After the Second World War, due to technological progress and military needs, drones gradually developed. In the 1950s, the Soviet Union’s demand for drones became urgent. The famous designer Lavochkin was ordered to design a new La-17 drone, which was a military drone officially in service in the Soviet Union. The La-17R drone was also the last military aircraft named after Lavochkin. At the same time, the La-17 also entered China. The Changkong No. 1 drone designed with this as a reference was also my country’s first large-scale high-speed drone. Not only that, the La-17 is also a long-lived aircraft. Its improved version, the La-17K, is still in service in the Russian army, and the improved version of Changkong No. 1 is also in service in my country in small quantities. Let’s take a look back at this classic work that has great significance for both countries.
Master’s posthumous work
1. Product 201
In the 1940s, unmanned target aircraft had already appeared. After the end of World War II, unmanned target aircraft were more widely used. With the advent of the jet age, aviation powers also thought about developing jet unmanned target aircraft. The Soviet Union also had towed target aircraft and ordinary fighters converted into drones at that time, but the former could not effectively simulate jet fighters and missiles, and might hit the towing aircraft, while the latter was extremely expensive. In 1950, Air Force Marshal K.A. Vershinin proposed to S.A. Lavochkin to develop a radio-controlled unmanned target aircraft training proposal, which would be used for air defense force training and testing K-5 air-to-air missiles. Lavochkin readily accepted it. On June 10 of the same year, the Soviet Council of Ministers issued Decree No. 2474-974, officially issuing a development order. Lavochkin initially appointed A.A. Merkulov as the chief designer, and later A.G. Chesnov took over. The new aircraft was codenamed "Product 201"
Considering the purpose of the target aircraft, it is necessary to find ways to reduce costs. The aircraft’s appearance design is very simple, and it looks like a V-1 missile with the engine moved to the belly of the aircraft. The steel mailbox occupies most of the fuselage. The reason why aluminum alloy is not used is that steel is easier to weld. The engine uses the RD-800 ramjet engine developed by the 670th Experimental Design Bureau (OKB-670), designed by M.M. Bondaruk. The engine has a diameter of 800 mm and uses gasoline as fuel. At the same time, the fuel supply system does not use an oil pump, but a high-pressure gas cylinder, which is extremely simplified. The engine compartment is located under the fuselage. In addition to the fuel tank, the most expensive equipment inside the fuselage should be the AP-53 autopilot designed by A.G. Antipov of the 112th Experimental Design Bureau (OKB-112), which was changed to AP-60 in 1952 and AP-61 a year later. In addition, there is a radio device designed by N.I. Belev of the 648th Institute (NII-648). All electrical equipment is powered by a generator located in the nose and driven by a small 2-blade propeller.
Initially, the design did not consider installing landing gear, but adopted belly landing, similar to the Me-163, and installed shock absorbers and parachutes to slow down the landing speed and reduce the impact force. However, it was found during the design that the shock absorber had a complex structure and was very heavy. Moreover, as a target aircraft, the landing problem was only considered when it was not shot down. Therefore, the shock absorber was simply abandoned and the engine compartment was used for shock absorption. Since there were no parts inside the ramjet engine, there was enough deformation space. Besides, the ramjet engine itself was not valuable, and it could be replaced if it was damaged.
Because it uses a ramjet engine, it cannot take off autonomously, so it is carried by a mother aircraft. Initially, it was planned to use the Tu-2 to carry it, but this plan was considered too risky. In December 1951, it was changed to use the Tu-4 underwing suspension, which greatly improved the safety factor and launch success rate.
