Aluminum is the "panacea" in the metal industry, and its application range is extremely wide. In the military industry, it occupies an extremely important position. Aluminum alloys have the characteristics of low density, high strength, and good processing performance. They are widely used in aerospace, armored weapons, etc., especially in aviation industry materials. It occupies the position of the first material. In modern warfare, wherever there is gun smoke, there is aluminum.
Deadly aluminum
In December 2022, the Ukrainian Ministry of Defense released a video saying that the Avadivka area was attacked by thermite bombs. The video showed that the Russian army launched dozens of thermite incendiary bombs. After the explosion in the air, there appeared a rain of iron flowers like the iron flowers of the people. It is reported that the Russian army uses 9M22S thermite bombs, which are generally launched by BM-21 40-tube 122mm rocket launchers. The warhead weighs about 65 kg and contains 180 independent combustion units. Each unit is about 40 mm long and 25 mm wide, and can burn continuously for more than 2 minutes. After the explosion, the killing range of this bomb can cover about 6,000 square meters, which is about the size of 4/5 standard football fields. It is usually used to attack enemy armored clusters, and can also be used to burn enemy fortifications, buildings, equipment and other important large-scale facilities.
Thermite bomb is the abbreviation of thermite incendiary bomb. Its charge is mainly composed of a mixture of 68.7% thermite, 29% barium nitrate, 2% sulfur and 0.3% adhesive. After the thermite bomb is excited, it releases a lot of heat in a short time. Its temperature reaches 3000℃ and emits dazzling light, which can instantly burn through 100 mm steel plates. On the Korean battlefield, the US military used thermite bombs. In the Chinese People’s Revolutionary Military Museum, the steel helmets and guns of the volunteers who were melted together after being attacked by thermite bombs are still stored.
In fact, thermite bombs were born during World War I. The principle is that aluminum powder and metal oxides produce redox reactions under high temperature conditions. Oxygen atoms release iron from the combination and give way to aluminum, thereby releasing a large amount of heat to generate high temperature, melting the metal into slag and molten liquid. According to literature records, this temperature can reach 2500℃ to 3500℃. At the same time, the large amount of heat released by the reaction melts the aluminum. It is estimated that 500 grams of thermite (iron oxide and aluminum) will burn out within 30 seconds.
Different from adding iron oxide as a reactant in civilian welding operations, thermite bombs will add ferric oxide to aluminum powder to make the thermite easier to ignite. In addition, copper oxide is added to intensify the explosion reaction. Usually, thermite bombs mixed with aluminum and copper can be used as hollow charges for armor-piercing bullets. When they are stimulated by the explosion of explosives, the explosion range is expanded, the explosion time is prolonged, and it is conducive to the expansion and pressurization of bubbles in the water. The power is amazing. For this reason, many types of depth charges, torpedoes, anti-ship missiles, anti-aircraft ammunition, anti-tank armor-piercing shells and blasting shells use thermite explosives as the charge.
In addition to using thermite in large weapons and ammunition, some countries also use thermite in grenades, such as the M202 uses a one-tube four-tube launcher, loaded with 66 mm incendiary rockets, and charged with 0.61 kg of TPA (thickened triethyl aluminum). The effective range is 200 meters, and a salvo of 4 rounds can cover an area of 500 square meters. In the operation to kill Bin Laden in 2011, the US special forces used thermite ammunition at a long distance during the retreat to blow up the stealth helicopter that crashed into Bin Laden’s residence.
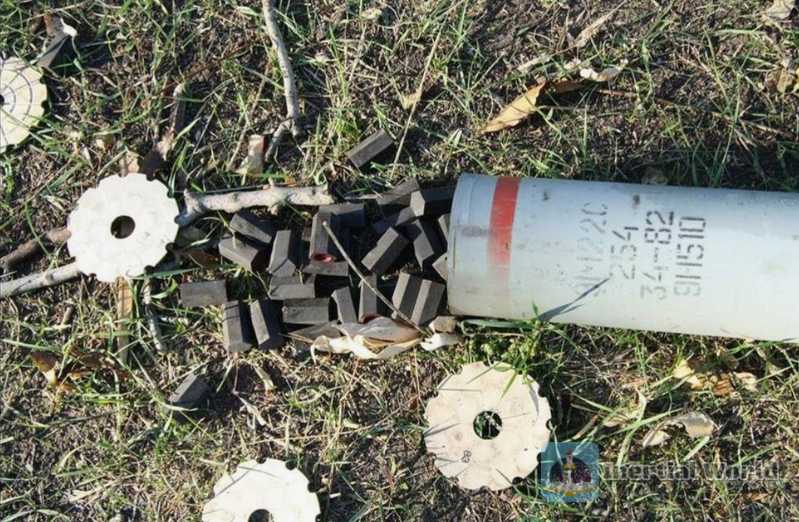
Application in military industry
In 1825, Danish scientist Oster extracted aluminum as a single metal for the first time. It was not until the invention of electrolytic aluminum smelting in 1886 that the foundation for large-scale production of aluminum was laid. In 1906, German Wilm accidentally discovered that after a small amount of copper and magnesium were added to aluminum and placed for a period of time, the strength would increase over time. Therefore, the aging hardening phenomenon of aluminum alloy was proposed, and the first hard aluminum alloy was produced, which marked the birth of modern aluminum alloy. As a new type of material, the strength of aluminum alloy is equivalent to that of steel, but the weight is much lighter than steel, and it is easy to process and form, has strong corrosion resistance, and is rich in resources. Therefore, it is often used as a structural material in the aerospace field.
