In our traditional vision and concept, manufacturing large equipment such as tanks has always been a very complex and extremely time-consuming industrial production. After all, this type of equipment is composed of thousands of parts, and each part must be precisely designed, manufactured, tested and installed to ensure its performance and reliability. Traditional tank production models have always required a lot of manual operation, which is time-consuming and labor-intensive, and prone to errors and defects. If the tank is to be improved or upgraded, new parts need to be redesigned and manufactured, and then compatibility tests are conducted, which will also increase the production cost and cycle of the tank. It can be said that it takes a long time to manufacture a complete tank.
But not long ago, the official media generously publicly displayed my country’s latest tank production model-the intelligent tank production line of the Inner Mongolia First Machine Factory. In the data video, a highly intelligent, automated, and streamlined production line is continuously producing my country’s most advanced 99A2, 15-type light tanks, VT-4 foreign trade tanks, etc. in an assembly line manner. It is reported that the tank production line uses 3D printing manufacturing technology and intelligent equipment to achieve the assembly line and rapid offline of tank production.
Let’s start with the Inner Mongolia First Machine Factory
Inner Mongolia First Machine Group Co., Ltd. is affiliated to China North Industries Group Corporation. The weapons industry it belongs to is the cornerstone of the modernization of national defense science and technology industry and weapons and equipment. It is the backbone of the development of mechanized, informationized, and intelligent equipment of our army. It is the main body of scientific research and manufacturing of the combat capability of the modern new army system, and an important force in the weapons and equipment and technical support services of various military services. As the country’s only equipment research and production base integrating main battle tank series, medium and heavy wheeled armored vehicle series, and medium-caliber artillery, Inner Mongolia First Machine has formed a research and production pattern of wheel-track combination, vehicle-gun combination, light and heavy combination, and domestic and foreign trade combination, completing equipment research and production tasks on schedule with guaranteed quality and quantity, and fulfilling the primary responsibility of strengthening the army.
In the early days of the founding of the People’s Republic of China, my country’s tank industry was in a blank state. In the several military parades held in the early days of the founding of the People’s Republic of China, the mechanized armored vehicles reviewed were almost all spoils of war captured during the War of Liberation and the War to Resist US Aggression and Aid Korea.
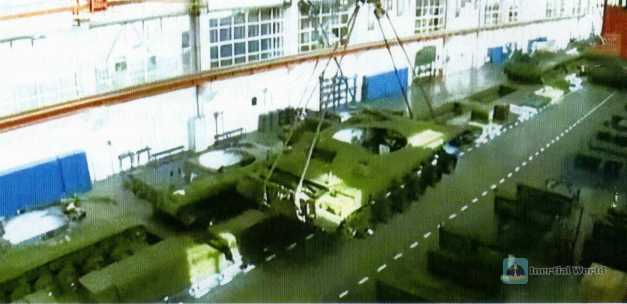
In May 1953, the Chinese and Soviet governments signed an economic assistance agreement, and the Soviet Union helped China build a tank manufacturing plant and a large and medium-caliber anti-aircraft gun and tank gun manufacturing plant. These are the No. 1 and No. 2 Machine Plants. The state has far-reaching considerations for setting up the No. 1, No. 2 Machine Plants and the No. 202 Plant in Baotou. First, from a strategic point of view, Baotou is located in the hinterland of China’s northern border, close to the Soviet Union, and was China’s rear area at the time. It is also outside the flight radius of the US B29 strategic bomber and is relatively safe. Second, Baotou is surrounded by mountains and rivers, with open terrain and rich products. The northern Bayan Obo has rich iron ore resources. The state will build a steel joint enterprise in Baotou, and there is a Beijing-Baotou Railway directly to Baotou, and the Baotou-Lanzhou Railway is also under construction. Third, Baotou is vast and sparsely populated, which can provide good conditions for the tank factory and artillery factory weapon test site. Fourth, the old city of Baotou can be used as a support for the construction of new factories and life supplies. Fifth, building a factory in Baotou is in line with the national policy of developing remote areas, promoting industrial construction and economic development in ethnic minority areas, and improving the rationality of the layout of the national defense industry.
