With the appearance of the fifth-generation fighters J-20 and J-35 in the equipment sequence of the Chinese Air Force and Naval Aviation, China has achieved a key technological leap from the fourth-generation fighter to the fifth-generation fighter, forming a new aviation equipment system with the fifth-generation aircraft as the mainstay and the fourth-generation fighter as the backbone. According to the old tradition of "equipping one generation and developing one generation" of weapons and equipment in my country, the sixth-generation fighter has also entered the research and development schedule. The "Special Issue on the 85th Anniversary of the Founding of Northwestern Polytechnical University" of the "Journal of Aeronautics and Astronautics" published in January 2024 specially invited Academician Wang Haifeng of the Chinese Academy of Engineering of the Chengdu Aircraft Design Institute of Aviation Industry to write an article to discuss the topic of "Key Technologies for Coordinated Design of High-Performance Fighters and Engines", which envisioned the integrated design of the next generation (sixth generation) of advanced fighters. Previously, Academician Wang Haifeng, as well as Academician Yang Wei of the Chinese Academy of Sciences, the chief designer of the J-20, and Academician Sun Cong of the Chinese Academy of Engineering, the chief designer of the J-35 and J-15, have expressed their views on the sixth-generation fighter. This article, titled "Academicians Discuss the Sixth-Generation Aircraft", summarizes these views. The insights of the three top Chinese fighter chief designers on the sixth-generation aircraft are undoubtedly very valuable knowledge, which helps us to uncover the fog and better understand what is a "sixth-generation aircraft"
Academician Wang Haifeng on the sixth-generation aircraft: The focus is on the coordinated design of aircraft and engines
The advanced fighters in the 21st century must be "coordinated design of aircraft and engines"
The engine (power system) is the "heart" of the fighter and one of the core systems of the fighter. The performance of the engine largely determines the flight and maneuverability of the fighter and is a symbol of platform performance. Since the birth of the fighter, the coordinated design of aircraft and engines has been highly valued. The advent of jet engines has brought new features to aircraft design while eliminating propeller constraints. For example, the elimination of large-diameter propellers allows fighters to use front three-point landing gear, which significantly improves the pilot’s take-off and landing vision to adapt to the increase in take-off and landing speed. However, the thrust-to-weight ratio of early turbojet engines was very low, which led to the extreme focus of fighter design at the time on reducing the weight of the intake and exhaust pipes and friction losses. Most aircraft chose the engine nacelle form, such as the Me-262 using a wing engine nacelle layout, the P-59 integrating the engine nacelle into the wing root, and the Yak-15 setting the engine nacelle under the front center fuselage.
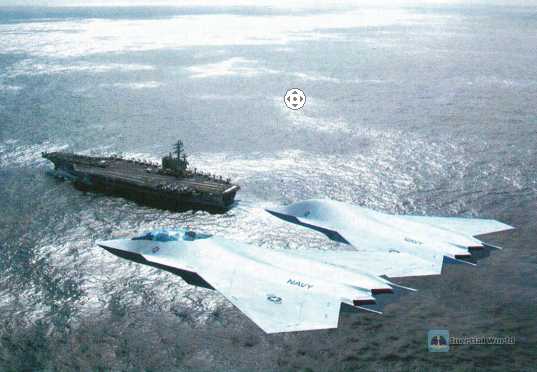
In the 1950s and 1960s, the supersonic competition prompted fighters to fully consider the propulsion system in aerodynamic layout and structural design, giving rise to preliminary comprehensive design thinking. First, the air intake, engine, and exhaust system are incorporated into the body shape surface and studied according to internal and external flows. Secondly, in order to improve the efficiency of intake compression and exhaust expansion under supersonic flight conditions, adjustable external pressure or mixed pressure inlets and ejector nozzles or convergent-expanding nozzles are widely used. In particular, the forward matching of Mach numbers ranging from 0 to more than 2 became a major problem that plagued aircraft design during this period. In 1957, L.F. Nicholson et al. of the United Kingdom discussed the focus of this period in the article "Engine-Aircraft Integration", including the interference between the jet and the fuselage, the integration of large intake and exhaust systems, and the jet lift increase during cruise and take-off and landing. In the 1960s, the development trend of vertical/short take-off and landing aircraft pushed the design collaboration of aircraft and engines to a new height. In order to achieve vertical/short take-off and landing capabilities, a special power system must be designed to include vertical lift, forward thrust, and reaction control force in hovering/low-speed states. In order to make the hovering state balanced and controllable, the layout of the power unit must make the combined lift pass through the center of gravity, and the reaction control system nozzle is located away from the center of gravity. The Harrier fighter chose to install a turbofan engine with four rotating nozzles in the middle of the fuselage. The first two nozzles eject the fan’s outer duct airflow, and the rear two nozzles eject the core engine’s gas jet. This form realizes single-engine vertical/short takeoff and landing, but the large bypass ratio non-afterburning turbofan engine cannot achieve supersonic flight. The Yak-38 chose a power system with two lift engines and a main engine with a bifurcated rotating nozzle. This configuration simplifies the engine design, but single-engine failure is fatal. In 1966, J.W. Ross of the United States discussed different configuration designs such as lift engines and lift fans in the article "An Integrated Method for the Development and Testing of V/STOL Propulsion Systems", pointing out that vertical/short takeoff and landing aircraft should fully integrate the propulsion system during the design and testing phase.
