This year’s Singapore Air Show showcased two tankers, one is the multi-purpose A330MRTT, and the other is the veteran KC-135 tanker with a service history of 70 years. Because this tanker is too large, visitors can only watch its entire appearance from a distance, or get close to the aircraft to take a close-up photo, or walk under the shade of this KC-135 tanker. In addition to the "big" feeling of this tanker, the author also has a more than ten-meter-long hard pipe refueling device. It is hard to imagine that this is a tanker from the 1950s. It is really shocking.
Let’s talk about the KC-135 tanker first
The KC-135 tanker came out in the early 1950s and was put into service with the US Air Force in 1956. It was developed by Boeing and was originally designed to meet the US Air Force’s demand for aerial refueling capabilities. The aircraft was originally planned for civilian use, but due to its excellent airframe performance and large-capacity fuel tank, the US Air Force began to use it as an aerial refueling aircraft to complete the task of refueling fighter jets in the air. The KC-135 is based on the improvement of the civil airliner 707. It utilizes the advanced technology of similar aircraft and adds an aerial refueling system to the design, making it the world’s first aircraft dedicated to aerial refueling. Its flexibility and versatility make it a milestone in the field of military aviation and lay the foundation for the subsequent development of military refueling aircraft. In terms of fuselage design, the KC-135 adopts a conventional layout. The fuselage is made of aluminum alloy, with a cantilevered swept lower wing and a normally arranged cantilevered tail. The vertical tail length of the first 582 aircraft was short. In order to improve the stability of the take-off length, the aircraft produced thereafter increased the height of the vertical tail. There is an integral fuel tank between the wing spars of the aircraft, and other fuel tanks are located in the bottom cabin of the fuselage. The bag fuel tank in the bottom cabin of the fuselage is made of nylon fiber. One weighs only 36 kg and can hold nearly 7,000 kg of fuel. A telescopic pipe is installed under the rear fuselage. After the aircraft improved by the multi-point refueling system project, a hose drogue refueling pod can be hung under each wing. The aircraft can refuel aircraft of various types in the air at night and under complex weather conditions, and the refueling speed can reach 2948 kg/minute.
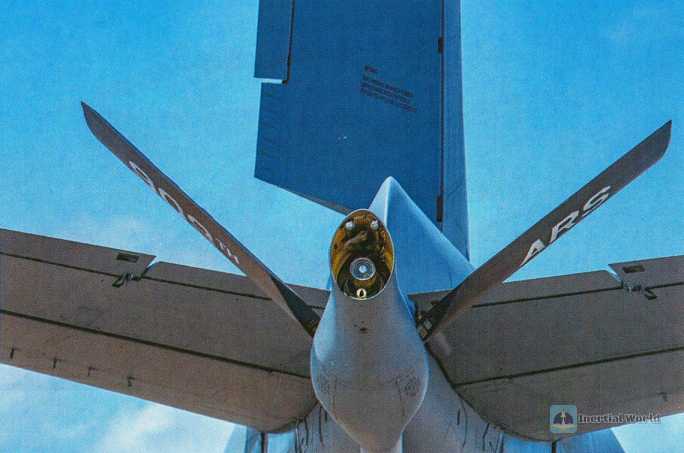
The crew consists of 4 people: the pilot, the co-pilot, the navigator and the refueling operator. The co-pilot is responsible for operating the fuel system. The refueling operation cabin is located in a fairing under the rear fuselage. The refueling operator sits forward in a tilted position to facilitate observation of the refueling pipe and the receiving aircraft. The cargo hold has no portholes and can carry both people and goods. For example, it can carry 6 463-liter pallets, 376 kg of cargo or 80 passengers. The personnel/cargo transportation capacity varies depending on the fuel load.