According to different use conditions and parts, aluminum alloys for aerospace can be divided into high-strength aluminum alloys, heat-resistant aluminum alloys, and corrosion-resistant aluminum alloys. High-strength aluminum alloys are mainly used for aircraft fuselage parts, engine compartments, seats, control systems, etc. In most cases, they can replace aluminum die forgings and are the most widely used. For example, 7075-T7651 aluminum alloys are widely used in aircraft frames, integral wall panels, landing gear, skins, etc. due to their high strength, good toughness, stress resistance and exfoliation corrosion resistance. Heat-resistant aluminum alloys are mainly used in cabins close to motors, air exchange systems, etc., and have a high degree of alloying. For example, 2000 series aluminum alloys with excellent temperature resistance are mostly used for heat-resistant parts and heat-resistant weldable structural parts and forgings on aircraft that work in the temperature range of 150℃ to 250℃. Corrosion-resistant aluminum alloys have good corrosion resistance in media such as air, water and oil. They have good strength, plasticity, impact toughness, fatigue performance and weldability, and are often used in seaplanes.
In the 1960s, the liquid oxygen tank of the rocket was made of 2014 aluminum alloy. The 2219 aluminum alloy developed later became an ideal material for the fuel tanks of rockets and space shuttles due to its stronger stress corrosion resistance, heat resistance, weldability and toughness. In addition to making fuel tanks, aluminum alloys are also used for components, frames and covers of spacecraft. For example, the crew cabin, fuselage, vertical tail flaps, elevator ailerons and horizontal tail of the space shuttle are all made of aluminum alloy.
Aluminum alloys are widely used in marine equipment, which can not only reduce the weight of the ship, increase the speed and save fuel, but also because aluminum alloys have good formability, are easy to cut, stamp, cold bend and cut, and have a large ability to absorb impact stress, which is very suitable for making streamlined hulls. Therefore, general high-speed warships use aluminum alloy materials. For example, the Independence-class littoral combat ship of the United States uses a large amount of aluminum alloy materials. At the same time, aluminum alloy, as a lightweight material, can also significantly reduce the dead weight of ships. The main material of the aircraft elevator on the US aircraft carrier is also aluminum alloy, which is nearly 10 tons lighter than that of all-steel materials. In addition, since aluminum is non-magnetic, it can be used for special-purpose anti-magnetic ships.
In terms of weapon manufacturing, Western countries began to use aluminum armor in the 1950s, and have gone through four stages of development, namely, from high-toughness weldable AI-Mg alloy armor to medium-strength weldable Al-Zn-Mg aluminum alloy armor, and then to aluminum alloy interstitial layer armor and aluminum alloy armor with composite armor. Vehicles using aluminum armor have also developed from armored transport vehicles to light tanks, infantry fighting vehicles and main battle tanks. Like the British "Scorpion" light tank, not only the armored body is made of aluminum alloy, but also the brake disc, steering knuckle, inducer, road wheel, turret seat ring, fuel tank, etc. are all made of aluminum alloy. The bridge bodies of bridge-building tanks and river-crossing pontoon bridges in various countries also use aluminum alloy welded structures. Aluminum alloys are also used to make artillery parts, such as the main frame, cradle, front seat plate, left and right ear shaft brackets, sight bracket, traction rod and balance machine outer cylinder of the US M102 105 mm howitzer. After being made of aluminum alloy, the total weight was reduced by 2.3 tons, and the whole gun was airlifted and airdropped. In addition, aluminum alloys can also be used to make chaff bombs, which are thrown in the air to interfere with radar.