The First Machine Factory began construction in 1954. On December 25, 1958, it trial-produced the first main battle tank manufactured by New China, marking that the factory has since become the cradle of China’s tank manufacturing and production.
On October 1, 1959, at the military parade celebrating the 10th anniversary of the founding of the People’s Republic of China, 32 Type 59 main battle tanks produced by the First Machine Factory drove through Tiananmen Square for review. In 1974, the First Machine Factory developed and finalized China’s first generation of medium tanks, named "Type 69 Medium Tank", marking that China’s main battle tanks have shifted from imitation to self-production, and China’s main battle tank research and development has entered a new era. For a long time, although the First Machine Factory developed and produced Type 59, Type 69, Type 79 and other tanks, due to the technical level and limited national strength, the main equipment of the People’s Liberation Army for decades was mainly the Type 59 series tanks (jokingly called "five pairs of wheels" in the military), which lagged far behind the armies of the United States, Western Europe, the Soviet Union and other countries. In the following years, due to the comprehensive adjustment of my country’s national economy, the closing of the factory’s major product trade contracts and the continuous and substantial reduction of military expenditures, military enterprises fell into the dilemma of "no rice to cook", and the First Machine Factory also faced the risk of "closing down". The state only saved this only tank factory in China with the minimum orders
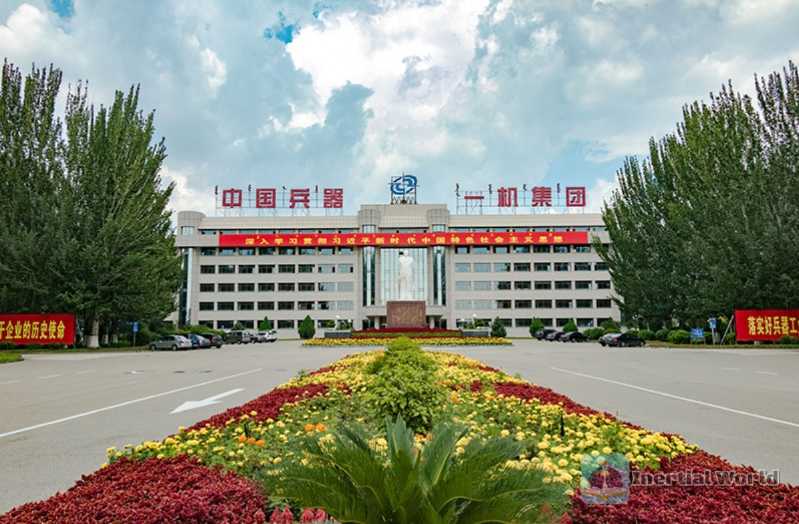
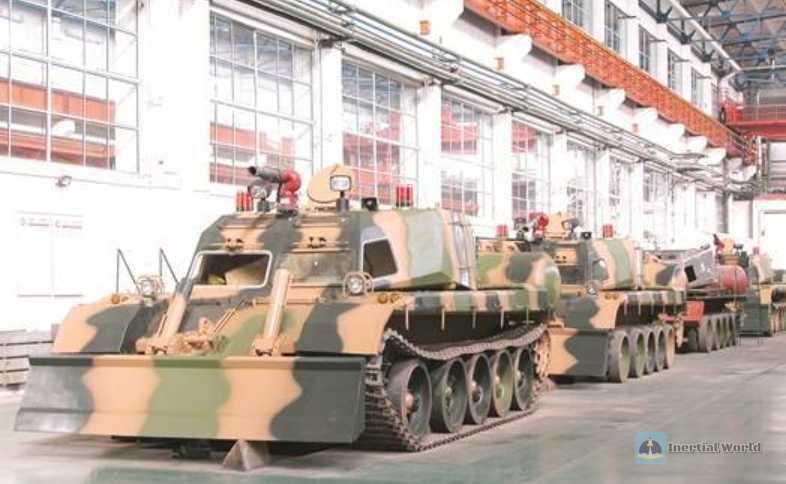
After surviving the most difficult 1990s and entering the new century, my country’s economy developed rapidly, and the entire army began to replace the 99-type and improved main battle tanks on a large scale. Inner Mongolia First Machine took advantage of the situation and once reached its peak today.
