Submarines can not only rely on the advantage of long underwater navigation to avoid the search and attack of surface ships and other combat platforms, but also use concealment to launch attacks on the enemy. Therefore, whether it can be equipped with a powerful power system has become an important factor affecting the comprehensive combat capability of submarines.
The power system of conventional submarines is usually divided into diesel-electric power system and air-independent propulsion (AIP) system. Since the diesel-electric power system relies on battery power when sailing underwater, and the battery capacity is limited, it needs to be charged in the snorkel state. This is undoubtedly the most exposed moment for submarines and the most fatal weakness of conventional submarines. Therefore, installing an AIP system on conventional submarines is one of the effective means to increase endurance and improve concealment.
The submarine AIP system is mainly divided into two categories: thermal engine system and electrochemical system. The thermal engine AIP system mainly includes closed cycle diesel engine (CCD), closed cycle steam turbine (MESMA), "Stirling" engine (SE) and small nuclear power unit (SSN), and the electrochemical AIP system mainly includes alkaline fuel cell and proton exchange membrane fuel cell (PEM). However, the AIP systems with relatively mature technology and have entered the practical stage are mainly closed cycle diesel engine, "Stirling" engine, closed cycle steam turbine and fuel cell.
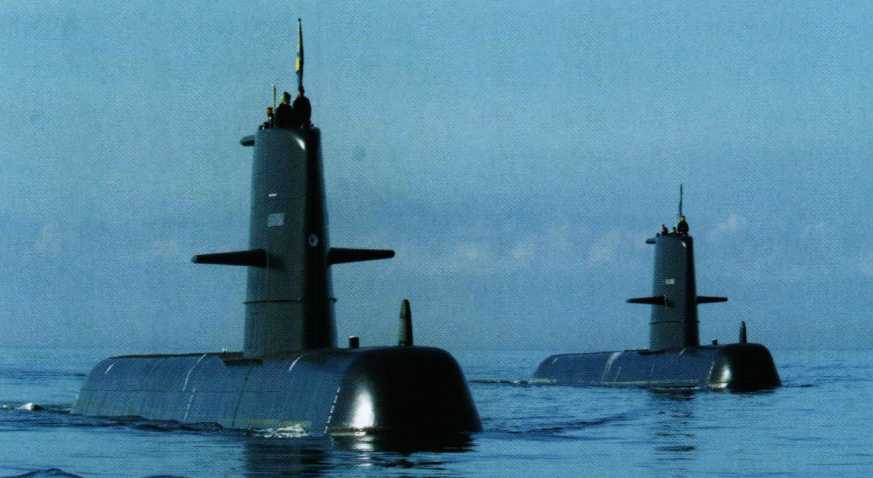
Closed-cycle diesel engine AIP system
The closed-cycle diesel engine AIP system uses a traditional diesel engine as the main engine and realizes a closed cycle by controlling the intake and exhaust of the diesel engine. The exhaust gas generated by the diesel engine enters the absorber after cooling. The exhaust gas is fully mixed with seawater in the absorber. The carbon dioxide and water vapor are dissolved in the seawater and discharged outside the boat through the water management system. Part of the cleaned gas enters the mixing chamber, and after replenishing oxygen and argon, it returns to the diesel engine to realize a new combustion cycle
The prototype of the closed-cycle diesel engine AIP system appeared in the late World War II. The Soviet Union built many Type 615 and Type 617 submarines, but the process of hydrogen peroxide decomposing into oxygen is very unstable and prone to explosion. Among them, the M-256 submarine sank due to a fire caused by the explosion of liquid oxygen (later, liquid oxygen was replaced with sodium peroxide), so the Type 615 was also nicknamed "lighter", which also led to the early retirement of all Type 615 in the 1970s.
The United Kingdom, Germany and the Netherlands are the main countries researching the AIP system of closed-cycle diesel engines. In 1980, the United Kingdom developed a 25-kilowatt closed-cycle diesel main engine, using potassium hydroxide as a chemical purifier for carbon dioxide and introducing argon into the circulating gas to solve the thermal efficiency problem. This technology aroused the interest of Germany and the Netherlands, and further research was carried out.
