also "commercial confidential, no comment" like General Electric.
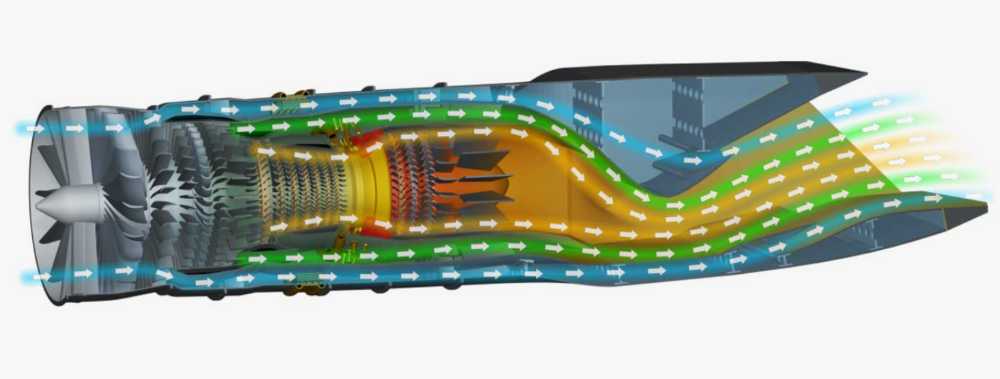
In addition to the engine body, the high intelligence of the sixth-generation aircraft means that the flight, engine and fire must be linked. When the pilot changes the flight attitude through the flight control system, the engine control system and the fire control system react quickly to adjust their respective working states like the human nervous system. The full authority digital electronic control system (FADEC) used in the third-generation aircraft is obviously no longer sufficient, and the control system of the adaptive engine will inevitably undergo earth-shaking changes.
It is not difficult to understand that in the five R&D contracts released by the United States, in addition to the two major engine manufacturers General Electric and Pratt & Whitney, there are also three major OEMs, Boeing, Lockheed Martin and Northrop Grumman. To some extent, the OEM responsible for realizing the whole machine flight and fire linkage has a more difficult R&D than the engine manufacturer.
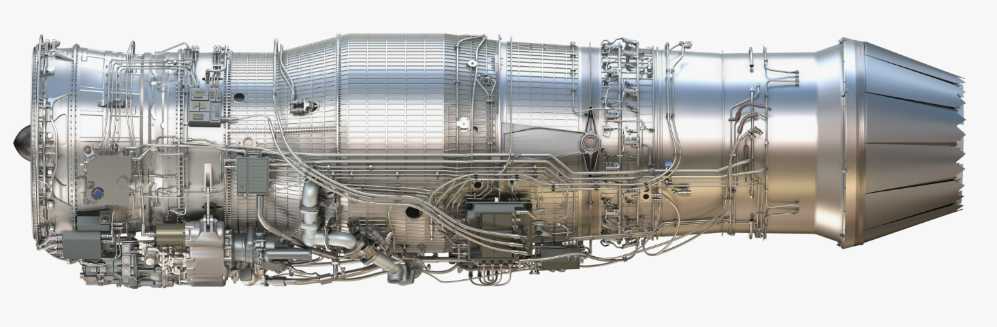
General Electric once designed the so-called "TBCC" engine for hypersonic aircraft based on YF120, which greatly expanded its variable cycle working range and can work in a ramjet mode at high speed like Pratt & Whitney J58. It is estimated that at an altitude of 17,000 meters, it only takes 8 minutes to accelerate from 0 to Mach 4.1. It can be seen that adaptive engines are not only an inevitable trend in the development of military high-performance fighters, but also in the future hypersonic/aerospace aircraft field, adaptive engines will also have great development space.