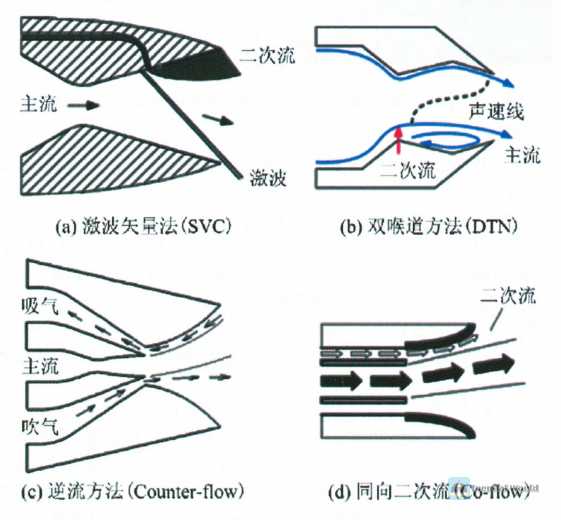
In the 1970s, the third-generation fighter turned to pursue subsonic maneuverability. During this stage, the engine was required to have a high thrust-to-weight ratio and a large thrust, and the medium bypass ratio afterburning turbofan engine became the mainstream choice. The design of the air inlet focused on improving the intake efficiency at subsonic speeds and stable operation at low speeds and large angles of attack. Fixed geometry air inlets with good subsonic performance and light weight became popular again, such as the F-16; while the adjustable air inlet mostly chose the upper adjustable compression ramp form, such as the F-15. The upper compression ramp produces considerable lift while adjusting the inlet to match the launch, which affects the balance of the entire aircraft. During the test flight, it was found that the pitch moment caused by the inlet adjustment was different from the wind tunnel test. The exhaust design focused on the impact of different nozzle spacing on subsonic and supersonic drag, as well as the effect of the central body rectification measures. In the end, the F-15 chose a narrow spacing layout with better supersonic performance, while the F-14 and Su-27 chose a wide spacing layout. In 1983, Ricky (G.K.Ricky) introduced a lot of research on the layout of inlet, engine and exhaust in this period in the article "Comprehensive Fighter Airframe-Propulsion System". Mathematical modeling and numerical simulation methods began to be used in this field. In 1979, the National Aeronautics and Space Administration (NASA) of the United States developed an engine installation performance calculation program based on the wind tunnel test results integrating 19 inlet characteristics and 9 tail nozzle characteristics. In the 1980s and 1990s, the fourth-generation fighter began to be designed. The pursuit of stealth, supersonic cruise and over-stall maneuvering required in-depth cooperation between the aircraft and the engine at the beginning of the design. The stealth requirement limits the choice of the inlet form. Most of the fourth-generation aircraft choose a fixed-geometry inlet with a large S-bend in the pipe and the lip and sidewalls that conform to the parallel principle. At the same time, stealth requires that the nozzle shape and the rear body of the aircraft adopt a unified design. During the bidding stage of YF-22 and YF-23, General Electric and Pratt & Whitney designed dual thrust vector nozzles and unilateral expansion nozzles for the two aircraft respectively. Under the requirements of supersonic cruise of aircraft, military turbofan engines turned to use small bypass ratios, and the resulting increase in fuel consumption prompted the engine to consider choosing newer technologies, such as the variable cycle design of the YF120 engine. Under the requirements of aircraft post-stall maneuvers, the engine thrust vector nozzle became practical. In 1986, Pratt & Whitney published "Fighter Aircraft/Propulsion System Integration"; then in 1992, General Dynamics, McDonnell, Rockwell, Wright Laboratory and other major American aircraft and engine development units also published a series of fighter airframe/propulsion system integration papers, focusing on the consideration of using thrust-limited control to reduce control surfaces and expand maneuvering range.
