The Story of Ejection Seats (Part 1)
During World War II, parachutes had become an essential life-saving tool for military aircraft. In an emergency, the pilot would first open the canopy, unfasten the seat belt, then climb out of the cockpit, jump out, open the parachute, and land on the ground. At the time, the success rate of this life-saving method was still very high, at around 90%.
However, as the flight speed of the aircraft continued to increase, it became increasingly difficult for the pilot to climb out of the cockpit and complete the parachute escape solely by relying on his physical strength. In addition, when parachuting at high speeds, the pilot could easily collide with the aircraft’s wings and vertical tail. Studies at the time showed that if the aircraft’s flight speed reached 500 kilometers per hour, the pilot had to rely on external force to leave the aircraft in an emergency and parachute to save his life, so the ejection seat came into being.
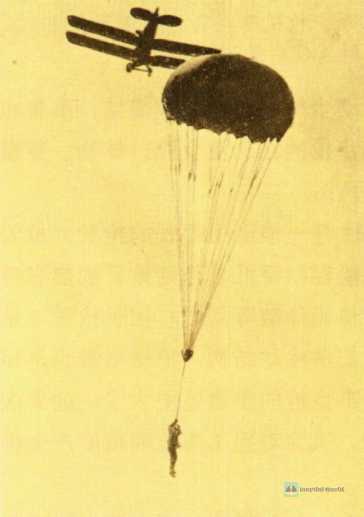
Germany’s first trial of ejection seats during World War II
Although the concept of ejection seats can be traced back to the 1920s or even earlier, truly practical ejection seats did not appear until the late World War II. Germany and Sweden were the first to equip a new generation of high-performance fighters with ejection seats that were usable. The original ejection seats used springs or compressed air as the power source for ejection out of the cabin. Although the technical conditions were limited at the time, this was a great improvement in the pilot’s life-saving method.
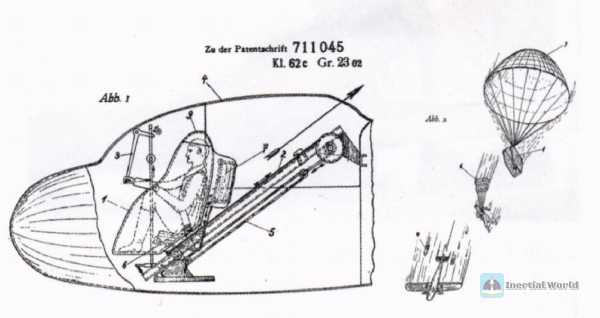
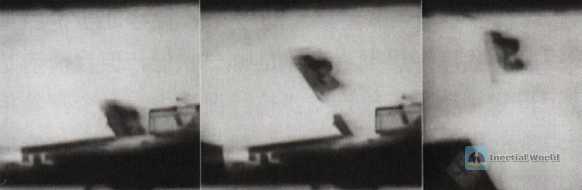
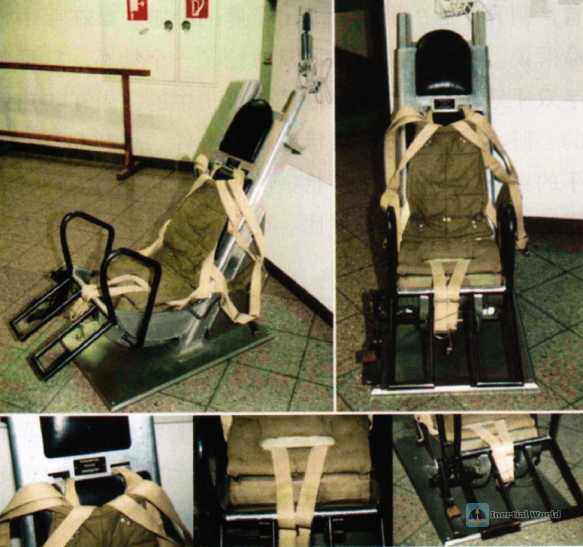
Germany pioneered the first on the small-batch Heinkel He-280 jet fighter, equipped with a compressed air ejection seat. On January 13, 1943, test pilot Helmut Schenk used this to "escape" during the test flight of the He-280, becoming the first pilot to use an ejection seat to leave the plane in an emergency and be successfully rescued. By the end of World War II, Germany had at least 60 records of pilots successfully ejected and saved their lives.
At the same time, the Germans also discovered some inherent deficiencies of compressed air ejection seats, such as the heavy weight of the compressed air container, easy leakage, and low ejection energy. Therefore, the ejection seat powered by gunpowder became another emerging technology route at the time. It not only has more advantages in ejection energy, but also has a lighter system, takes up less space, and is easier to maintain.