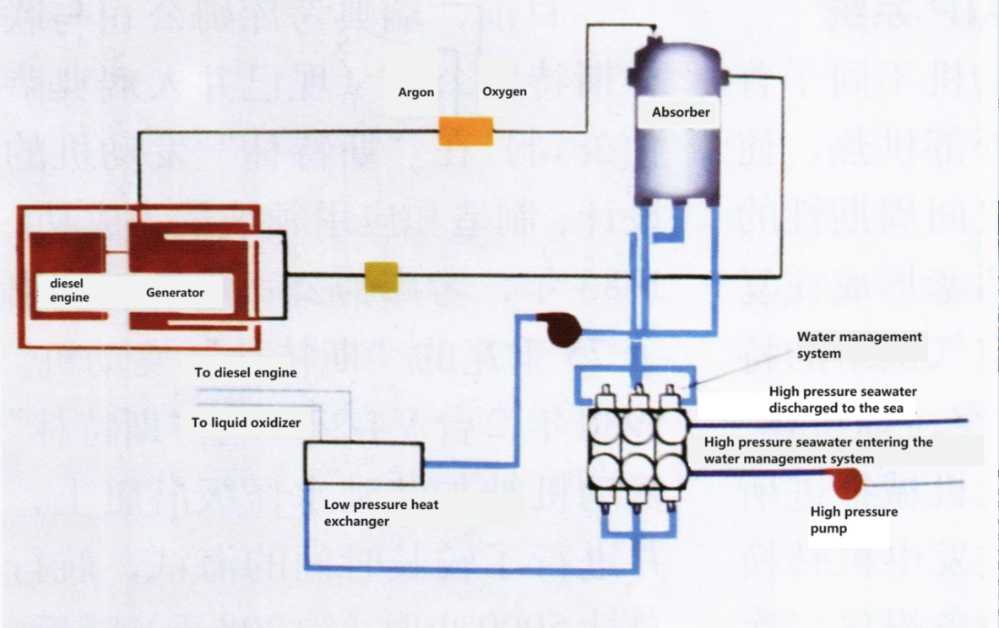
In 1993, Germany successfully tested a 250-kW closed-cycle diesel engine system on the retired Type 205 submarine U1, and prepared to modify it on the Type 209 exported abroad. It plans to install the AIP system with an additional pressure-resistant compartment, which will be inserted into the submarine. This can ensure that the submarine’s endurance time increases by 4 to 5 times when the maximum underwater speed remains unchanged. It can sail continuously for 16 days at a speed of 4.5 knots underwater, and its endurance is close to 1,800 nautical miles (about 3,333 kilometers).
In 1993, the Netherlands built a third-generation 450-kW closed-cycle diesel engine and an improved water management system, and subsequently designed the Moray-class submarine equipped with an AIP compartment, preparing to sell this class of submarines to the international market. The Eel class includes 1100, 1400 and 1800 types. The 1400 and 1800 types can be equipped with a 300-kilowatt closed-cycle diesel engine AIP system, which can sail continuously underwater for 20 days and have a low-speed range of up to 11,000 nautical miles (20,372 kilometers).
Although the closed-cycle diesel engine technology is mature, easy to mass-produce, low in development cost and high in reliability, due to the large oxygen consumption, high noise generated, and low efficiency caused by the limited system output power, countries have basically stopped developing this technology.