Entering the 21st century, the informationization level of fighters has rapidly increased, the power of radar, communication, electronic and other loads has increased significantly, energy efficiency and thermal management have become bottlenecks in fighter design, and the scope of flight/engine design collaboration has continued to expand. During this period, the United States gradually implemented research programs such as Adaptive Multipurpose Engine Technology (ADVENT) and Adaptive Engine Technology Transition (AETP), and carried out comprehensive optimization research on all functions, heat, and propulsion such as Integrated Aircraft Energy Technology (INVENT) and High-Efficiency Supersonic Vehicle Exploration (ESAVE), optimizing the aircraft layout, engine configuration, onboard energy form, and energy scheduling management as a whole.
Looking at the history of fighter development, whether it is called flight/engine integration, flight/engine collaboration, or flight/engine integration, the flight/engine has always worked together around the goal of comprehensive optimization, and different periods have different understandings and design concerns. From the long-term development of research work, the degree of cross-coupling between the two sides, and the requirements for in-depth collaboration between the designers of both sides, it is entirely possible to use the expression "aircraft and engine collaborative design", referred to as "flight-engine collaborative design".
Take the sixth-generation aircraft of the United States as an example. The concept of penetrating air control (PCA) proposed by the US military for the Next Generation Air Domination (NGAD) fighter is essentially in line with the initial concept of air control theory proposed by Douhet (G.Douhert), Mitchel (W.Mitchel1), etc., that is, using the air force to penetrate the enemy’s defense line and go deep into the hinterland to directly strike high-value political or military targets. The development of high-survivability technologies such as stealth makes this operational concept possible. Driven by this operational demand, fighter concepts such as the "Global Air Combat Project" (GCAP) jointly developed by the United States NGAD and the United Kingdom, Japan and other countries all reflect the main capabilities and characteristics of high-performance fighters, including:
1) More comprehensive flight performance, which can take into account both deep penetration and maneuverability at typical engagement points.
2) Higher stealth performance, broadening the frequency domain and spatial range, enabling it to penetrate the depth of high-threat areas
3) Larger weapon load, which can support continuous engagement and engage the enemy’s superior forces with a small number of troops
4) Strong situational awareness and electronic countermeasures capabilities, able to avoid enemy detection first and gain the advantage of first-sight-first-fire when it is unavoidable.
To achieve such capability characteristics, the aircraft and the engine must be deeply collaboratively designed from all dimensions to meet the constraints of cycle, cost, technical risk, etc., and achieve overall optimization and balance. Flight performance places higher demands on lift-to-drag ratio and fuel consumption rate. The lift-to-drag ratio of the aircraft is affected by the interaction of internal and external flows and the change of the local shape of the engine nozzle on the basis of the shape layout. The fuel consumption rate is affected by the aircraft’s intake and exhaust efficiency, power extraction and bleed air, and on the other hand, it is affected by the degree of matching between the flight conditions of each section in the mission and the engine design point. The speed difference between deep penetration and typical engagement points is large, and the optimization design is more difficult. It is necessary to carry out collaborative design of the aircraft and the engine for flight performance optimization. Stealth performance requires collaborative design of the aircraft and the engine to further reduce the radar and infrared characteristics of the propulsion system. On the other hand, the possible solutions of the US NGAD all choose an extremely simple layout. This type of layout not only has inherent weaknesses in lateral stability and maneuverability due to the reduction of stabilizers and control surfaces, but also limits the adjustment range of the aircraft’s main dimensions and reference area due to the constraints of the plane shape edge angle. Aiming at control enhancement, the coordinated design of the aircraft and the engine is carried out. The increase in weapon loading has brought about the problem of increased aircraft weight and increased fuselage cross-sectional area, and the thrust needs to be increased to balance the drag and weight effects. At the same time, there are also constraints on the overall balance and force transmission path of the large-sized weapon bay, which increases the complexity of the intake and exhaust and engine layout and internal flow channel design. In the field of situational awareness and electronic countermeasures, the more the aperture gain and power are required, the better. The requirements for high gain on aperture size are constrained by the aerodynamic shape and structural layout, so they turn to continuously increase the demand for power, resulting in a rising demand for heat dissipation. Future high-performance fighters urgently need to work together to solve the problems of power extraction and heat consumption through coordinated design of the aircraft and the engine. In summary, the coordinated design of high-performance fighters
and engines mainly includes:
1) Coordinated design of aircraft and engines for flight performance optimization.