Swedish Saab develops ejection seats on demand
Similar to Germany, Swedish Saab (SAAB) also began designing ejection seats based on its own needs in 1941. Its demand was that the latest fighter J-21 used a pusher tail propeller, which could pose a danger to parachuting pilots. Initially, Saab’s ejection seat chose to use compressed air as the power, but later cooperated with Bofors (a well-known anti-aircraft gun manufacturer) to develop a gunpowder-powered ejection seat.
After successfully completing the dummy test in 1944, all J-21 series fighters were equipped with ejection seats. In July 1946, the Swedish ejection seat successfully saved the life of their own pilot. After the war, Swedish Saab’s ejection seat went through several generations of development. In addition to equipping its own fighters, it was also exported. However, in the 1980s, facing the products of Martin and Baker, Saab was not competitive enough and its own demand was not large, so it gave up the development of ejection seats. The last domestically produced Swedish ejection seat was installed on the Saab J-37 "Torn". The later JAS-39 "Gripen" fighter used Martin Baker’s Mk10L ejection seat.
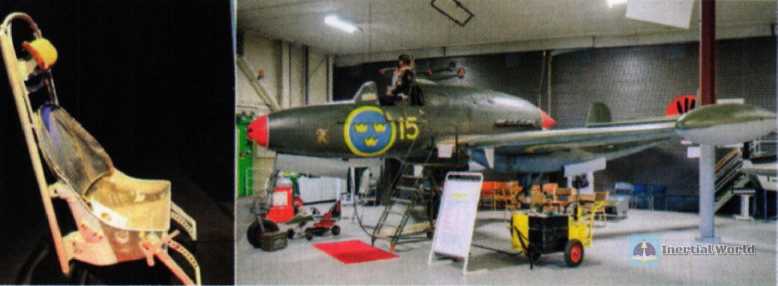
The jet age must have an ejection seat
After the war, with the advent of the jet age, the speed of aircraft became faster and faster, until it broke the sound barrier. It was impossible for pilots to escape by parachuting manually in the past. The demand for ejection seats became more urgent. In the introduction of the German materials, not only the physical objects and technical materials of the ejection seats of Nazi Germany in World War II were seized by the Allies, but also the basic medical achievements directly related to the development of ejection seats.
During the ejection process of the ejection seat, how much acceleration can the pilot’s body (especially the spine) withstand, and what is the limit? In the early stage of the ejection seat research in World War II, Germany conducted targeted research on the ejection facility at Berlin Tempelhof Airport. In the research and testing, both corpses and prisoners from the Sachsenhausen concentration camp were used. After the war, data and information in this area were applied and transformed on both sides of the Atlantic Ocean, and aviation medical researchers in Nazi Germany also worked for the United States and other countries after escaping trial.
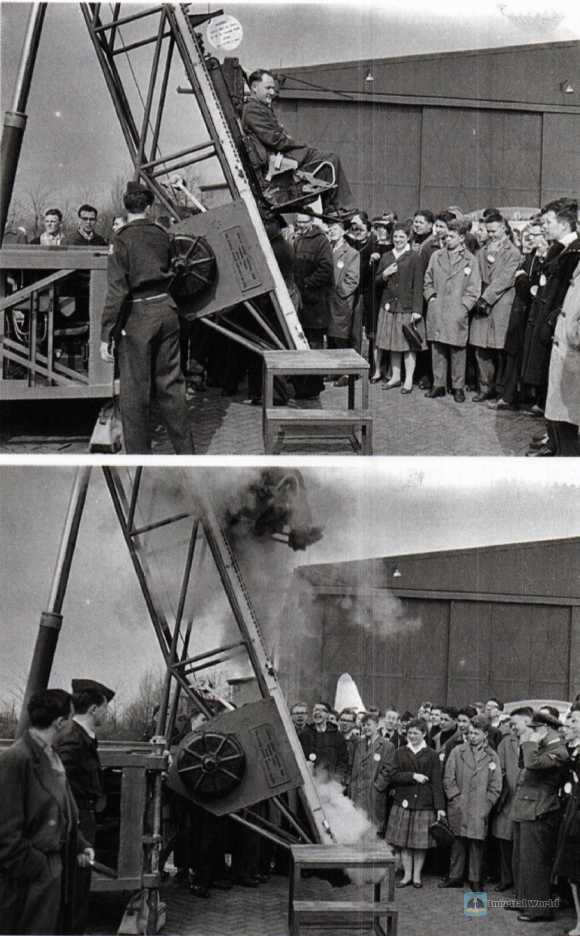
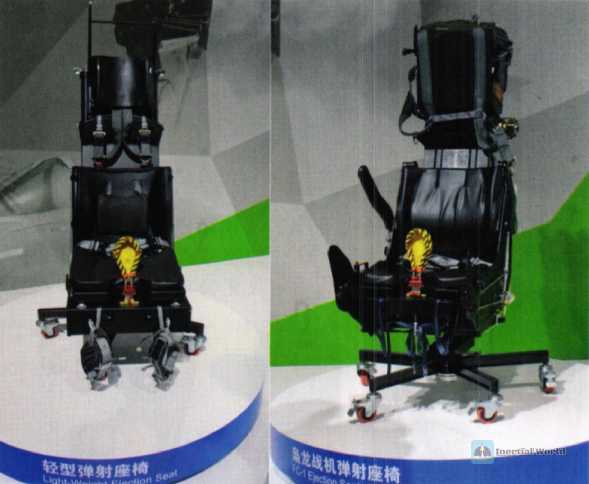
Martin-Baker has successfully saved 7,664 times
Martin-Baker was founded in 1934 by James Martin and Valentine Baker. The company’s initial product was aircraft, and Baker, an ace pilot in World War I, was the company’s test pilot. In September 1942, the Martin-Baker MB.3 prototype was on its tenth flight. Due to engine failure, the aircraft rolled over and caught fire during an emergency landing, and Baker was unfortunately killed. This was undoubtedly a major setback for Martin-Baker. Martin, who lost his close friend and business partner, decided to develop an ejection seat that could save pilots’ lives.