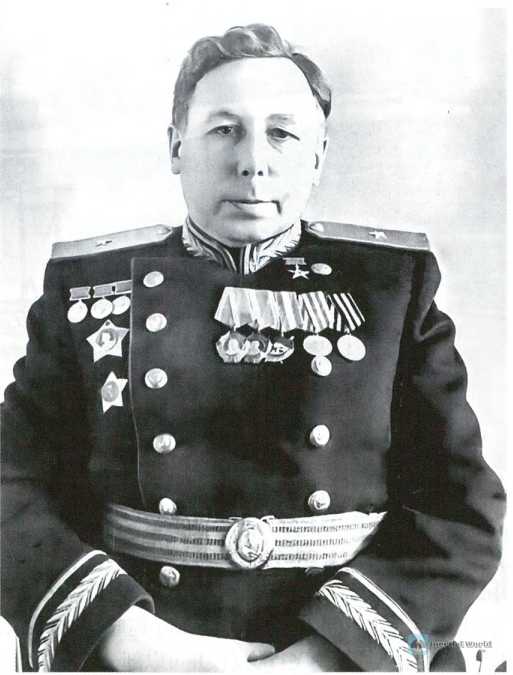
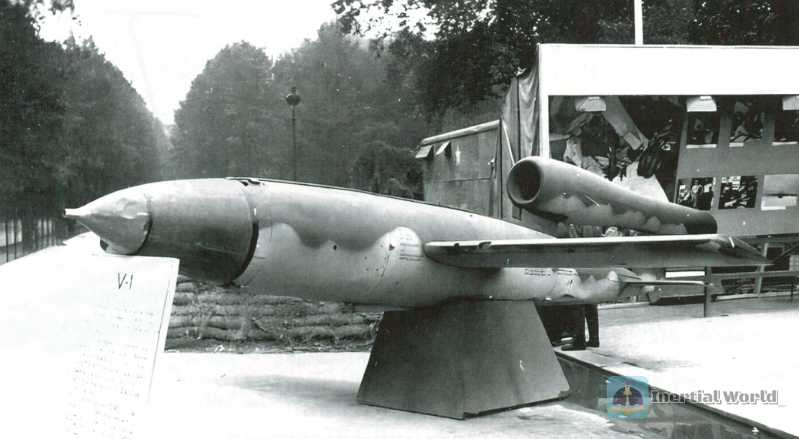
On May 13, 1953, Product 201 began factory testing at the test site of the Sixth National Intelligence Bureau of the Air Force. This test was pre-programmed with a route program and did not use radio control. Two Product 201s were hung under the wings of the Tu-4. The mother aircraft launched the drone at an altitude of 8,500 meters and 515 kilometers per hour. The drone flew for about 20 minutes and was in good condition. The maximum flight speed was about 850 kilometers per hour. The fuel in the aircraft could provide the aircraft with about 20 minutes of flight. However, the parachute was not very effective. Although the aircraft adopted a high angle of attack posture and opened the parachute to slow down during landing, the aircraft still landed at a high speed, and the engine compartment was also deformed. After recovery, the engine could only be replaced. Fortunately, the ramjet engine was not expensive.
The national test was carried out at the Vladimirnovka Air Force Test Site from June to October 1954. A total of 19 flights were carried out, 13 of which were airdropped, including one double-aircraft salvo. In the test, the maximum flight speed of Product 201 was 911 kilometers per hour, and the cruising speed was around 600 kilometers per hour. The flight altitude ranged from 2,800 meters to 9,800 meters, and the cruising endurance time was about 40 minutes. The aircraft can simulate the flight status of the main missiles at that time, and can partially imitate fighter jets. The test found that if the flight control system was improved, the flight time could be extended by 1.5 minutes. The landing system is still not successful. After the engine stops working, the aircraft can continue to maintain altitude for 80-100 seconds, and then start to hang up and descend at a speed of 300-340 kilometers per hour, that is, about 8-10 meters per second. Before approaching landing, the aircraft adopts a high angle of attack attitude to continue to slow down, and the descent speed will be halved. At the same time, the parachute is opened. Landing will inevitably damage the engine, so the engine is basically disposable.
Although Product 201 can meet the training requirements of air defense forces, it cannot meet the test of K-5 missiles. Because according to actual tests, the RP-1 and RP-2 radars equipped by Soviet fighters can only detect Product 201 at a distance of 2-3 kilometers and track at a distance of 1.1-1.25 kilometers, but the minimum launch distance of the K-5 missile cannot be less than 3 kilometers, so the test did not continue. According to the national test results, the relevant departments suggested that 5 more Tu-4 bombers be modified as carriers and more military tests be carried out. After the 1960s, the improved La-17M entered military service. The La-17 with ramjet engines was also equipped with rocket boosters and changed to ground launch. For this reason, the fuselage was specially reinforced. These improved La-17s were named La-17N.
In general, product 201 met the design requirements, but because it needed to be transported by a mother aircraft, the cost was still relatively high. However, the Soviet Ministry of Defense decided to accept this result and determined that the aircraft could be finalized, named La-17, and mass production began. From 1956 to 1958, a total of 249 La-17s were produced at Factory 47 in Orenburg and Factory 21 in Gorky. In addition, the Kazan Aircraft Manufacturing Plant also modified 6 Tu-4s (including the one modified during the test) to launch the La-17. Interestingly, in the mid-1950s, the Western aviation yearbooks clearly distinguished between the MiG-15 and the La-15, but there was no information about the La-17, which shows that the aircraft had a high level of confidentiality.