First, the performance design point selection is based on combat needs, focusing on cruise and maneuvering (medium-high altitude subsonic and high-altitude supersonic) of typical combat missions.
Second, the coordinated design of the aircraft and the engine should be carried out around the design point, mainly focusing on the low resistance in the cruise design range and the residual thrust at the maneuvering design point for comprehensive optimization of "thrust-drag".
Third, the power system takes into account both specific fuel consumption (SFC) and supersonic thrust, but if the optimization of the two cannot be achieved at the same time, SFC should be prioritized, and the intermediate state thrust can be appropriately relaxed.
Specifically, the main method is to develop adaptive variable cycle engine technology. Variable cycle engines can achieve a balance between the flow supply and demand of both the forward and backward sides by adjusting the flow ratio, thereby greatly reducing the overflow volume and overflow resistance. Therefore, the use of variable cycle engines can not only adapt to the high Mach number and high maneuverability of fighter jets, but also reduce overflow resistance during subsonic and supersonic cruises, thereby increasing the combat radius of fighter jets. Taking the AETP engine project as an example, the US Air Force believes that replacing the engine developed by the plan can increase the combat radius of the F-35 by 30%, increase acceleration by 18%, and reduce the need for refueling aircraft sorties by 45% in combat patrol (CAP) missions.
In addition, adjusting and improving the inlet (air port)/engine matching, engine/exhaust (air port) matching, etc. in engineering technology can improve the collaborative working effect of aircraft and engines.
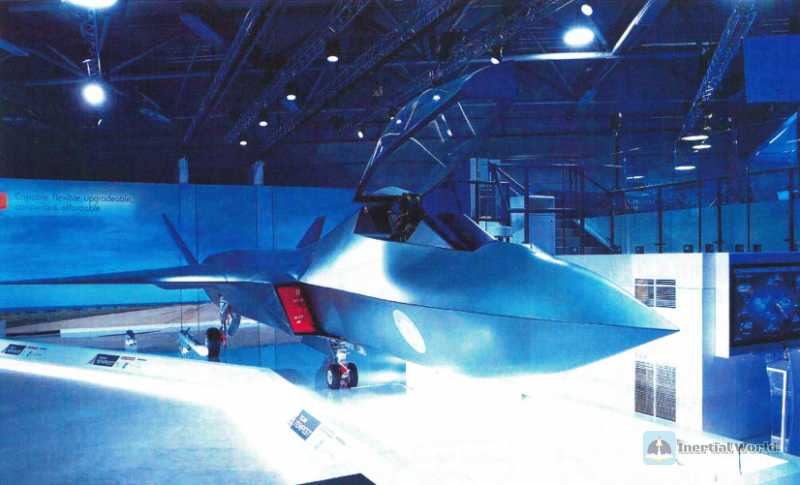
Specifically, for example, adjust the aircraft/engine design matching point, such as selecting the cruise point where the fighter is used for a long time and frequently as the inlet design working condition. In the transonic acceleration section, the transition is made by reducing the engine conversion speed and increasing the fuel consumption rate, and flow control measures such as auxiliary air intake are adopted under take-off and maneuvering conditions. This scheme is conducive to reducing the size envelope of the air inlet, reducing the windward resistance of the air inlet and even the resistance of the whole aircraft.
2) Flight collaborative design for stealth performance optimization.
The radar and infrared radiation signals of the engine have a great impact on the stealth characteristics of the aircraft. The main solutions include: reducing radar radiation through shielding and absorption. Reduce infrared radiation through engine thermal parameter optimization, component cooling/shielding and jet mixing, and active control. For example, as a terminal countermeasure against infrared missiles, active infrared suppression measures such as spraying cold media on the hot wall of the engine tail nozzle and jetting aerosol can be adopted.