The KC-135 aerial refueling aircraft has a 35-degree sweep angle on its main wing. It is equipped with four jet engines under the wing. Initially, it used J57-P-59W turbojet engines, with a single thrust of 6,236 kg and a total thrust of 24,944 kg. The fuselage can be divided into two parts, upper and lower. The upper part is generally used as a cargo hold, and the lower part is almost entirely a fuel tank. A large cargo door is configured on the port side of the cargo hold. The rear section of the fuselage is the refueling operation area. Taking the KC-135E as an example, it can carry about 227,500 pounds of fuel, and the cargo hold can carry up to 83,000 pounds of cargo. There are four to five crew members in total: the pilot, co-pilot, navigator and aerial refueling operator. There is usually a fifth crew member observer on board. The task of the refueling operator is to complete the communication and docking between the tanker and the receiving aircraft and control the refueling volume.
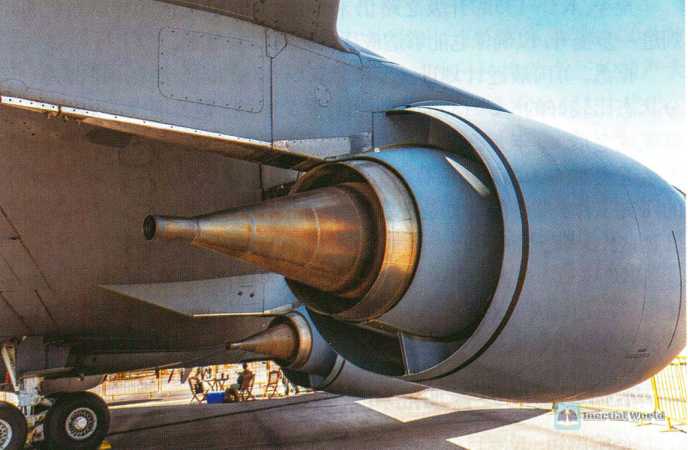
KC-135 tanker can refuel various aircraft with different performance. KC-135 aerial tanker adopts telescopic sleeve type (hard pipe type) refueling method, with a high oil delivery rate of 975~1690 liters per minute. It is composed of an external telescopic main pipe, telescopic sleeve and V-shaped control rudder. The telescopic sleeve is extended from the main pipe only when refueling, and can be adjusted according to the relative position of the receiving aircraft during the refueling process. It adopts a telescopic sleeve type aerial refueling system with an adjustment distance of 5.8 meters for refueling operations, and can move in a space range of 54 degrees up and down and 30 degrees horizontally. The fuel it carries is JP-4 type fuel, which can refuel various types of fighters and can also be used for its own engine. It has a total of 10 fuselage fuel tanks, located under the front and rear fuselage floors and the tail floor, and a central wing fuel tank. In addition, there is a main fuel tank and a spare fuel tank on each side of the wing. A KC-135 aerial refueling aircraft can refuel a B-52 strategic bomber or two FB-111 fighter-bombers in the air. In order to improve the overall performance of the aircraft, the US Air Force has made several improvements to it. In the 1970s, the KC-135 underwent a series of upgrades, including the "PACERCRAG" (thrust doubling) and "REACT" (refueling range improvement) projects, which were designed to improve the performance and efficiency of the aircraft. During the Vietnam War, the KC-135 provided aerial refueling support for various combat aircraft such as the F-105 "Thunderbolt" fighter-bomber, the F-4 "Ghost" fighter, and the B-52 "Coherence" strategic bomber, enabling these aircraft to perform missions in remote target areas, while increasing their stay time in the air and improving their strike effectiveness.
degrees and 30 degrees horizontally. The fuel it carries is JP-4 fuel, which can refuel various types of fighters and can also be used for its own engines. It has a total of 10 fuselage fuel tanks, located under the front and rear fuselage floors and the tail floor, as well as a central wing fuel tank. In addition, there is a main fuel tank and a spare fuel tank on each side of the wing. A KC-135 aerial refueling aircraft can refuel a B-52 strategic bomber or two FB-111 fighter-bombers in the air. In order to improve the overall performance of the aircraft, the US Air Force has made several improvements to it. In the 1970s, the KC-135 underwent a series of upgrades, including the "PACERCRAG" (thrust doubling) and "REACT" (refueling range improvement) projects, which are designed to improve the performance and efficiency of the aircraft. During the Vietnam War, the KC-135 provided aerial refueling support for various combat aircraft such as the F-105 Thunderbolt fighter-bomber, the F-4 Spirit fighter, and the B-52 Synchro strategic bomber, enabling these aircraft to perform missions in remote target areas, while increasing their stay time in the air and improving their strike effectiveness.