Closed cycle steam turbine AIP system
The closed cycle steam turbine system consists of a high-temperature gas circuit and a steam circuit: ethanol and oxygen are mixed and burned in the combustion chamber of the high-temperature gas circuit to produce high-temperature and high-pressure gas. The gas is sent to the steam generator for heat exchange and then enters the cooling device. Part of the cooled gas returns to the combustion chamber, and part is discharged outside the boat by its own high pressure; the water in the steam circuit evaporates into high-temperature and high-pressure steam in the evaporator, and outputs power through the steam turbine. The steam enters the condenser and condenses into water, and then enters the steam generator, thus completing the steam cycle
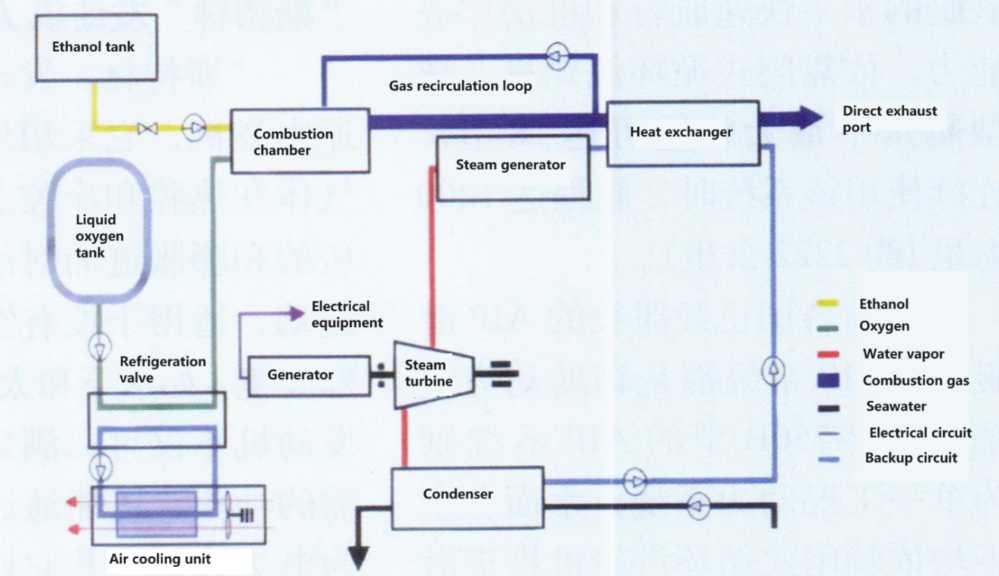
Currently, France is the country that has made the greatest technological progress in the closed cycle steam turbine AIP system. The French Navy replaced the ruby-class nuclear reactor with an ethanol boiler, heated the water through the combustion of liquid oxygen and ethanol to produce steam, and then drove the steam turbine to drive the generator set, charging the battery or directly driving the motor to work in a closed underwater environment.
Bertine, a French company, has developed a closed-cycle steam turbine system and installed a 200-kilowatt closed-cycle steam turbine AIP system on the Augusta 90B submarine for military trade export. In 1994, Pakistan ordered three submarines, named Khalid-class, becoming one of the first countries in the Asia-Pacific region to have AIP submarines.
The Scorpio class, one of the best-selling submarines in the international military trade market, was jointly developed by France and Spain. It has flexible technology and advanced performance. It can be equipped with a closed-cycle steam turbine AIP system, with an output power of more than 200 kilowatts, and can sail continuously underwater for 18 to 21 days at a speed of 4 knots.
In 2019, Russia’s first P-750B (Serval-class) submarine equipped with a closed-cycle steam turbine AIP system was unveiled, which attracted special attention. Although this type of submarine is still in the design stage, the closed-cycle steam turbine system has completed model manufacturing and is undergoing testing and research.
The P-750B is equipped with two closed-cycle steam turbines with a single power of 400 kilowatts and a 2,500-kilowatt propulsion motor. It can sail continuously underwater for 30 days and nights, which can greatly improve the submarine’s underwater rapid navigation and maneuverability. Relying on the closed-cycle steam turbine, the maximum underwater speed of this type of submarine can reach 18 knots. When the system is used continuously, the range is 1,200 nautical miles (about 2,222 kilometers)
Among the AIP submarines currently in service in various countries, the AIP system is an auxiliary power system, while the P-750B AIP system is a single-operating power system, which relies on closed-cycle steam turbines to propel the submarine both on the surface and underwater. When sailing on the surface, it uses air to work; when sailing underwater, it uses liquid oxygen stored in the Dewar flask to work. This design not only reduces the complexity of the power system, but also helps to reduce the size of the submarine and the underwater displacement.