3) Flight-engine collaborative design for flight control optimization.
In view of the problem that the new aerodynamic layout of future high-performance fighters is difficult to obtain satisfactory stabilization and control effects in a wide speed range with a simple aerodynamic rudder effect, it is necessary to introduce power to participate in control. The mutual coupling between the engine and the control, first, directly generates force and torque on the aircraft through thrust vector deflection or distributed thrust difference, so as to participate in flight control together with the aerodynamic energy surface, and is to adapt the engine characteristics by adjusting the flight control strategy to obtain the performance benefits of the aircraft as a whole. The main goal is to provide multi-axial control stabilization when flying within the conventional envelope. At the boundary of the envelope (stall, over-stall conditions, etc.), emergency use ensures safety. The implementation forms of thrust control include mechanical and fluid routes. At present, the main one is mechanical, but the United Kingdom, the United States and other countries are actively studying and testing fluid. Fluid thrust vectoring technology achieves thrust vectoring by adjusting the internal flow field of the nozzle. Compared with the mechanical type, it has the characteristics of simple structure and light weight. Currently, common fluid thrust vectoring nozzles include shock wave vector, double throat, co-flow, counter-flow and other types. Considering factors such as aerodynamic efficiency, stealth, control and structural weight, binary mechanical and passive fluid thrust vectoring nozzles are more beneficial to the design of high-performance fighter jets, but fluid thrust vectoring technology is still a long way from practical engineering application.
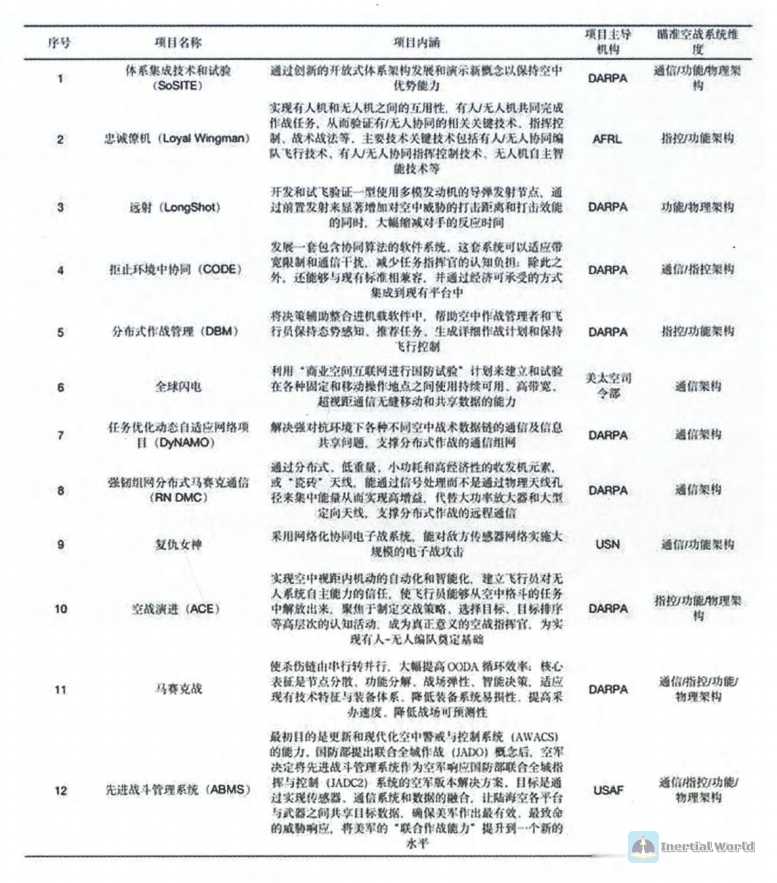
Flying engine collaborative design for full-machine energy optimization.
Facing the high energy consumption and high heat consumption characteristics of future high-performance fighters, the traditional energy acquisition and management system is overwhelmed and has become the main factor restricting the performance of fighters. To solve this problem, it is necessary to thoroughly innovate the energy system and truly realize the "integration" of energy between the flight and the engine: the energy system of the whole aircraft is unified, the whole electric transmission is carried out in the aircraft, and it is converted into the required energy form at the end of use; the energy of the flight and the engine are integrated, the power distribution management is unified, and the independent aircraft accessories and engine accessories are cancelled; the flight heat management is integrated, the heat source is managed through the management, the fuel heat sink is excavated and the new heat sink is explored.