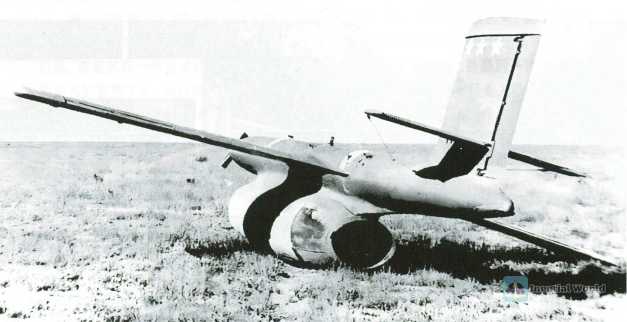
2. Product 203
After the La-17 entered service, it did not receive enough praise. The reason is very simple. The launch method of the aircraft is not economical, and because of the use of ramjet engines, the endurance is very short. Once the air defense forces fail to shoot down the target aircraft for the first time, the target aircraft will run out of fuel before the next approach. The military urgently asked the Lavochkin Design Bureau to improve the La-17 target aircraft. In July 1958, the Soviet Council of Ministers ordered the improvement of the La-17. The Lavochkin Design Bureau acted quickly. A.G. Chernokov proposed an improvement plan based on a series of problems of the La-17, and the design code was Product 203. The general idea of the plan is: replace the turbojet engine to increase the range, use a ground launch vehicle, and install a rocket booster.
Chernokov chose the simplified version of the RD-9B engine used on the MiG-19 fighter, the RD-9KTRD, which does not have afterburner capability and many structures have been simplified. The service life is 15 hours, and the thrust is reduced from 3,300 kg to 1,950 kg, but this is much higher than the thrust of the RD-900, which is less than 700 kg. There are teardrop fairings on the wingtips for compressed air, which will be sent to the engine to improve flight quality. The rocket booster is the PRD-98 type. The launch vehicle is an improvement on the gun vehicle of the KS-19 100mm anti-aircraft gun, with the design code 202, which is why the design code of the improved La-17 is directly 203. In addition, the autopilot has also been replaced with the AP-73 type.
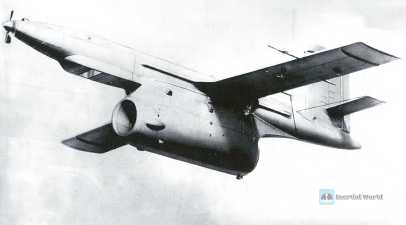
The improved La-17 has a maximum take-off weight of 3,065 kg (2,472 kg if the rocket booster is not installed), a range of 490 km, and a ceiling of 16,000 meters. However, due to the aerodynamic design, after replacing the engine, the flight altitude should not be lower than 3,000 meters, otherwise it is easy to disintegrate. The problem of low radar visibility of the La-17 has not been well solved, which is a good thing for the aircraft itself, but not for the target drone. Therefore, it is necessary to add Lunenberg lenses or corner reflectors to increase the radar reflection area, but it is still difficult for the radar to detect it. Product 203 began state testing in May 1960, and was finalized and put into service in the same year, with the designation La-17M (M means "improved"), and then began mass production until it was discontinued in 1964.
However, on June 9, 1960, S.A. Lavochkin, a famous Soviet aircraft designer, twice a hero of socialist labor, a winner of the Stalin Prize, a member of the Supreme Soviet of the Soviet Union, and an academician of the Soviet Academy of Sciences, died at home due to severe cardiovascular circulatory disorders, resulting in cardiac arrest. After the death of the core figure of the 301st Experimental Design Bureau (OKB-301, also known as the Lavochkin Design Bureau), the design bureau lost its independent status and became the 5th Bureau of the 52nd Experimental Design Bureau (OKB-52, Chelomey Design Bureau). After the merger, the actual person in charge was the former deputy chief designer G.N. Babakin. When the Soviet Union’s Lunar Project E-6.5 lunar probe failed to launch in 1964, S.P. Korolev, the head of the 1st Experimental Design Bureau (OKB-1), began to seek technical help. At this time, he was interested in the former Lavochkin Design Bureau, which had been incorporated into OKB-52, so he actively contacted Babakin, who also responded positively. In April 1965, Korolev personally visited the 5th Bureau and handed over all the design data of E-6 to Babakin. Babakin, who was overjoyed, immediately separated the 5th Bureau from the OKB-52 Design Bureau with the assistance of Korolev and renamed it "Lavochkin Design Bureau". Babakin himself was directly promoted to the chief designer of the design bureau. Unfortunately, Korolev, who helped the design bureau to become independent, also died on January 14, 1966.
Although Lavochkin passed away, the improvement of La-17 had to continue. Due to the large-scale adoption of anti-aircraft weapons in the 1960s, aircraft began to focus on low-altitude penetration, so the La-17M, due to its high minimum flight altitude, was no longer in line with the needs of the times.