In the 1980s and 1990s, the KC-135 tanker ushered in a full range of upgrades and improvements, and all performance parameters were effectively improved. The KC-135 has undergone the "PACER COIN" project to upgrade its communication and navigation systems. The "PTPU" (Thrust Boost) project has improved engine performance and improved the TF33 engines of some KC-135 aircraft. The KC-135 has also undergone the second phase of the "PACER CRAG" upgrade to improve the availability of fuel tanks. In addition, the KC-135 has also undergone the "GLASSCOCKPIT" program to upgrade the traditional instrument cockpit to a glass cockpit to improve control and navigation performance.
To date, the KC-135’s upgrade journey has not stopped, and its advanced communication and navigation systems will be further improved to ensure that it can adapt to modern military needs.
It is reported that the United States recently plans to further reduce the comprehensive fuel consumption of the KC-135, and will add wingtip tips to some KC-135 tankers in relatively good condition. According to the calculations of the US Air Force, after the modification is completed, it can save up to $65 million in comprehensive costs each year. In the U.S. Air Force’s recently released fiscal year 2024 budget request, it hopes to provide $15 million to support related research work. The final plan is to seek up to $140 million to modify these KC-135 tankers from 2025 to 2028.
KC-135 tanker, an important role in air support, its rich equipment performance and multiple combat applications constitute a key link on the battlefield. This aircraft has maintained its important strategic position since its birth and has become a solid pillar for the extension and support of air power.
Hard pipe refueling and hose refueling that must be mentioned
As we all know, our army’s most advanced tanker is the "Yunyou-20" transformed from the Yun-20. At present, there are pictures of Yunyou-20 refueling the J-20 with hoses in the air on the Internet. In addition to the J-20, there are also pictures of Yunyou-20 refueling the J-16 and H-6 in the air on the Internet, all of which are hose refueling methods.
Therefore, the Y-20 and other tankers in my country all use hose refueling devices. When using this method for aerial refueling, the equipment of the receiving aircraft is very simple, as long as a fixed or retractable refueling pipe is installed on the nose or leading edge of the wing. The refueling equipment of the tanker consists of a winch, a 22 to 30-meter-long hose and a funnel-type cone sleeve. When the refueling pipe is extended into the cone, the mechanism on the cone automatically locks the refueling pipe mouth to connect it with the oil delivery hose, and the hose is released and recovered by the winch.
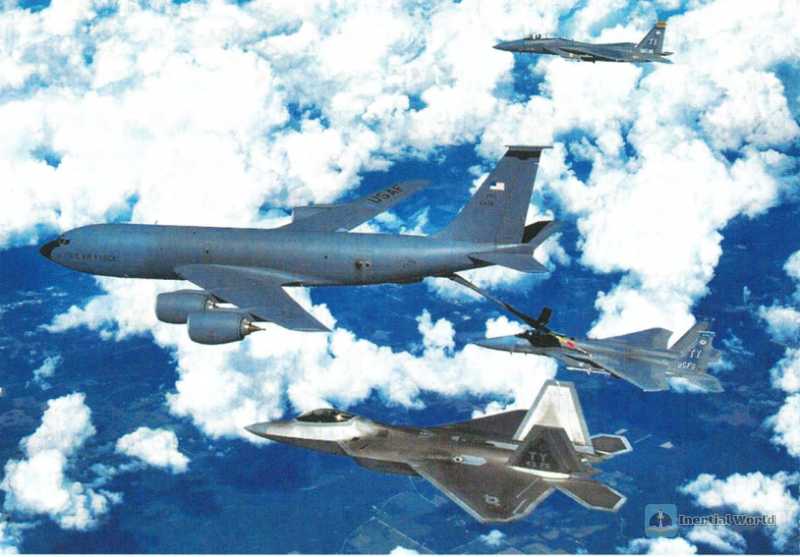
Using hoses for refueling, a large tanker can be equipped with several sets of refueling equipment, and can refuel several fighters at the same time. Since the tanker and the receiving aircraft are in relative motion, the use of flexible hoses is safer. It can be modified on different models and has a wide range of applicable speeds, from helicopters with a speed of 200 kilometers per hour to fighter jets. The technology is relatively easy to implement and the cost is low. No special operator is required. The disadvantages of hose refueling are: it is quite sensitive to atmospheric turbulence, it is difficult to connect, and it requires high operating skills from the pilot. The oil delivery speed is slow, about 1,500 liters per minute, so it takes a long time to refuel large military aircraft.