Some key technologies that will be used in the sixth-generation aircraft
Some iconic new technologies of the sixth-generation aircraft have been widely recognized and recognized by all top aviation giants including the Chinese aviation industry. Chief Designer Wang Haifeng also mentioned them in the interview. They include: manned/unmanned collaborative technology, artificial intelligence technology, extremely high stealth technology, and omnidirectional detection and omnidirectional attack technology. Among them, manned-unmanned aerial vehicle coordination means that although the sixth-generation aircraft is still a manned fighter, it can command unmanned aerial vehicles and cooperate with them through advanced networked combat systems; artificial intelligence technology refers to the large-scale application of artificial intelligence technology in the aircraft’s avionics system and other aspects, pushing the level of fighter automation to a new height; extremely high stealth technology, from the current point of view, means that the stealth level of the sixth-generation aircraft is one level higher than that of the fifth-generation aircraft such as the F-22. Specifically, it is achieved by canceling the aircraft’s horizontal tail or even the tail wing, further simplifying the aerodynamic control surface and improving the flight control system, and the overall design of the aircraft is further integrated; and omnidirectional detection and omnidirectional attack technology requires new technologies such as sensor fusion, sensor aircraft, and new airborne weapons. From the introduction of Chief Designer Wang Haifeng, we can see that our country’s sixth-generation aircraft must be manned, and will also adopt the above-mentioned four aspects of design and technology.
Chief Designer Wang Haifeng also mentioned that there are still some disruptive new technologies that are not yet sure whether they can be applied to the sixth-generation aircraft, that is, they have certain possibilities and potential for application in the sixth-generation aircraft. They include: laser weapon technology, adaptive engines, hypersonic weapons, swarm warfare, etc.
At the same time, Academician Wang Haifeng also pointed out that in addition to the recognized technical standards, China’s sixth-generation aircraft must have its own characteristics. He said: We have selected and supplemented some technical directions according to the war we designed, and adopted different organizational models to carry out pre-research and development according to their characteristics and maturity. "Due to the highly confidential nature of the sixth-generation aircraft project, Chief Designer Wang Haifeng certainly cannot reveal what subversive new technologies our sixth-generation aircraft has selected and supplemented, but one thing is clear-our domestically produced sixth-generation aircraft has "unique skills" different from other sixth-generation aircraft, and China’s sixth-generation aircraft is completely developed according to our own national conditions and needs, which best fits the needs of the Chinese Air Force.
When will the sixth-generation aircraft appear? Chief Designer Wang Haifeng is full of confidence. He said: "I believe that in 2035 or the nearer future, we will see (domestic sixth-generation aircraft), (our) current efforts are being transformed into a weapon to protect the sea and sky. "Considering that the United States has set the development node of its sixth-generation aircraft in 2030, and Europe intends to launch a new generation of fighters around 2035, our Chinese sixth-generation aircraft has "moved forward side by side" with European and American strong players in terms of development time schedule.