In November 1961, the former Lavochkin Design Bureau, which had become the 5th Bureau of OKB-52, began to continue to improve the La-17M, planning to expand the flight altitude of the target aircraft to 500-18,000 meters, and further increase the radar reflection area to effectively simulate the Tu-16, Il-28 bomber and FKR-1 cruise missile. This improvement was relatively simple, so there was no new design code. The main content was the use of the RD-9BKR turbojet engine, with a service life extended to 30 hours, and the thrust could be adjusted according to the change of low-altitude flight status. The autopilot was also replaced by the AP-122 type from the AP-73 type, and the processing and control capabilities were further enhanced. The rear fuselage was installed with a Lunenberg lens to increase the radar reflection area. The improved La-17M is called "La-17MM", which means "improved version of La-17M"
The new aircraft was tested by the state from October to December 1963. The test results showed that the La-17MM could fly at an altitude of 580-18,100 meters, with a significantly longer flight time. It could last for 32 minutes at an altitude of about 600 meters and 97 minutes at an altitude of about 18,000 meters. The maximum flight speed could reach 875 kilometers per hour, while the landing speed was 270-302 kilometers per hour, and the sinking rate was 5-6 meters per second. In 1964, the La-17MM began mass production.
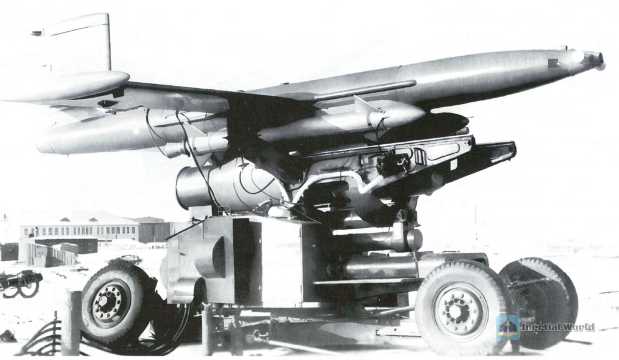
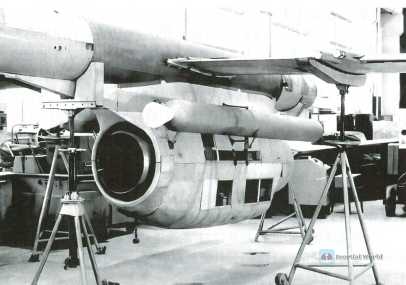
However, as the RD-9 series engines were gradually exhausted after the mid-1970s, and most of the engines in service were replaced by the P-11 series engines, the RD-9 series engines were discontinued in 1985. Of course, even if it were not for the replacement of new engines, the RD-9 series engines were already outdated, so it was not economically viable to maintain a production line of outdated equipment just for individual models of aircraft. Some people proposed to use the RI1F-300 engine on the retired MiG-21 to replace the RD-9 series engine. Considering that there are still a large number of La-17s in service in the army, this work is imperative. At this time, the Lavochkin Design Bureau has completely turned to the missile and aerospace fields, so the improvement work was entrusted to the Kazan Aircraft Manufacturing Plant. The improvement took three years. Mass production began in 1978, and the model was La-17K. It was discontinued in 1993. La-17K is the latest improved model with a relatively large output. Therefore, after the disintegration of the Soviet Union, this target drone is still in service in the Russian army. Even after continuous software system upgrades, the aircraft still has a place in the Russian army.
3. Product 204
After the La-17 was put into service, the Soviet army actually wanted to have an unmanned reconnaissance aircraft, but because the aircraft used a ramjet engine, it was not appropriate to improve it based on this. But the Soviet army couldn’t wait any longer. In June 1956, the Soviet Council of Ministers required OKB-301 to develop a reconnaissance version of the La-17 and deliver it for testing before July of the following year. OKB-301 took immediate action. Now an AFA-BAF-40R aerial camera is installed on the nose of the La-17, named "Product 201FR". After testing, the aircraft has a ceiling of 7,000 meters and a range of 170 kilometers. In clear weather, it can effectively scout local frontier positions and depth conditions. Two years later, the Soviet military considered developing a reusable unmanned reconnaissance aircraft that can be operated on the ground, which is more difficult. In November 1960, OKB-301 received a task: to develop a reusable reconnaissance aircraft based on the La-17M. The aircraft must be able to conduct daytime photography and radar reconnaissance of a local area with a depth of 250 kilometers, and there is no requirement for real-time control on the ground. The new aircraft was code-named "Product 204" and M.M. Pashinin was the chief designer.