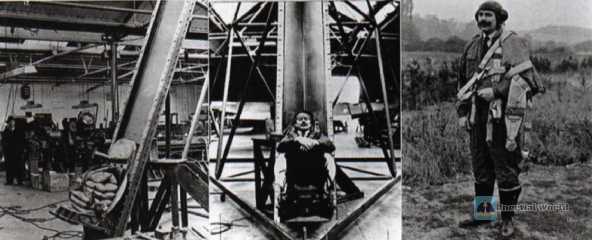
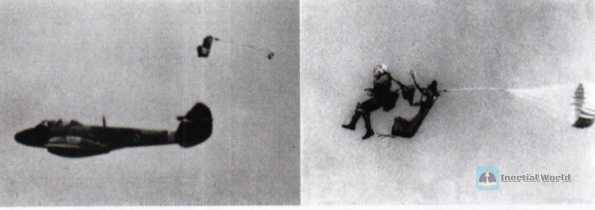
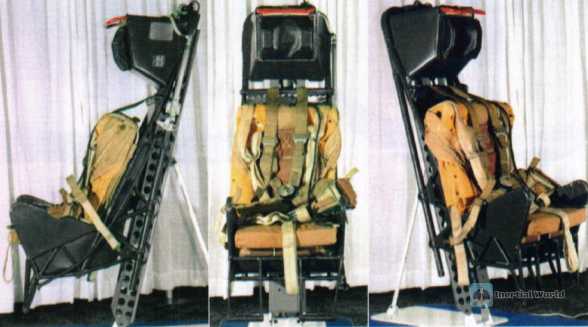
Later, in 1944, the British Aircraft Production Department commissioned Martin Baker to develop the ejection seat. When Martin Baker decided to develop a gunpowder-powered ejection seat, the first thing to be solved was how much acceleration the human body could withstand during the upward ejection process: what was the limit. After Martin-Baker completed a series of ejection tests on 90 kg (200 lb) dummies in early 1945, a fitter named Bernard Lynch in the factory bravely stood up and finally obtained data through his "human test". After a series of ground tests, on July 24, 1946, Lynch completed the first air flight ejection test of the Martin-Baker ejection seat. At an altitude of 2,400 meters, Lynch ejected from the back seat of a 510 km/h Gloster "Meteor" 3 fighter. The ejection seat worked well and Lynch landed perfectly. Subsequently, Lynch successfully conducted more than 30 ejection tests under various conditions, which eventually laid the foundation for the finalization of the first generation of Martin-Baker ejection seat.