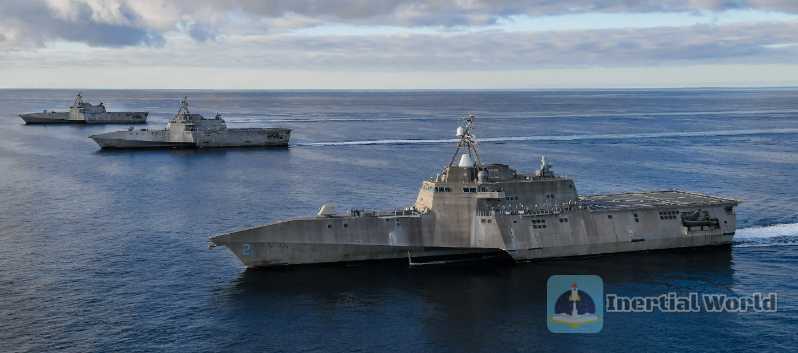
Aluminum’s history of participation in wars.
Aluminum, as a new type of light metal that has only been mass-produced in modern times, was soon used in war.
Before World War I, except for the German "Zeppelin" airship, which used aluminum as a structural material, the main structure of the aircraft was made of wood. However, people found that rain would cause the aircraft to become heavy and unable to take off. For this reason, they began to look for waterproof materials that could replace wood. It was not until Wilm invented hard aluminum alloy that aircraft used aluminum alloy skins. In 1915, German aircraft designer Hugo Junkers used aluminum alloy to manufacture the world’s first all-metal aircraft - the Junkers J1 monoplane. For this reason, aluminum alloy is also known as "flying metal"
During World War I, Germany and other countries had to use aluminum as a substitute to manufacture helmets, water bottles, gas masks and other individual equipment due to steel shortages. Since aluminum ore is mainly distributed outside Europe, the warring parties in World War I tried to weaken each other’s war potential by blocking each other’s sources of mineral mining, smelting and processing, and attacking each other’s maritime transportation. For example, Germany destroyed Britain’s maritime transportation lines through submarines, while Britain took reciprocal measures including trade controls, forcing Germany to strengthen the recycling of aluminum products. At that time, Germany was so short of aluminum that it had to recycle people’s aluminum cans, jewelry, etc. for military manufacturing
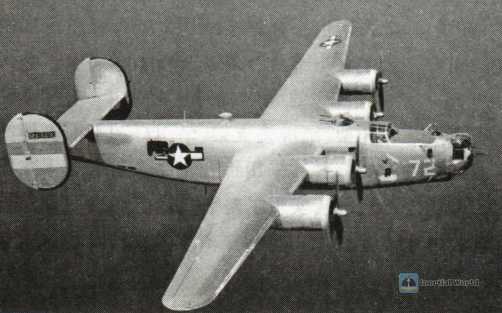
After World War I, aluminum became the third most important strategic material after oil and steel. Although Germany was a country with a shortage of aluminum, after controlling the aluminum industries of Hungary, Yugoslavia and Belgium, Germany’s aluminum production capacity increased significantly. From 1937 to 1941, Germany’s aluminum production soared from 120,000 tons to 324,000 tons. Before 1940, Germany’s aluminum production had always ranked first in the world. Britain’s aluminum production capacity also increased from 83,000 tons in 1939 to 363,000 tons in 1943. By 1943, the United States’ aluminum production capacity had reached nearly 900,000 tons. Although the Soviet Union built two large aluminum smelting plants in Leningrad in 1926, there was still a huge gap. From 1941 to 1945, the total aluminum production of the Soviet Union was only about 420,000 tons. This is why Stalin said, "Give me 30,000 tons of aluminum, and I will win this war." Japan’s domestic bauxite resources are very scarce, and it mainly relies on importing aluminum ingots from the United States or plundering occupied areas. After the outbreak of the Pacific War, the United States stopped supplying aluminum ingots, and the U.S. bombing affected aluminum smelting. In the late stage of the war, Japan had to use wood to manufacture aircraft again.
As a strategic resource, aluminum was the focus of control by various countries during wartime. In order to stabilize the aluminum market, the United States first controlled all aluminum production by the government, and then strengthened the price control of domestic bauxite. This behavior of government participation in the market was imitated by various countries. During the entire World War II, although the demand for bauxite was large, the price of aluminum did not rise sharply. Under the situation of crazy expansion of aluminum production capacity by various countries, global aluminum production reached its peak during World War II. In 1900, global aluminum production was only 6,800 tons. By 1941, global aluminum production soared to 1 million tons. Behind the surge in aluminum production is the growing demand of various countries. In 1938, the United States produced only 900 aircraft throughout the year, and from 1940 to 1945, the annual output jumped to 300,000. Take the B-24 bomber as an example. 85% of the material of the bomber is aluminum alloy. About 19,000 were produced during World War II. During the entire World War II, the United States consumed a total of 3 billion pounds of aluminum (about 1.361 million tons) to manufacture military aircraft.