At present, my country has been using hose refueling technology for many years, and the technology is already quite mature. Previously, the H-6 was equipped with the RDC-1 refueling pod developed by my country. After a long period of upgrades and improvements, the RDC-1 refueling pod has been compatible with the specifications of the Russian-made UPAZ-IM aerial refueling pod. This means that the new domestic hose refueling pod can not only refuel the domestic J-10, J-11, and J-16 series fighters, but also the Russian-made Su-30 and Su-35 series fighters of the Air Force. This new type of pod has not only greatly increased the fuel carrying capacity and refueling volume of the Y-20, but also greatly improved its actual combat availability. Of course, if we compare the Y-20 with the KC-135 and A330 MRTT, or the most advanced KC-46 tanker of the US Air Force, there is still a certain gap. In terms of fuel supply, the A330MRTT of the European Air Force and the KC46 of the US Air Force are currently equipped with three hose refueling devices and one hard pipe refueling device.
Compared with hose refueling, the advantages of hard pipe refueling technology are very prominent. The refueling speed is fast, and the efficiency of hard pipe refueling is very high. The refueling volume can reach 6,300 liters per minute, which is equivalent to filling 1,500 cars in one minute. Ordinary fighters can solve the problem within one or two minutes, while the time required for hose refueling is four or five times that of hard pipe refueling. This is very likely to determine the success or failure of an air battle on the battlefield where "time is life"; hard pipe refueling has little effect on air flow disturbance. Due to the use of rigid telescopic sleeves, it does not affect air turbulence. The big upsetting feeling will not cause the J-10 tanker behind the H-6U to have difficulty aligning with the erratic refueling pipe in the air turbulence; the tanker is easy to operate and dock, which reduces the difficulty of the pilot’s operation.
Hard-pipe refueling technology certainly has some disadvantages, such as (for large aircraft) requiring a dedicated refueling operator; only one fighter can be refueled at a time; the refueling speed is high, and low-speed aircraft cannot be refueled; the structure is complex, and the tail of the aircraft needs to be modified, which is expensive. Due to the high refueling pressure, some fighters cannot withstand the maximum refueling rate, and the tanker must be regularly inspected and maintained.
However, compared with the hose refueling device used by my country’s current Y-20, the actual combat capability of European and American tankers equipped with hard-pipe refueling devices is still much stronger. Therefore, we have to admit that the lack of hard-pipe refueling devices is the biggest shortcoming of the Y-20, or my country’s Air Force tanker. This is also the reason why my country considered the use of hard-pipe refueling technology and carried out targeted design and testing when designing the J-20 fighter.