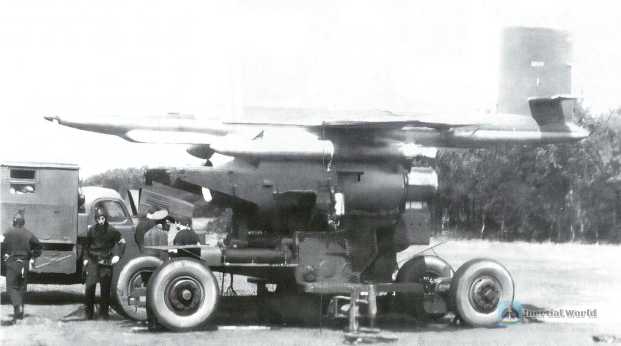

The new aircraft is developed on the basis of the La-17M, with a 54 cm longer fuselage, AFA-BAF-40R aerial camera and new AFA-21 low-altitude camera installed, and AP-63 autopilot installed. In addition, for transportation needs, the wings can be folded, and it can be transported using ZIL-134K trucks, with better maneuverability. In July 1963, a national test was conducted, and the test results showed that the aircraft had a flight altitude of 900-7000 meters, and could conduct photographic reconnaissance of objects 50-60 kilometers away from the launch position at a flight speed of 680-885 kilometers per hour. After the finalization of product 204, it was named La-17R, and the whole system was called TBR-1. The whole system includes the launch vehicle, power supply vehicle, command vehicle, transport vehicle, crane vehicle, radar station, etc. Factory No. 475 produced a total of 20 sets, which were in service until the early 1970s. Subsequently, an upgraded version of the La-17RM reconnaissance aircraft (product 204M) was developed, mainly upgrading the relevant electronic equipment.
Due to the various changes in the design bureau after Lavochkin’s death, since the mid-1960s, the relevant improvements of La-17 have been entrusted to the Kazan Aircraft Manufacturing Plant. By the 1980s, the Kazan Aircraft Manufacturing Plant also carried out a full-scale upgrade of the La-17R series. Including flight performance reaching the La-17MM standard, the camera equipment has been replaced with the updated AFA-40, AFBA-40 and AFA-20 models, and can carry infrared telescopes and radiation detection instruments such as FFT-21 and ASChFA-5M. Some improvements have also been made to the flight attitude. The Soviet Union already had better unmanned reconnaissance aircraft in the 1980s, so the aircraft was soon retired.
Eastern "Long Sky"
At the beginning of the founding of New China, my country did not have the ability to produce unmanned target aircraft, but there was a need for the development and testing of aviation weapons. Therefore, in the late 1950s, 20 La-17 target aircraft and 10 MiG-15bis fighter aircraft were imported. As Sino-Soviet relations deteriorated and the Soviet Union withdrew its experts, my country had no channels to import unmanned target aircraft, and the inventory was getting smaller and smaller. Therefore, my country’s aviation weapon testing was once in a dilemma. In order to get rid of the embarrassing situation of relying on imported target aircraft from abroad, in March 1965, my country launched the independent development of unmanned target aircraft.
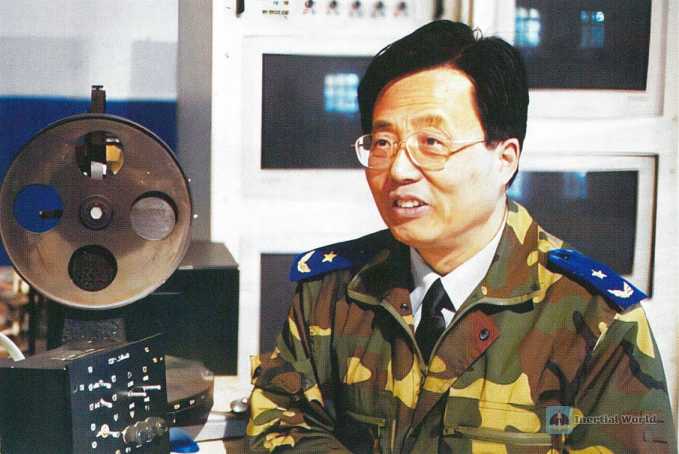
The initial development task was undertaken by the Second Station of the First Test and Training Base of the Air Force, and the person in charge was Zhao Xu. Zhao Xu graduated from the Flight Mechanics and Control Department of the Missile Department of Beijing Institute of Aeronautics and Astronautics, and came to the base in the Badain Jaran Desert after graduation. The environment at that time was very difficult. Unlike the Lavochkin Design Bureau, which had rich experience in aircraft design, most of the entire development team of the "Changkong No. 1" target aircraft were young people who had just graduated and had no experience in developing such equipment. There were only 8 people in the entire base who had been exposed to the knowledge of related subsystems, but they were not in the design team. Therefore, the design team finally determined the principle of focusing on research and development, relying on domestic and ground launch.