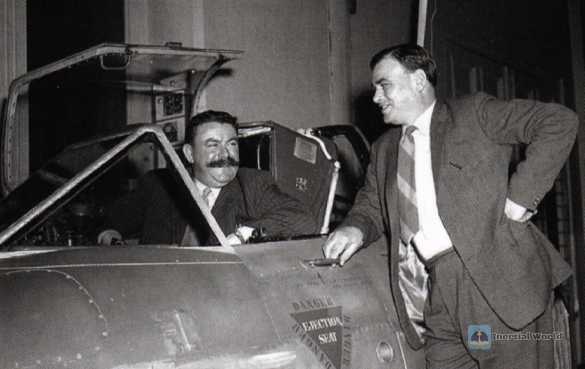
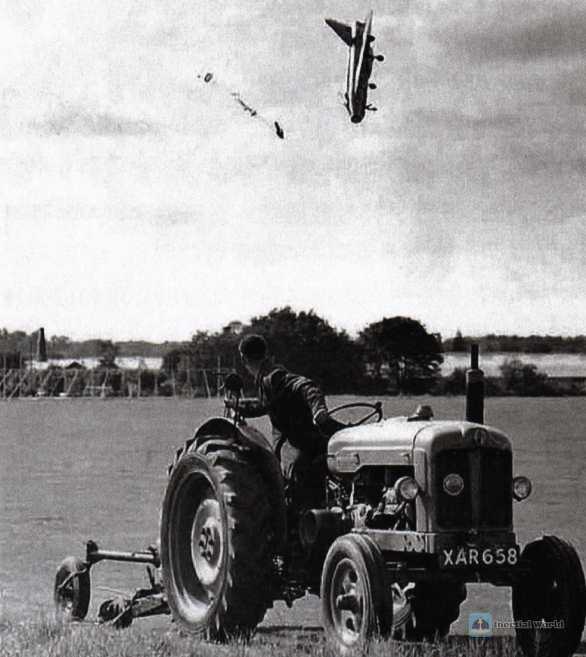
After the birth of Martin-Baker’s first mass-produced ejection seat Pre-Mk1, in a test flight of the Armstrong Whitworth AW52 flying wing verification aircraft in May 1949, test pilot John O. Lancaster used this ejection seat for the first time in actual application. For more than 70 years since then, Martin-Baker’s ejection seats have been widely used on Western fighters. As of now, data from Martin-Baker’s official website shows that its ejection seats have successfully saved pilots’ lives 7,664 times.
From a variety of models to American standardization
The development of ejection seats in the United States after the war was not only digested and absorbed from German spoils of war, but also introduced the British Martin-Baker ejection seats and the "chaos" that eventually emerged: the developers include North American Douglas, Republic, Lockheed, Grumman and other aircraft companies, as well as ejection seat manufacturers such as Weber, Stanley and Stansell, and the users, the US Air Force and the US Navy, each taking what they need. Almost one type of ejection seat for each fighter, the "bad result" is a big trouble in cost and use and maintenance. The high initial procurement cost and spare parts cost are certain, and the pilots who use it and the ground crew who maintain it have to master one type of ejection seat after another.
Thus, in the mid-1970s, the U.S. military began to promote the standardized and universal ACES (Advanced Concept Ejection Seat), which brought benefits such as cost advantages of large-scale procurement and "burden reduction" for pilots and ground maintenance personnel. Initially, the development and production contracts for the ACES 2 ejection seat were awarded to McDonnell Douglas and Weber Aircraft. In the nearly half-century changes in the U.S. aviation manufacturing industry, Weber withdrew from the business. After McDonnell Douglas merged with Boeing, the ACES product line was transferred to Collins Aerospace, a subsidiary of Raytheon Technologies today.

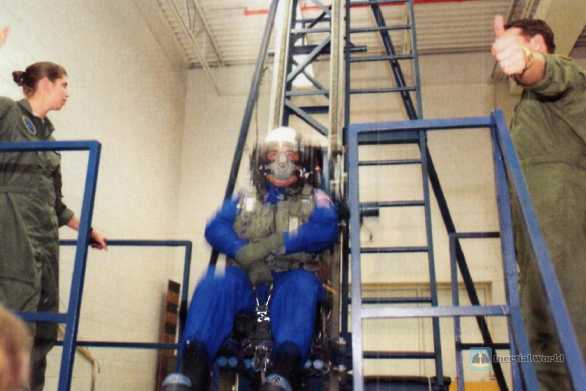
After pulling the ejection handle
In an emergency, after the pilot pulls the ejection handle, the subsequent ejection life-saving procedures mainly include these stages: ejection preparation, ejection start, ejection channel clearing, ejection departure, ejection deceleration, separation of the person and the chair, and stable landing.
When the pilot decides to eject from the aircraft, he should maintain the correct ejection posture as much as possible. After the pilot completes the "ejection preparation", he pulls the ejection control handle quickly and forcefully with both hands at the same time (or with one hand) to activate the energy mechanism of the seat ejection control system, which completes the tasks of tightening the seat shoulder straps, tightening the waist belt, and lowering the arm limiter.
After the ejection control handle is activated, the first-stage power device of the ejection seat is automatically directly or indirectly activated, and at the same time, the work of "ejection channel clearing" is completed - either the canopy is jettisoned during the canopy ejection, or the canopy gun is fired or the micro-explosive cord is detonated during the canopy ejection.
After the first-stage power of the ejection seat is activated, the seat rises, and during the ascent, the leg limit belt is tightened, the oxygen supply on the aircraft is cut off, the emergency oxygen system on the seat is connected, the seat program control system is activated, the remote ignition system is fired and the second-stage power device is started. Under the joint action of the first-stage and second-stage ejection power systems, the person-seat system is ejected from the aircraft, and the divergence control of the ejection trajectory is performed.