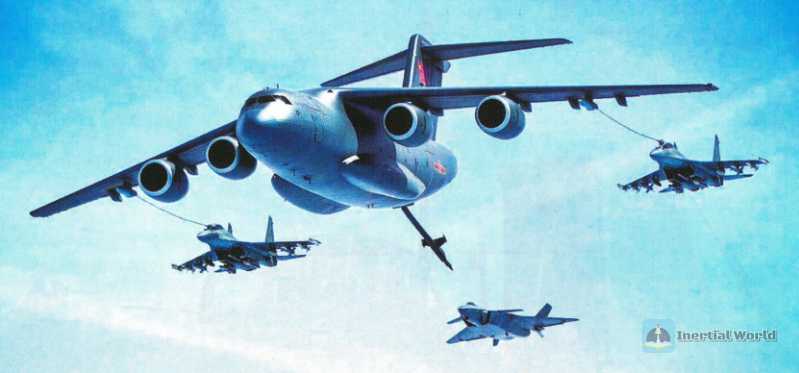
The hard pipe refueling device will make the Chinese Air Force soar
In fact, the research and development of hard pipe refueling has already begun in China. According to the situation revealed, it is likely to mature in about 5 years. At that time, as the only available aerial refueling platform in China, the Y-20 is likely to be equipped with a hard pipe refueling device. This is because the prototype of the Y-20, the Y-20 large transport aircraft, has been replaced with a brand-new domestic large bypass engine, and its load capacity and maximum take-off weight have been greatly improved. It is reported that the maximum take-off weight of the Y-20 has increased from 179 tons to 220 tons. Therefore, the performance of the Y-20 platform has reached the best at present, which provides the platform basic conditions for the further modification and upgrading of the Y-20.
The Y-20 equipped with a hard-pipe refueling device is bound to greatly enhance the capabilities of the Chinese Air Force’s "trump card" J-20. The J-20 is not only the "trump card" weapon of the Air Force, but also a "kick-in" weapon. Its mission is to play the role of the first attack in the war. At the same time, in the denial mission, the J-20 needs to move forward significantly to intercept the enemy’s long-range bombers and fighters. Therefore, it is natural for the J-20 to use hard-pipe refueling to greatly extend its range and shorten the refueling time. After adopting the hard-pipe refueling technology, theoretically, 12,000 liters or nearly 10 tons of fuel can be received in about 2 minutes, which is close to the maximum internal fuel load of the J-20. The maximum range of the J-20 after refueling exceeds 8,000 kilometers, and the maximum combat radius can be easily extended to more than 3,000 kilometers. After multiple refuelings, the J-20 can completely complete a long-distance flight across the ocean and continent like the F-22. With the cooperation of the Y-20 hard-pipe refueling aircraft, the J-20 with aerial refueling capability can cover the first and second island chain areas in combat interception range, becoming the sharpest "spear" of the Chinese Air Force with both offensive and defensive capabilities.
Of course, our most ideal refueling method is still "soft and hard coexistence" like the KC-46, that is, "old aircraft" use hose refueling and "new aircraft" use hard pipe refueling. This mechanism enables most of the combat aircraft of the Air Force that are capable of aerial refueling to be fully covered by tankers, which is more reasonable than radically and directly promoting hard-pipe refueling technology or conservatively continuing to use hose refueling technology.
While walking at the Singapore Air Show, I was wondering when our military tankers could be equipped with such hard-pipe refueling devices, or when a mature "hard and soft coexistence" aerial refueling mechanism could be formed. Maybe tomorrow, let’s look forward to it together!
Related reading
- 国产大飞机海外首秀:中国商飞C919和ARJ21飞行展示
- Domestic large aircraft overseas debut: COMAC C919 and ARJ21 flight demonstration
- 从美军B-52H战略轰炸机双机通场新加坡航展说起
- 近距离观察F-35A隐形战斗机
- 近观新加坡F-15SG战斗机
- 我进入了F-16D的座舱
- 新加坡航展上的萨博“鹰狮”JAS-39战斗机
- 我当上了苏-30的飞行员--苏-30MKM战机前的超强体验
- 中国的“老朋友”--来自冲绳的P-8A反潜巡逻机
- 又见C-17运输机
- 首次亮相新加坡航展的直-10ME
- 公开展示的“阿帕奇”武装直升机
- 静态展示的CH-47F“支努干”重型运输直升机
- 细看新加坡“紫菀”-30防空导弹
- 先进机型齐亮相---新加坡航展上的中航展台
- 混动装甲战车--新加坡“特雷克斯s5”轮式装甲车管窥
- 2024年新加坡航空展室内展台参观记