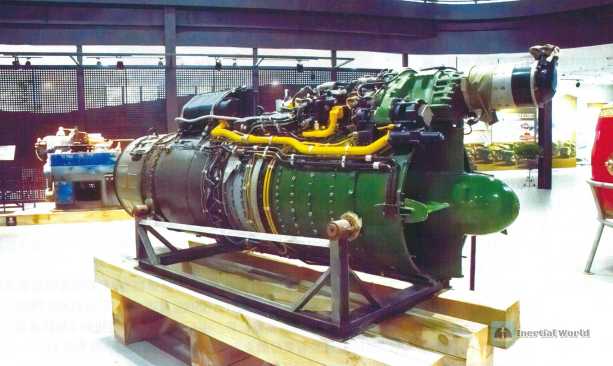
Research and development mainly selected the only modern target aircraft La-17 available at the time as the basis for development, rather than starting from scratch. This is also the most practical solution. At the same time, it can save the overall design link and meet the country’s urgent needs for unmanned target aircraft. Based on the domestic, try to use the equipment that is available or capable of being developed in China. For example, the relevant equipment on the La-17 target aircraft can be copied if it can be copied, and some that cannot be copied or there is no need to copy it can be replaced with existing equipment. The most typical one is the RD-900 ramjet engine. Although this engine has a simple structure and low price, it was not scientific to open a separate production line for this equipment at the time when the economy was not rich. In addition, the problems that the La-17 equipped with this engine had in the Soviet Union also existed in China, so my country also needed to further extend the range and hovering time of the unmanned target aircraft. For this reason, the design team directly chose to use the turbojet-6 engine with the largest production volume at that time, which was consistent with the Soviet counterparts. As for ground launch, it must use equipment such as launchers, but there was nothing to refer to at that time, and everything needed to be paid attention to.
Although it can be said that this can relatively reduce the difficulty of development, it is only "relatively". We only have the physical object of the La-17 target aircraft, and no design drawings, so we don’t understand the "why", so all links must be recalculated to understand why the Soviet counterparts designed it this way. In this work, Zhao Xu led the team to use simple equipment such as slide rules, abacus and hand-cranked computers to conduct comprehensive calculations and demonstrations on the aerodynamic characteristics, structural strength, flight performance, flight track, etc. of the La-17, laying a solid foundation for development. At the same time, the seemingly simple engine replacement also encountered many difficulties. The most typical example is that the thrust of the WP-6 engine is 7 times that of the RD-900, but the aerodynamic layout of the aircraft has not changed much, so the lift torque is generated too early during takeoff, affecting the takeoff of the aircraft. So Zhao Xu did the opposite and increased the nose-down torque when the target aircraft took off, which solved the problem. As for the takeoff method, since the ground takeoff was chosen, the launcher must be designed. The common method at that time was to use rocket boosters, which was what the Soviet counterparts did. However, rocket boosters are disposable, and Zhao Xu wanted to adopt a more economical approach. Inspired by a blurry photo of a three-wheeled pulley of the Australian "Kindivik" target aircraft, they developed a ground takeoff vehicle.
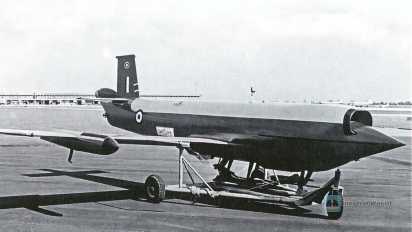
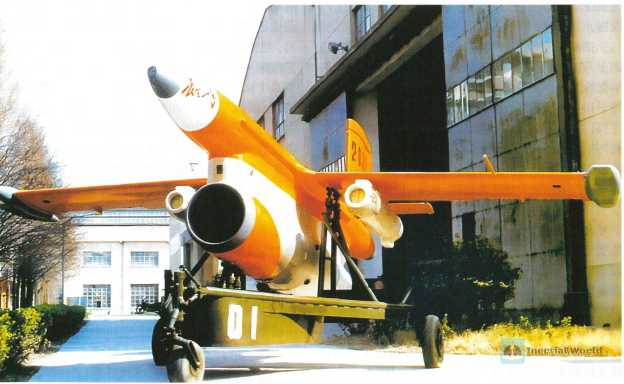
The modified target aircraft was successfully tested, but this was a modification of the test base after all, which was relatively rough. It only proved that it was possible to do so. Therefore, if you want to truly develop an unmanned target aircraft by yourself, you still need to rely on a dedicated UAV development unit to complete it. In April 1968, the National Defense Science and Technology Commission and the National Defense Industry Office issued a target aircraft development task to Nanjing Institute of Aeronautics (now Nanjing University of Aeronautics and Astronautics), requiring the modified La-17 target aircraft to be used as the original standard. The target aircraft was developed according to the new tactical and technical indicators, combined with China’s national conditions and the design specifications and standards promulgated by the state. The target aircraft was named "Changkong" No. 1, and the person in charge was Guo Rongwei. Starting from the overall design, China Southern Airlines conducted a comprehensive design analysis and experimental research on the appearance layout, fuselage structure, power plant, flight control, electrical system, remote control and telemetry system, and take-off vehicle system. The overall design was optimized, the internal loading layout was adjusted, the power plant design was improved, a new flight control system was independently developed, the fuselage structure, control system, fuel supply system, electrical system, radio system, take-off system were improved, and formal production facilities were built.