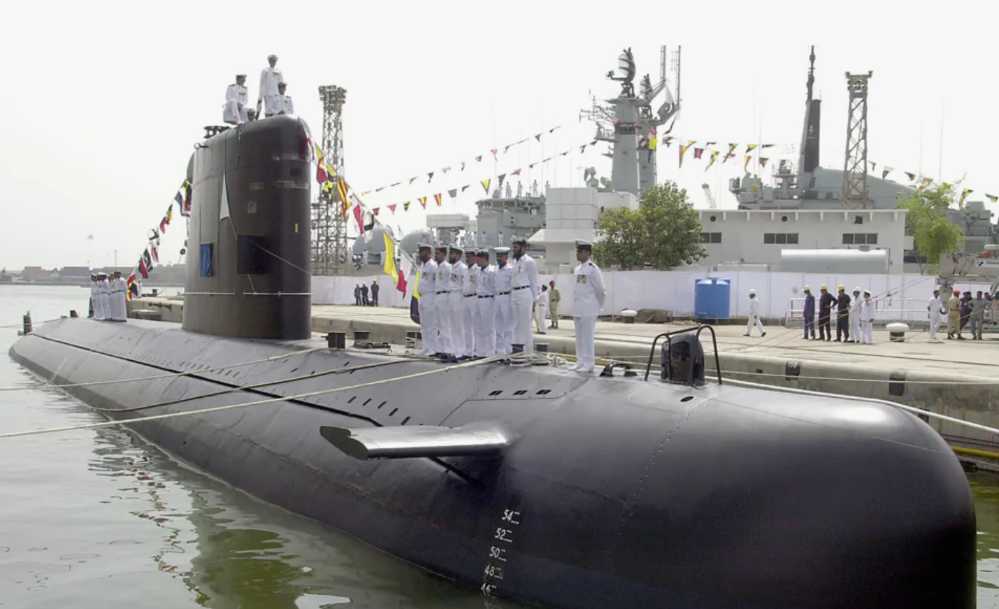
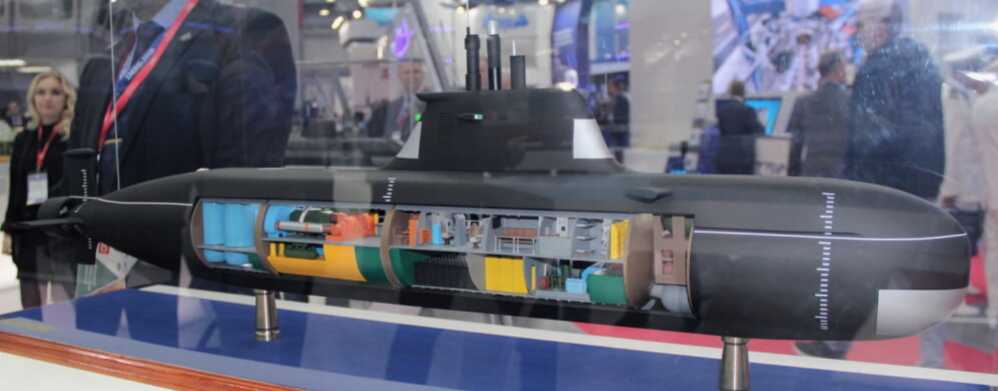
"Stirling" engine AIP system
The "Stirling" engine is different from ordinary internal combustion engines. It uses external heating to make the gas periodically compress and expand between the hot chamber and the cold chamber to form reciprocating motion on the piston. It is suitable for special environments without air supply, such as underwater and space. The "Stirling" engine can not only meet the power required for mechanical propulsion, but also convert it into electricity through a generator to provide secondary energy for other equipment on the boat. Although there are problems such as difficult manufacturing process, high manufacturing cost, and high sealing technology requirements, due to its characteristics of thermal engine cycle, it is very suitable as a submarine AIP system and can provide sufficient power for submarines to continue underwater navigation.
Currently, Sweden’s Kockums and United Stirling (now incorporated into Sweden’s Saab) are the most successful in the design, manufacture and application of the "Stirling" engine. In 1983, Kockums successfully developed a 75-kilowatt "Stirling" engine. In 1988, two V4-275R Stirling engines were installed on the Submarines-class submarines and underwent a long sea trial, with a total of 5,000 hours (about 208 days). Subsequently, the Swedish Navy decided to equip the Gotland-class submarines with the Stirling engine AIP system. The Gotland became the first submarine to include the Stirling engine in the equipment sequence at the initial stage of design, occupying an important position in the history of submarine development. The Gotland equipped with the AIP system has an underwater endurance increased from the usual 2 to 3 days to more than 15 days, greatly enhancing the submarine’s concealment.