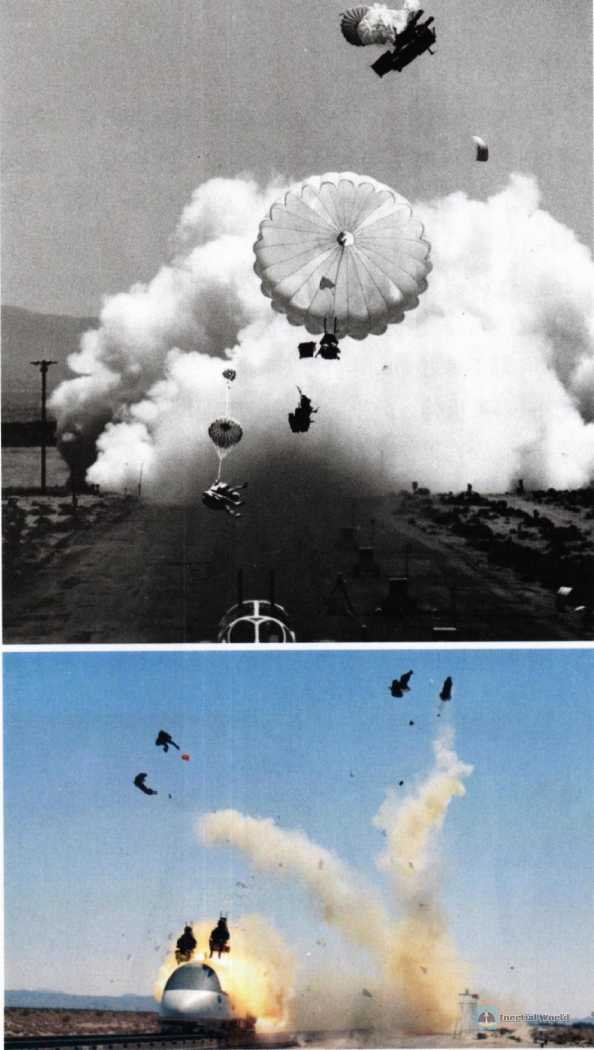
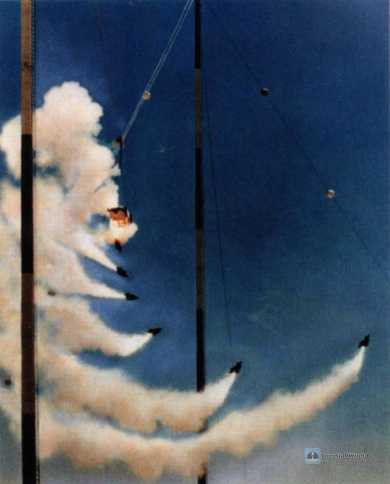
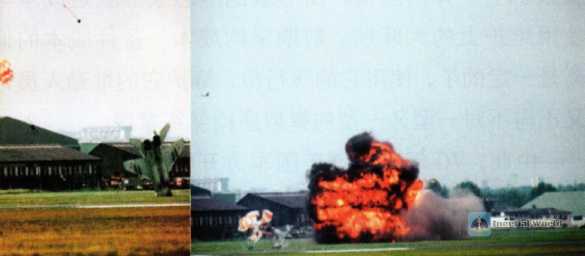
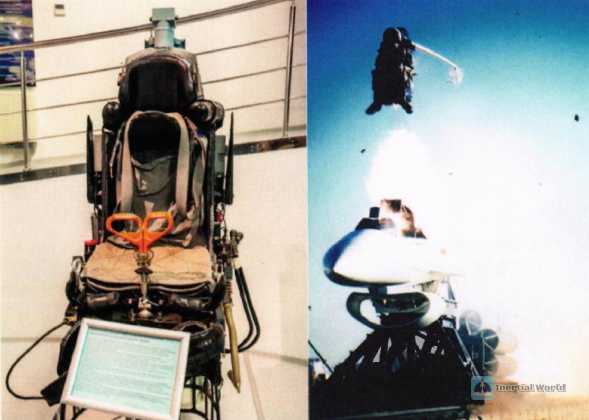
After the ejection seat leaves the cabin, it relies on the action of the parachute gun or the parachute shooting mechanism to shoot out the stabilized deceleration parachute, or uses the hard stabilizer bar to stabilize and decelerate the person-chair system. At the same time, the ejection seat’s program control system completes the collection of airspeed and other signals.
As the stabilized deceleration parachute begins to work, after the ejection height reaches the set height of the control system, the restraint points between the seat and the pilot are released, and the life-saving parachute is ejected to separate the pilot from the seat. After opening the main parachute, the pilot descends steadily and lands safely, and uses the life-saving items carried to ask for help or save himself.