At present, the tracked equipment produced by Inner Mongolia First Machine Tool Co., Ltd. covers the entire series of light, medium and heavy equipment, and the wheeled equipment includes multiple basic and variant equipment, which is the backbone equipment of our army’s armored mechanized forces. The total order volume of tracked vehicles and wheeled vehicles, medium-caliber artillery, foreign trade military products, military spare parts, etc. has also exceeded 10 billion. In addition, in combination with the national strategy of "One Belt, One Road", Inner Mongolia First Machine Tool Co., Ltd.’s products have been continuously exported in batches to Pakistan, Thailand, Tanzania, Morocco, Bangladesh, Venezuela, Sudan, Myanmar, Uganda, Nigeria and other countries. Among them, the VT-4 tank has broken through many technical bottlenecks, and its comprehensive performance has reached the advanced level of similar international equipment. It has received large-scale continuous orders from Thailand, Nigeria and Pakistan, showing the good market prospects of China’s domestically produced tanks.
New manufacturing favorite: 3D printing technology
After briefly combing through the history and current situation of the First Machine Factory, let’s go back to the tank production line mentioned at the beginning
As we mentioned earlier, the production process of tanks is accompanied by the manufacture of thousands of parts, and the traditional manufacturing method not only requires a lot of manual operation, but is also prone to errors and defects, and the production cycle of tanks will also be greatly increased. Today, the First Machine Factory has broken this situation by using 3D printing technology in the new production process. In fact, not only the latest tank production, but also various advanced fighters of the Chinese Air Force in recent years have also used 3D printing technology, and this production method has also been used by many media for publicity.
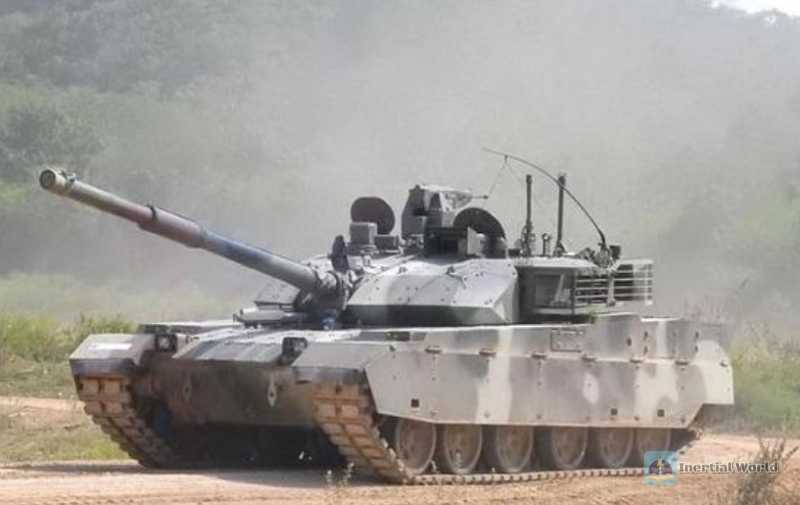
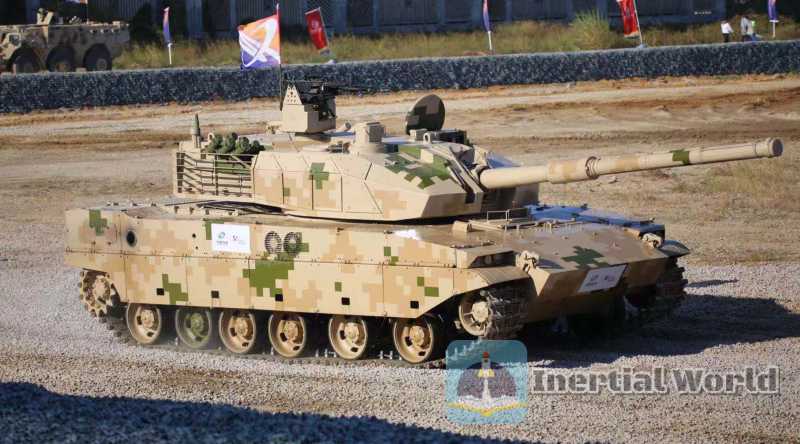
Metal 3D printing technology is "additive manufacturing" technology, also known as "incremental manufacturing", "additive manufacturing", and "additive manufacturing" technology. It is a digital manufacturing technology that realizes moldless forming of components by adding and stacking materials layer by layer. Additive manufacturing technology organically integrates "material preparation/precision forming" and discretizes the manufacturing of three-dimensional complex shape parts into simple two-dimensional plane shapes layer by layer, providing an effective way for designers to realize their creative ideas, especially to realize high-performance or extraordinary performance components and structures. At the same time, this technology can greatly shorten the production cycle, reduce manufacturing costs, save material consumption and processing and manufacturing costs. These advantages make additive manufacturing technology possible for the transformation of the manufacturing industry, and it has great application value and broad application prospects in the research, production, use and maintenance of major weapons and equipment.