After learning about this, the Japanese Defense Equipment Agency actively contacted Sweden and introduced the manufacturing technology of the Stirling engine for equipment or modification of the conventional submarines of the Japanese Maritime Self-Defense Force. The Soryu class is the first batch of Japanese submarines to adopt AIP technology. The power system consists of 2 diesel engines, 4 Stirling engines (the "Yinglong" and "Doulong" are not equipped) and 1 main propulsion motor (lead-acid batteries for boats 1 to 10, lithium batteries for "Yinglong" and "Doulong"), with an underwater output power of 5880 kilowatts (4116 kilowatts for "Yinglong" and "Doulong") and a maximum underwater speed of 20 knots (close to 20 knots for "Yinglong" and "Doulong"). Equipped with 4 V4-275R-Ⅱ engines, the continuous charging power can reach 300 kilowatts, and the underwater endurance is 5 to 7 times longer than that of the Oyashio class.
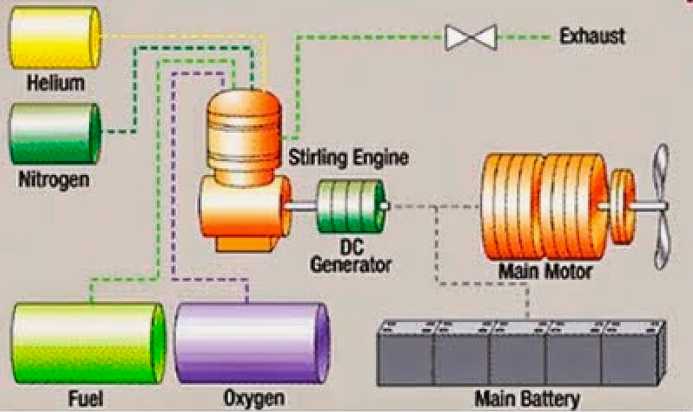
Fuel cell AIP system
Fuel cells use catalysts at the anode and cathode to accelerate electrochemical reactions, converting chemical energy into electrical energy. Fuel cells and their auxiliary devices are collectively referred to as electrochemical generators. Fuel cells are also divided into different types according to the properties of the electrolyte. Each type of fuel cell requires specific electrode materials and fuels. The most widely used one is the proton exchange membrane fuel cell (PEMFC).
In the 1970s, the Soviet Union developed the proton exchange fuel cell (PEMFC). The Celestine Design Bureau modified the Type 613 submarine to provide power for the submarine through fuel cells. The ordinary 613 type can achieve low-speed navigation at 2 knots and a cruising range of 3 to 7 days. The modified S-273 is equipped with a 280-kilowatt fuel cell, which can cruise at a speed of 2.5 knots for 28 days.
Siemens of Germany has also conducted long-term research on the fuel cell AIP system. In 1983, it built a full-scale test bench on land. For testing, the German Navy modified the Type 205 U1 submarine (hull number S-180) and embedded a 3.8-meter fuel cell AIP system compartment in the middle of the hull, increasing the displacement by about 30 tons. The installed power unit includes two 900-kilowatt diesel engines and one 1,100-kilowatt main propulsion motor, using a 7-kilowatt fuel cell module with a total power of 100 kilowatts. The generated electricity can be directly supplied to the main propulsion motor or used to charge the battery, which greatly improves the submarine’s technical and tactical level. It can not only extend the submarine’s underwater endurance, but also continuously charge the battery pack underwater. In 1988, the U1 submarine underwent a nine-month seaworthiness test and was able to sail underwater for 200 nautical miles (about 370 kilometers).
German submarine engineers believe that fuel cells as submarine AIP systems have more advantages than Stirling engines and closed-cycle steam turbines. Subsequently, the Type 212A submarine was developed to replace the Type 205 and Type 206, and the feasibility of adding an AIP compartment to the export version of the Type 209 was studied.