Academician Sun Cong on the sixth-generation aircraft: air combat will enter the era of cognitive maneuverability
Previously, Academician Sun Cong, an expert in the field of aircraft design and president of the China Aeronautical Research Institute, published a heavy article in the 8th issue of "Acta Aeronautica Sinica" in 2021, "Looking at the Development Trend of Future Fighters from the Evolution of Air Combat Victory Mechanisms", In the section "Winning Mechanism of Future Air Combat", Academician Sun expressed his views on the future sixth-generation aircraft. He believes that the development of a new generation of information technology will be the most significant feature of the sixth-generation aircraft. He said, "From the perspective of the development law of aviation technology in the 20th century, the development of fighter jets is rapidly evolving towards complex air combat systems. With the explosive development of incremental and variable technologies such as autonomy, artificial intelligence, unmanned, computing, and communications, aviation platforms will achieve deeper interconnection and more extensive collaborative capabilities, which directly stimulates the research and application of complex air combat systems. ”
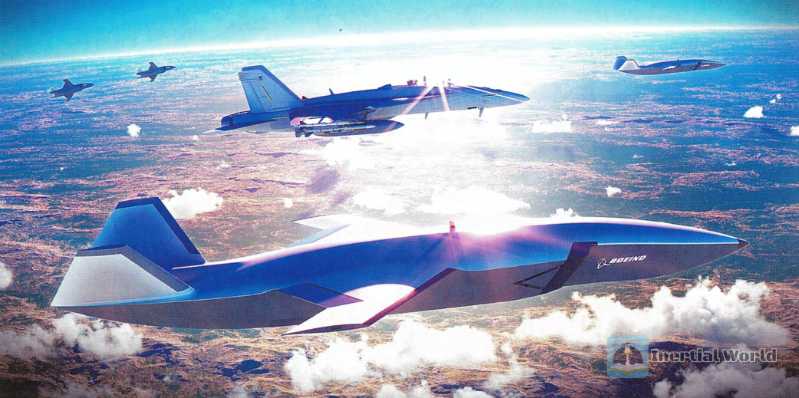
Academician Sun Cong envisioned an air combat scenario in the 2030s: Two high-stealth fighters of Country A are performing air patrol missions, and are suddenly guided by the ground command and control center and ground early warning radar to intercept the air penetration formation of Country B. The fighters of Country A turned on the radar for burst detection at a suitable distance, but found a total of 10 targets in the two formations in front and behind. As the distance between the two sides was rapidly approaching, and the radar of Country A’s fighter could not accurately identify the target, the two pilots had no time to think too much. After coordinated target allocation, they each selected two targets and fired two missiles at each target. During the guidance process, the radar suddenly received a warning of a target. The radar guidance signal was received by the aircraft, but it was impossible to determine which formation in front or behind launched the missile. In a hurry, the aircraft abandoned the mid-course guidance and turned around to disengage. In fact, this was a 2V2 air combat scenario in a broad sense. In addition to two manned high-stealth fighters, Country B also flew four unmanned loyal wingmen, two long-range forward air nodes, and two air patrol aircraft with three functions of decoy/detection/smart interference, a total of eight low-cost/consumable drones.
Academician Sun Cong pointed out that this air combat scenario is not far away from us, and we can find clues from the current technical layout of the US military. In 2016, the US Air Force officially released the public version of the "Air Superiority 2030 Flight Plan", which clearly stated that in order to continue to maintain cross-generational air superiority, the US Air Force needs to quickly build a new generation of air superiority. Combat system and the next generation of air superiority fighter PCA. In August 2020, the U.S. Naval Air Systems Command established the NGAD office to accelerate the development of the next generation of carrier-based fighters. From the current technical layout of the U.S. military, it can be judged that the U.S. military is taking the "next generation of air dominance" (sixth-generation aircraft) as a starting point, and focusing on the communication architecture, command and control architecture, functional architecture and many other key dimensions of the future air combat system. Carry out comprehensive technical research and verification to accelerate the construction of a distributed, highly survivable, highly lethal, dynamic, flexible and efficient complex air combat system.
Judging from the current technical layout of the U.S. military and academic discussions, future air combat will inevitably be a confrontation between air combat systems. At least the U.S. military is shaping a new model of confrontation between air combat systems and accelerating the research and development and construction of related The core concept is: with the next generation fighter platform such as PCA as the core node, a small number of high-end platforms such as PCA are combined with a large number of low-cost, consumable, modular, and highly autonomous unmanned wingman/cruiser, etc. to build a native air combat system. In the future, the core pursuit of the confrontation between air combat systems is to identify and recognize the relationship between the opponent’s multiple nodes, system architecture and complex kill chain, while preventing the opponent from identifying and recognizing the opponent’s system architecture and kill chain, and seek to delay, destroy and interrupt the opponent’s closed-loop function in the entire kill chain. Air combat will enter the era of cognitive maneuverability.