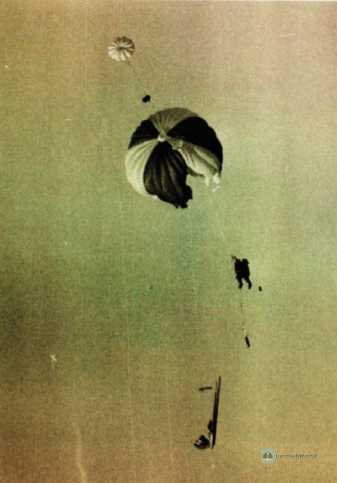
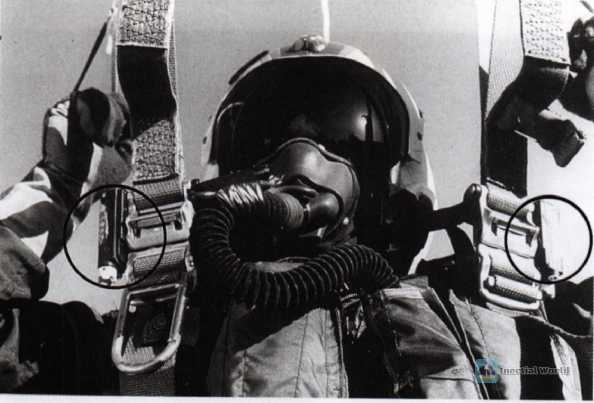
Is it a cover to be thrown or a cover to be penetrated
The "ejection channel clearing" stage in ejection life-saving is mainly to clear the canopy directly above the pilot that blocks the upward movement of the ejection seat. The methods adopted are mainly to throw the cover and to penetrate the cover. As the power source for jettisoning the canopy as a whole from the aircraft, there are high-pressure cold air type, high-pressure gas type (usually the two are backed up by each other), and there is also a canopy rocket type for dealing with larger and heavier canopies.
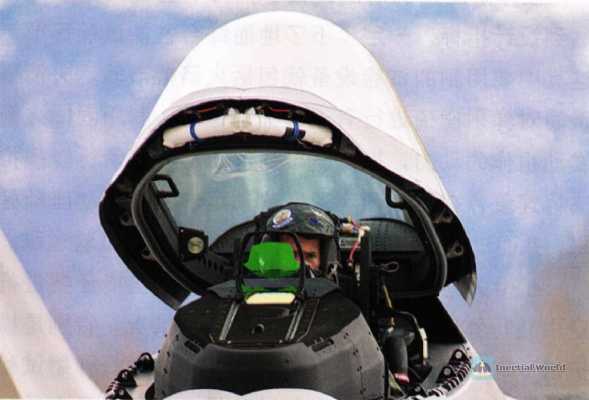
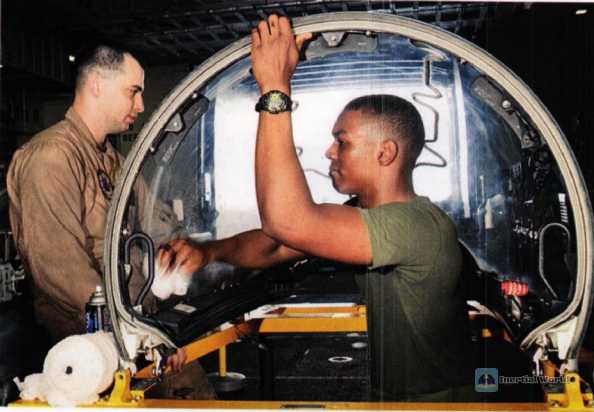
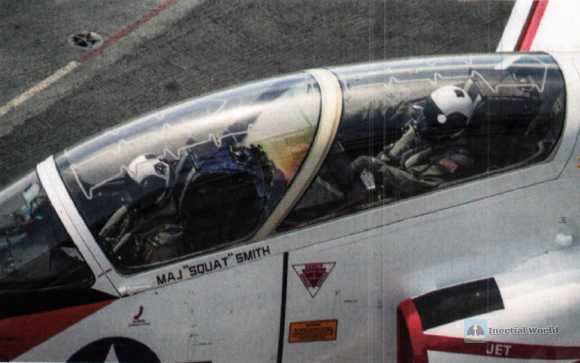
However, for the ejection seat that uses the canopy ejection, the seat ejection power can only be activated after the canopy is completely jettisoned from the ejection channel. The time for throwing the canopy is generally 0.1 to 0.4 seconds, which will cause a loss of altitude in some unfavorable postures (such as a high rate of descent), affecting the life-saving effect. Therefore, the ejection channel is mostly cleared by penetrating the canopy, that is, when the seat is started, the transparent part of the canopy is pre-broken to reduce the load of the transparent part of the canopy on the pilot during the ejection process.