In the manufacturing of tank parts, 3D printing technology can directly print out various tank parts according to drawings. No matter the size, shape, or material, they can be customized according to demand, and the printed parts are high-precision, high-strength, and high-durable, and no additional processing and treatment is required. In this way, the production cycle of tanks can be greatly shortened, the production efficiency of tanks can be improved, and the production cost and scrap rate of tanks can be reduced.
Today, my country’s latest tank production line has successfully used 3D printing technology, which not only shows the rapid development of my country’s tank manufacturing, but also shows that my country has formed a 3D printing technology system with a complete system structure, reaching the international leading level in some fields, and reaching the international advanced level in many fields, with a good foundation for leapfrog and rapid development.
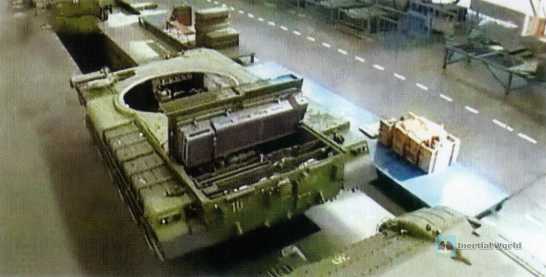
In fact, this is true. my country currently has some relatively systematic and in-depth research on the material science basis of 3D printing, and has developed a series of 3D printing non-metallic materials. Metal 3D printing has achieved very excellent mechanical properties; at the same time, a number of advanced photocuring, laser selective sintering, laser selective melting, laser deposition forming, molten deposition, electron beam manufacturing and other process equipment have been developed; in the manufacturing of aviation engine parts, aircraft functional parts and load-bearing parts, aerospace complex structural parts manufacturing, automotive and home appliance industry new product research and development, personalized medicine and other aspects have been widely used; dozens of 3D printing equipment manufacturing and service companies have emerged, providing support for the rapid development and innovative design of new products in multiple industries.
Intelligent assembly production line
In addition to 3D printing technology, the tank production line of Inner Mongolia First Machine also uses other intelligent and automated equipment, such as intelligent robots, elevators, rail conveyor belts, etc. These equipment can realize the assembly line production of tanks, greatly improve production efficiency, reduce costs, reduce human errors, and make tank production safer and more convenient.
With the continuous development of artificial intelligence technology, intelligent assembly technology and equipment have begun to be applied in key fields such as aviation, aerospace, automobiles, home appliances, semiconductors, and medical care. For example, multifunctional multi-target intelligent assembly equipped with machine vision can first accurately find various features of the target, and automatically determine the shape characteristics and accurate position of the target, and further use automatic execution devices to complete assembly, realize effective control of product quality, and at the same time increase the flexibility, reliability and stability of the production and assembly process, and improve production and manufacturing efficiency; digital intelligent assembly system can carry out global assembly planning according to the structural characteristics and processing characteristics of the product, combined with the supply cycle requirements, to maximize the utilization rate of each assembly equipment and shorten the assembly time as much as possible.