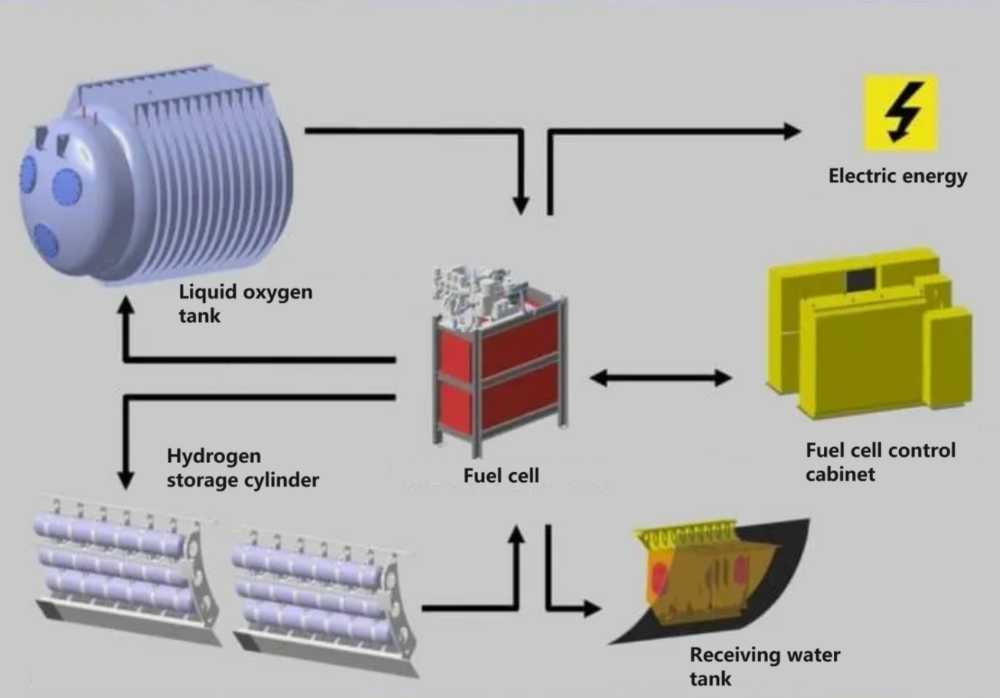
In 1998, the construction of the first Type 212A submarine U31 began. The propulsion system consists of a traditional diesel engine and a fuel cell system. The fuel cell system includes a fuel cell stack, a 14-ton oxygen storage tank, and a 1.7-ton hydrogen storage tank. Among them, the fuel cell stack consists of 9 groups of proton exchange membrane fuel cell modules, each with an output power of 34 kilowatts, and 9 groups totaling 306 kilowatts. When fuel cells are used for propulsion only, it can sail underwater for 21 days without interruption; the endurance at a speed of 4.5 knots exceeds 1,250 nautical miles (about 2,300 kilometers) and the self-sustaining capacity is 12 days; when batteries and fuel cells work together, it can ensure non-stop underwater sailing for more than 15 days, with a cruising range of 1,638 nautical miles (about 3,000 kilometers). Compared with the 209 type, it has increased by 4.4 times, greatly improving the combat capability and survivability of the submarine.
Based on the 212A type, the German Navy launched the 214 type for export: the power system uses two 2,000-kilowatt MTU 16V396 diesel engines and is equipped with two 120-kilowatt fuel cell modules, with an underwater self-sustaining capacity of up to 14 days. The Greek Navy purchased two to replace the Type 209 to maintain the combat strength of its submarines; South Korea purchased three and obtained some technology transfer, opening the precedent of its own submarine development and developing the Dosan Anchanghao class.
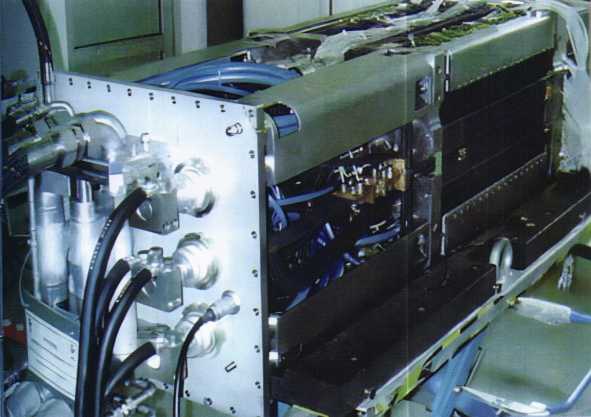
Both the Type 212A and the Type 214 use metal hydride storage tank technology, which is relatively mature, but the storage tank is quite bulky. At present, only pure hydrogen can be used as a fuel cell. The processing and extraction process of pure hydrogen is extremely complicated, and in such a small space as a submarine, once a leak occurs, the concentration exceeds the limit and is very likely to explode, which is very dangerous.
Germany is exploring chemical hydrogen production methods such as ethanol and methanol. These fuels are safe, reliable, and easy to store and convert on board, but they need to deal with the hidden emission of carbon dioxide under high pressure generated during the hydrogen production process. The Type 216 submarine is planned to use methanol-to-hydrogen fuel cells, but there are problems such as carbon dioxide emissions and impure hydrogen, so it has not yet been installed on the submarine.