There are mainly two ways to penetrate the canopy. One is a canopy breaking gun, which breaks the transparent part of the canopy through a canopy breaking gun installed on the top of the ejection seat. This canopy breaking method is easier to implement and is effective for canopies with lower strength (non-directional glass, i.e. cast polypropylene or cast polymethacrylate glass materials). In the face of canopies with higher strength, better toughness, and less breakable (directional glass, i.e. stretched polypropylene or stretched polymethacrylate glass materials), it is necessary to use micro-explosive cords pre-laid on the transparent part of the canopy to directly explode the transparent part. In the ejection life-saving process where every second counts, there is no time delay for throwing the canopy, and the ejection seat that uses penetrating the canopy has significantly improved performance.
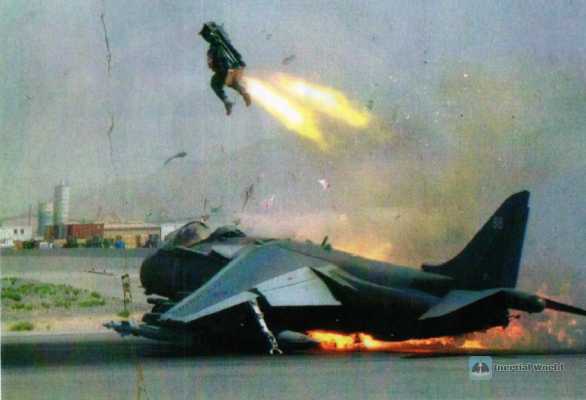
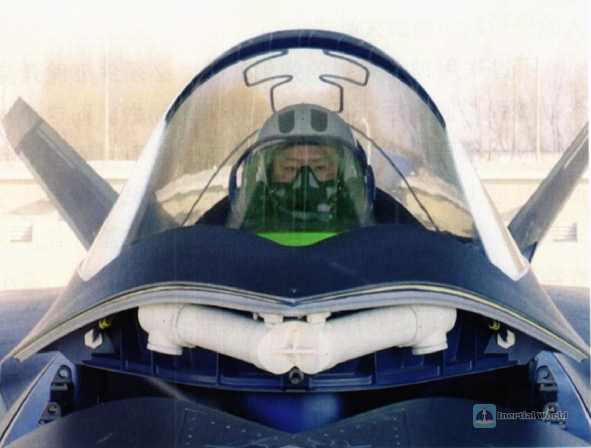
In the early models of the ejection seat, the ejection handle was set on the top of the seat. In this way, the pilot puts both hands on the ejection handle on the top of his head. When pulling, on the one hand, it ensures that the pilot’s posture is correct during ejection, and on the other hand, it pulls down the "curtain" and puts the pilot’s head and oxygen mask under the protection of the curtain to avoid the oncoming attack of high-speed airflow, avoiding the danger of the head being tossed and twisted under high-speed airflow.
In the design of the Martin-Baker ejection seat, the ejection handle originally added to the front of the seat between the pilot’s legs was auxiliary, to ensure that the pilot could smoothly pull the ejection handle and eject to survive when the pilot was overloaded by high G acceleration and could not raise his hands. But later this auxiliary design became the mainstream and completely replaced the ejection handle on the top of the ejection seat. The development of pilot helmet technology has also completely avoided the potential dangers of high-speed airflow blowing on the pilot’s face after ejection, such as facial deformation and lung damage.
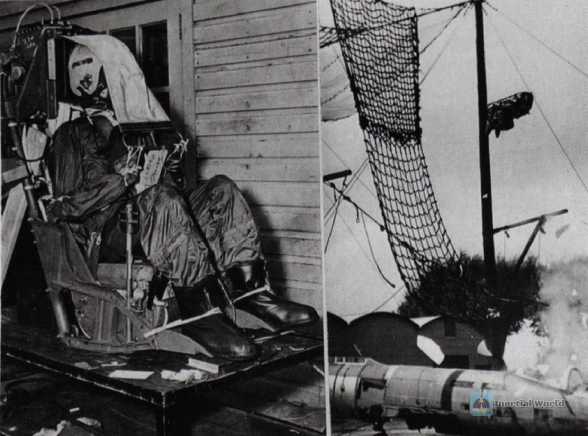
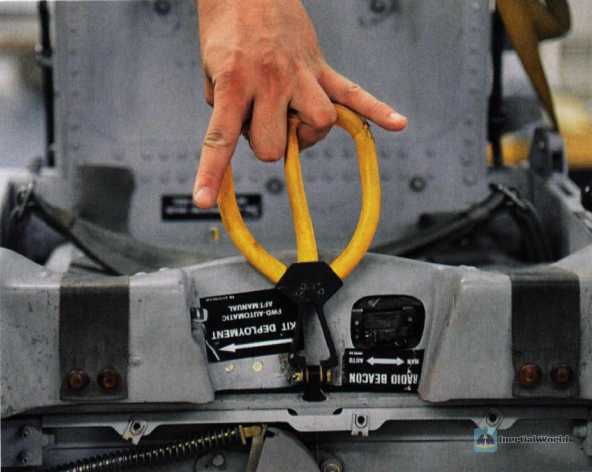
Indispensable test link
In the process of developing the ejection seat, in order to verify whether its performance meets the design indicators, the ground comprehensive performance test link must be indispensable. The test equipment to be used includes the rocket sled rail. The rocket sled rail conducts a speed ejection test on the ejection seat. The solid rocket engine is used as the power to propel the sled to slide at high speed on the rail to simulate the flight speed. When the predetermined speed or predetermined position is reached, the seat is ejected, and the entire test process is recorded by electrical and optical measuring equipment. After the relevant ground ejection test is completed, the ejection seat must also undergo an air flight ejection test to be closer to the actual situation, especially to simulate the ejection in an unfavorable posture during maneuvering flight. Aerial ejection tests are usually conducted with dummies, and ejection test aircraft are generally modified from fighters, trainers or bombers with front and rear cabins.