After World War II, the United States and the Soviet Union continued to promote the research and development of aluminum alloy materials in order to gain equipment advantages. During this period, many aluminum alloy series that influenced later generations, such as the T6 series of 7075 and the 7150 series, were born, which effectively promoted the development of the aviation industry.
New pattern of the global aluminum industry
Compared with other non-ferrous metals, the global reserves of aluminum are quite abundant. The content of aluminum in the earth’s crust is second only to oxygen and silicon, ranking third.
Bauxite is the main source of aluminum. At the current mining rate, the existing reserves can last for at least 200 years. However, the global distribution of bauxite reserves is extremely uneven. Large bauxite mineralization belts are mainly distributed in Africa, Oceania, South America and Southeast Asia. The bauxite reserves in industrially developed countries and large aluminum-consuming countries are generally small. According to statistics from the United States Geological Survey (USGS), the global bauxite reserves in 2021 are 32 billion tons, and the countries with the largest reserves are Guinea, Australia, Vietnam and Brazil. Among them, Guinea’s bauxite reserves are about 7.4 billion tons, accounting for about 23.13% of the world’s reserves: Australia’s bauxite reserves are about 5.3 billion tons, accounting for about 16.56% of the world’s reserves.
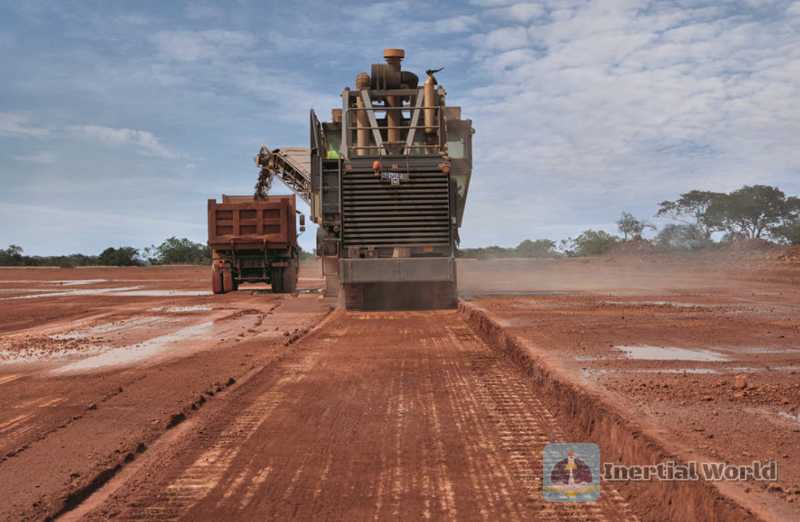
Since aluminum exists in the form of compounds in nature, in order to obtain elemental aluminum, it is necessary to first use chemical treatment to remove impurities from bauxite ore to obtain alumina, and then use electrolytic treatment to obtain liquid aluminum from the refined alumina, and finally make aluminum ingots. Previously, the traditional production countries and regions of electrolytic aluminum in the world were mainly concentrated in Europe and North America. In recent years, electrolytic aluminum is shifting to developing countries with better energy conditions. This is because. After the energy crisis in the 1970s, countries and regions such as North America, Western Europe, and Japan found that due to the heavy reliance on imports of bauxite, the raw material for local production of alumina, the production cost of electrolytic aluminum was high and the supply was unstable, which ultimately led to the lack of competitiveness of aluminum products. Not only that, out of consideration for their own environment, Western developed countries began to migrate their aluminum industry to countries and regions with advantages in resources and energy through mergers and acquisitions or technology exports.
Since the production of alumina and electrolytic aluminum requires a lot of water and energy guarantees, the global aluminum industry has gradually shifted to resource-rich countries. In order to develop the economy, these major bauxite producing countries have successively amended their mining and investment laws, actively supported multinational corporations to build or expand production facilities in their own countries, restricted the export of primary resource products, and vigorously developed their own aluminum industry, increased industrial concentration, digested aluminum resources locally, and exported aluminum products, so that the world’s aluminum production has continued to expand. Among them, the production growth in China, Oceania and Latin America is particularly rapid. According to USGS data, the top three global bauxite production in 2021 are Australia, Guinea, and China, accounting for a total of 72% of global production. The top three global alumina production are Australia, Jamaica, and China, accounting for a total of about 50% of global alumina production. At the same time, while consumption growth in traditional electrolytic aluminum consumers such as the United States, Canada and Japan has slowed down, demand in China, South Korea and India has grown rapidly, which has prompted Asia to form a complete industrial chain and the most potential market, and the world aluminum industry has also formed a new pattern characterized by the combination of resources and energy.