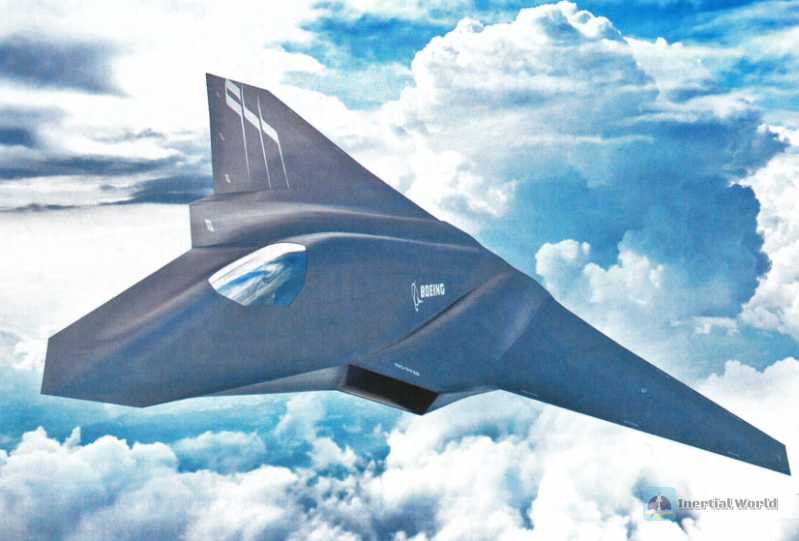
The design of air combat systems in the cognitive maneuver era belongs to the category of complex system design. Different from traditional single systems, complex systems achieve design goals more through distributed control, system autonomous decision-making, local visibility, flexible layering, collaborative cooperation, mutual influence between systems, and the pursuit of minimum constraints. Therefore, it is necessary to seek new methods and means to design complex systems to generate and manage emergent behaviors to meet the application needs of cognitive maneuver air combat. The overall goal of the design of future air combat systems is to take the next generation of air combat aircraft as a strong node from many aspects such as communication architecture, command and control architecture, functional architecture and physical architecture, and realize the rapid, efficient, accurate and parallel closed loop of the kill chain through extensive information interaction between multiple manned/unmanned nodes and different degrees of autonomous decision-making and operation, and realize the emergence of capabilities in many dimensions such as efficiency, robustness, adaptability, flexibility and accuracy. Autonomy and artificial intelligence technology are necessary conditions for the realization of complex air combat systems.
It should be noted that the emergence of the next generation of air combat forms is by no means a negation and abandonment of the previous generation of air combat forms. On the contrary, it is the inheritance and expansion of the previous generation of air combat forms. Defeating the opponent by competing for the comprehensive advantages of the "trinity" of maneuvering in the information domain, cognitive domain and physical domain has always been the guiding ideology of the unchanging winning mechanism of air combat.
Academician Yang Wei on the sixth-generation aircraft: the development progress is on the same starting line as the United States and Russia
In September 2020, after the first flight of the technical verification aircraft of the next-generation fighter NGAD (sixth-generation aircraft) of the United States, Academician Yang Wei was a guest on CCTV’s interview program and revealed some information about the development of China’s next-generation fighter.
First, he pointed out that China’s sixth-generation aircraft, in general, is more inclined to the two major elements of "informatization" and "intelligence" in design, which coincides with Academician Sun Cong. Secondly, Academician Yang Wei said that in terms of the layout design of the appearance, the appearance of the sixth-generation fighter will be more sci-fi, and there will be local air deformation capabilities. Of course, this will not be the exaggerated deformation force similar to "Transformers" in the movie, but a local deformation adjustment. This reminds us of new technologies such as flexible wings. "Flexible adaptive wings" mainly rely on the deformation of the wing surface itself to change the wing curvature and torsion angle to provide an almost ideal wing curvature shape, and achieve aerodynamic adjustment through adaptive changes, which is different from the traditional air control surface and vector thrust. In addition, we have also seen that a recent domestic aviation technology patent has been published, which further confirms the claim that my country’s next-generation fighter is designed with a variable aerodynamic layout. The wing surface of the next-generation fighter is based on the aerodynamic layout of the J-20, and adopts a larger diamond wing surface design, which is very similar to the existing F-22 and F-35 of the US military. The difference is that in order to achieve high maneuverability, the V-shaped vertical tail of the F22 and F35 has not been abandoned. my country’s sixth-generation aircraft has improved this existing vertical tail into a vertical tail with variable upper and lower anhedral angles. When the fighter needs to perform high-maneuver flight, it will be converted into a conventional V-shaped vertical tail. In the supersonic cruise state, the horizontal tail can be retracted. In terms of deformation design, the canard that has not been cancelled is also flexible. When entering the high-altitude and high-speed cruise state, the canard will automatically join the large side strips on both sides of the air inlet to achieve the purpose of stealth and drag reduction.
In terms of the development progress of the sixth-generation aircraft, Chief Designer Yang Wei clearly stated: "my country’s development of the sixth-generation fighter is already at the same starting line as the United States and Russia.