We can see that on the exposed production line, various semi-finished tank bodies are arranged on the track in a certain order, waiting to install important parts such as turrets and engines. The installation of these parts is completed by intelligent industrial robots, which can automatically identify, grab, move, fix and debug various parts according to the program without manual intervention, which not only improves the speed and accuracy of installation, but also avoids the risks and errors caused by manual operation. When all the parts of a tank are installed, it will be transported to the next stage by the elevator for final inspection and acceptance, and then it can be officially offline.
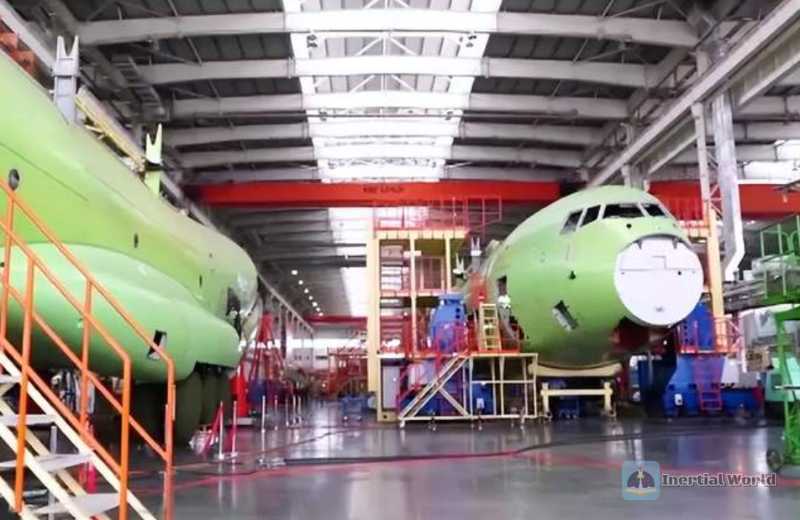
Such a production method can not only ensure the production quality and standardization of tanks, but also save a lot of manpower and material resources, and improve the production efficiency and scale of tanks. Moreover, this production line can also be quickly switched and adjusted according to different tank models, and can produce our own 99A2 and 15 types, as well as VT-4 for foreign trade, and even the next generation of the latest tanks. In short, this intelligent tank assembly line can already meet my country’s needs and goals for tanks in different periods.
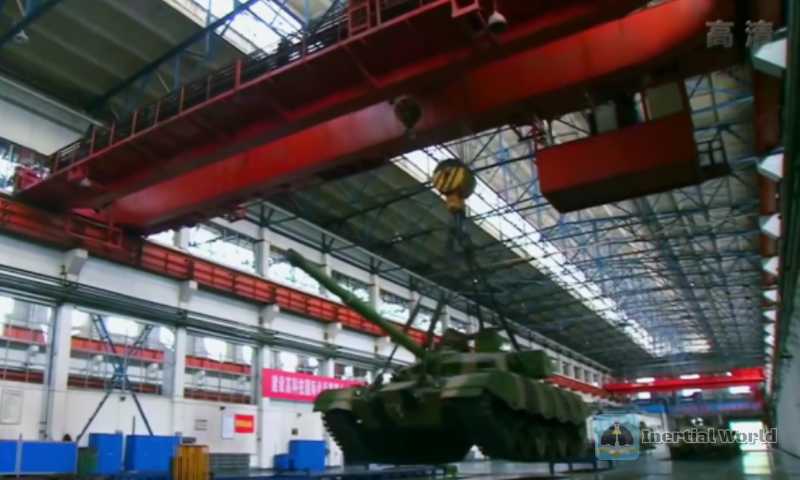
In fact, we are not unfamiliar with intelligent assembly production lines. Nowadays, many companies in my country have used them to improve production efficiency. Among them, the most famous is the Y-20 "pulsating assembly line" that was just exposed some time ago. The opening of this production line has greatly accelerated the delivery cycle of the Y-20, and it is also the basic condition for my country’s Y-20BE large foreign trade transport aircraft to go abroad and enter the international market.
Conclusion
In recent years, with the exposure of various types of advanced equipment production lines in my country, the strength and speed of China’s military industry have begun to constantly change people’s perceptions in the world, and various types of excellent products of China’s military industry have also begun to go to the world. For this, each of us should feel proud and proud.