Based on the modification of La-17 at the First Test and Training Base of the Air Force, China Southern Airlines built a new flight control system at the First Test and Training Base of the Air Force, With the strong assistance of brother units such as the 618th Institute of the 320th Factory, the first aircraft was developed in August 1969, and the first test flight was carried out in October. After that, 8 aircraft were tested successively, and finally in November 1976, the design finalization flight test was officially completed, and in December, the design finalization technical appraisal of the new target aircraft was passed by the Aviation Finalization Committee. In 1977, the state approved the design finalization. This is the first large-scale high-speed target aircraft successfully developed by China, code-named CK-1.
In 1977, for the nuclear weapons test mission, a pair of test pods were hung under the wings of the Changkong No. 1A sample aircraft, the take-off weight of the whole aircraft increased to 2160 kg, and the take-off thrust increased from the original 21.07 kilonewtons to 22.05 kilonewtons. In 1977, Changkong No. 1A began to participate in the execution The project was used to carry out atomic bomb air burst sampling missions, and soon completely replaced manned aircraft sampling. The project won the National Science Conference Award in 1978.
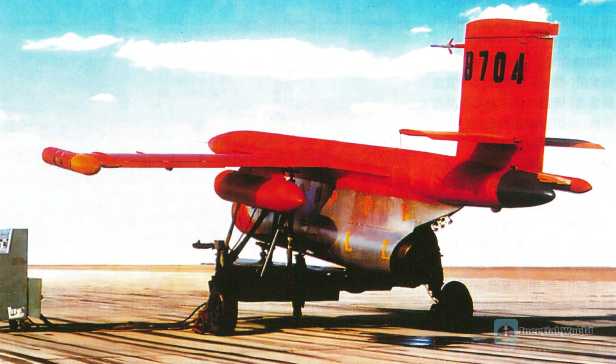
In the late 1970s and early 1980s, the Changkong No. 1 B low-altitude target aircraft was improved for low-altitude air defense weapon system testing and identification. The focus of the improvement was to reduce the flight altitude. The aircraft has a pair of auxiliary fuel tanks under the wings, each with a capacity of 160 liters, and the fuel weight has increased by 240 kilograms; the engine has added "low-altitude cruise" and "large rated" states, the former has a thrust of 8.428 kN, used for low-altitude level flight: the latter has a thrust of 23.03 kN, used for takeoff and climbing; the autopilot has been improved, and when the target aircraft descends from the middle altitude to the low altitude using the level flight altitude, the altitude signaler gives a signal and automatically changes to level flight. After the improvement, the aircraft’s minimum flight altitude has been reduced to 500 meters.
In early 1983, in order to meet the needs of air-to-air missile test firing, the military proposed to equip an unmanned aerial vehicle that could perform high-speed horizontal maneuvering flight with a slope of 70 to 77 degrees. At that time, it was planned to import 10 highly maneuverable "Firebee" unmanned target aircraft from the United States, and it was estimated that 40 million yuan would be needed. Zhao Xu was a member of the "Firebee" inspection team. After learning about the performance of the highly maneuverable "Firebee", he proposed to improve the highly maneuverable Changkong No. 1 on his own. To meet the requirements, it was necessary to improve the structure, control, fuel supply and other designs of Changkong No. 1, and there must be major improvements in appearance, thrust and cruise. With the joint efforts of the Second Station and Nanjing University of Aeronautics and Astronautics, the design, testing and manufacturing of the new Changkong No. 1 were completed in one and a half years. The improvements include the installation of a KJ-9C autopilot, which can perform high-maneuver coordinated turning control, the improvement of the aircraft’s fuel supply system, the installation of a fully enclosed fuel chamber at the front end of the middle fuselage, which keeps the fuel full during flight and ensures normal fuel supply at large tilt angles and negative overload conditions, and the partial strengthening of the fuselage structure: the installation of an infrared enhancer, a miss indicator, a smoke tube and a laser prism; the take-off weight is increased to 2,450 kilograms. On September 3, 1987, the design of this model was finalized and named Changkong No. 1 C. In addition, it is said that in 1988, the Changkong No. 1 E was also improved to simulate ultra-low altitude penetration weapons, but the specific situation is not known.