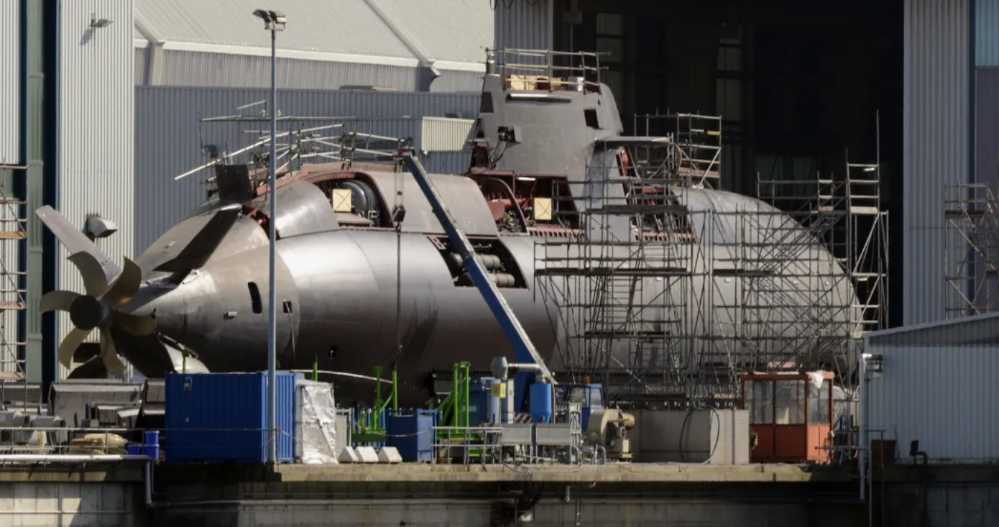
Small nuclear power AIP system
The small nuclear power AIP system is to add a miniaturized nuclear power unit to a conventional submarine, forming a power system of "diesel-electric + small reactor nuclear power". Normally, it is powered by a battery pack or a diesel-electric unit. When diving underwater for a long time, it is powered by a small nuclear power system, which allows the motor to run at low speed and charge the battery pack; when sailing at high speed, the small nuclear power system is connected in parallel with the battery pack to supply power.
The AMPS (Autonomous Marine Power Plant) series developed by Canada’s Ottawa Energy Conversion Systems is currently the most typical practical small nuclear power reactor. The AIP system has high technical maturity and rich test data, especially the AMPS1000 type, which has good safety, compact structure and long life. The submarine installed with it can obtain almost unlimited endurance at a speed of 8 to 12 knots without using batteries, which greatly improves the underwater navigation performance of conventional submarines.
The successful experience of the AMPS small nuclear power system has attracted the attention of France. The French Navy once installed a small nuclear power plant on the Augusta-class submarine for testing. Under the premise of ensuring the power demand of the entire submarine, the main propulsion motor power reached 900 kilowatts. When the submarine’s underwater speed was 13 to 17 knots, the underwater endurance reached 13,000 nautical miles (about 24,000 kilometers). The traditional diesel-electric power can only reach an underwater speed of 7 knots and an underwater endurance of 6,700 nautical miles (about 12,400 kilometers).
Although the addition of a small nuclear power compartment can greatly improve the comprehensive combat performance of conventional submarines, and it has more economic advantages than directly purchasing and equipping nuclear submarines, due to various reasons, the small nuclear power AIP system has never been truly added to the equipment sequence of submarines in various countries, and it still remains in the testing stage and scheme design stage.
Performance comparison and development prospects
Currently, the AIP technology vigorously developed by the navies of various countries is still dominated by the "Stirling" engine and fuel cells. For the AIP technology of the thermal engine system, they all require fuel combustion and mechanical transmission, so they cannot avoid the generation of thermal radiation and mechanical noise, and the maximum efficiency of the thermal engine system is limited by the Carnot cycle (a simple cycle with only two heat sources), and the efficiency is generally low. In contrast, fuel cells have no moving parts and do not require electrical energy conversion, so the noise is low, which enhances the stealth of submarines. Fuel cells directly convert chemical energy stored in fuel and oxidant into electrical energy, and the energy conversion reduces two steps compared to traditional heat engine conversion. Therefore, the absolute advantage of high efficiency determines that the fuel cell AP system has a good development prospect in the future.