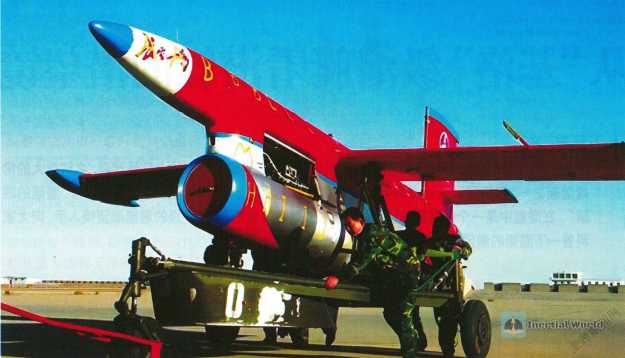
Technical performance
Changkong No.1 UAV has a length of 8.435 meters, a wingspan of 7.5 meters, and a height of 2.955 meters. It adopts a normal straight-wing layout, a mid-wing with a 2-degree downward anhedral angle, a wing area of 8.55 square meters, a horizontal tail located on the vertical tail, and an engine pod suspended under the fuselage. The empty weight of the aircraft is 1,460 kg, the fuel in the aircraft is 600 kg, and the take-off weight is 2,060 kg. The front and rear sections of the fuselage and the engine pod are aluminum alloy semi-monocoque structures, and the wings and tail are aluminum alloy single-beam thin-walled structures; the middle section of the fuselage is an integral fuel tank welded from 30CrMnSi steel plates; the short wing tips, tail wing tips, air inlet lips, nose and tail covers are all made of fiberglass. The power plant is a turbojet-6 engine with a rated static thrust of 21.07 kN at sea level and a maximum static thrust of 25.48 kN. The fuel tank capacity is 820 liters, and the fuel is supplied by the pressurized air pressure from the engine compressor case. The aircraft has a flight altitude of 6,000-18,000 meters, a maximum flight speed of 920 km/h, a flight time of 71 minutes, a maximum range of 950 kilometers, and a maneuvering slope of ±20 degrees to ±40 degrees.
The aircraft’s electrical equipment includes the KJ-9 autopilot, which has four channels: pitch, roll, heading and altitude, which control the aircraft’s elevator, aileron, directional energy deflection angle and engine working status respectively. Each channel is independent and interconnected. The components of the autopilot include a gyro platform and heading gyro, a rate gyro group, a program mechanism, an altitude signaler, an amplifier, a converter and an electric servo, etc. It has functions such as three-axis attitude stabilization and control, program climbing, equal-altitude level flight, automatic landing and emergency crash.
In addition, there are 583 remote control receivers, 25YF-1 telemetry transmitters and YD-1 transponders. The ground stations are MPB-2M remote control vehicles, PCT-6A telemetry vehicles and Heilongjiang radars. During remote control flight, the transponder composed of an antenna, a high-frequency combination, a receiver and a transmitter on the aircraft is responsible for receiving ground signals, then identifying commands and guiding the target aircraft. The aircraft is also equipped with a remote control command receiver, which can transmit 24 remote control commands to the autopilot or other devices that need to be controlled through the receiver-decoder unit. Ground personnel can also monitor the operation of automatic control systems and other equipment through radio telemetry equipment. The telemetry system has 52 channels, which can continuously provide the ground with information such as flight speed, altitude, angle of attack, engine temperature and speed. The transponder can receive the inquiry signal sent by the ground radar and give an answer to distinguish it from other targets in the air.
In order to power the relevant equipment, the aircraft is also equipped with a power system, including a QF-6 starter generator driven by a turbojet-6 engine, with a DC of 28 volts and a power of 6 kilowatts. The DC is converted into AC by a converter to power the flight control system, radio system and other power systems. There is also a 15XYG-45 silver-zinc battery as a backup power supply with a capacity of 45 ampere hours. Because Changkong No. 1 itself is very small, in order to visually simulate a larger enemy aircraft, a total of 5 corner reflectors are installed in the wingtip nacelles and the tail cover, and a total of 4 Sea Eagle No. 1 tracer tubes are installed on the outer sides of the two wings to enhance infrared and radar characteristics. When used as a target drone, Changkong-1 can go back and forth into the shooting area 2-3 times, so as to conduct multiple trainings. If the target drone is not shot down, it can be remotely controlled to land and recover.
La-17 series target drones and Changkong-1 target drones are both first-generation radio-commanded large jet drones. At the time, they were both technologically advanced target drones. Their performance was not inferior to the same-type target drones of the same generation such as the US "Firebee", Australia’s "Gindivik", and France’s CT20. At the same time, both aircraft also pioneered drones in both countries, and they also developed other models based on this. At the same time, their improved versions are still in service in their own armies, which is also the greatest encouragement to designers and technicians in both countries. When they were developed, there was no precedent, but now they have flourished.