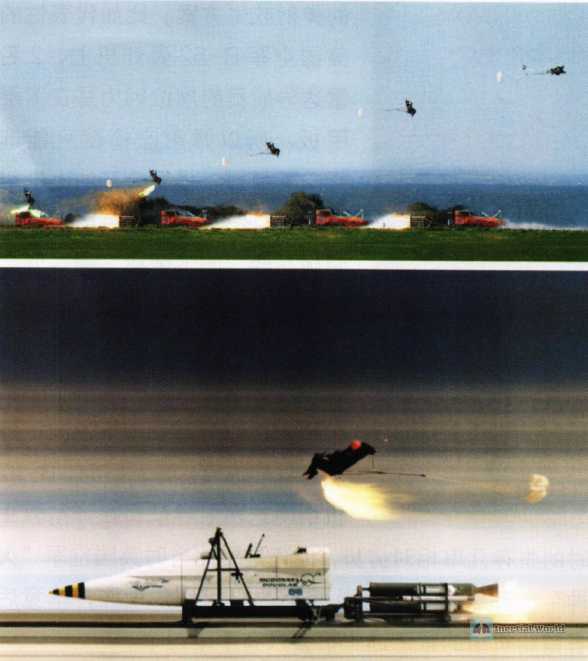
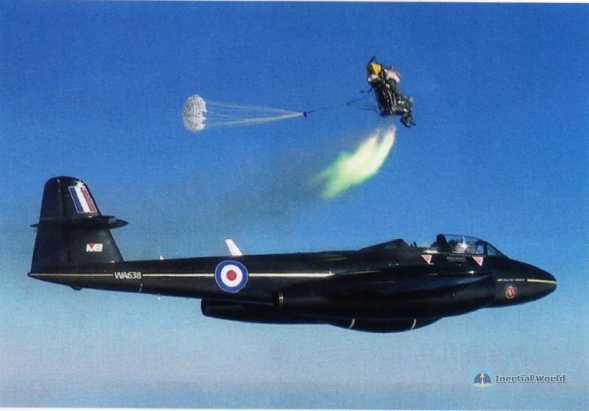
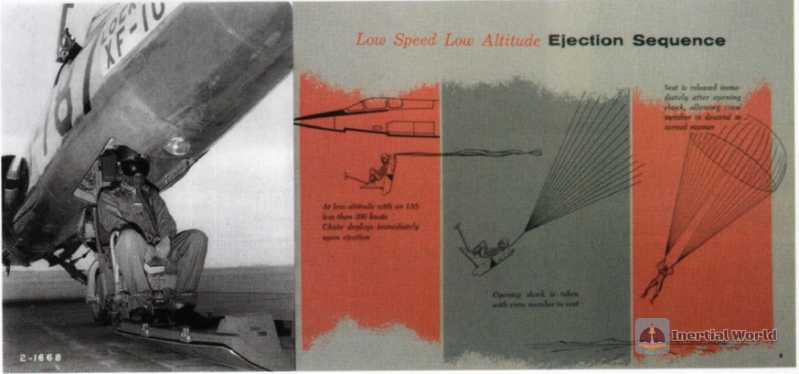
Ejection is not all upwards
For the ejection of the ejection seat, it can be simply understood as a vertical and horizontal movement process. Within a certain period of time, the vertical rise of the ejection seat must exceed the height of the vertical tail, and this "certain period of time" must be very short (in other words, the rise speed of the ejection seat is fast enough), otherwise the person and the chair who just left the cabin will be "caught up" by the vertical tail behind. In addition, the strong blow of the oncoming airflow increases the risk of this "collision". Therefore, in the early stage of the development of the ejection seat, there was a "downward ejection" plan to completely avoid the vertical tail of the aircraft. But obviously this reduces the chance of survival compared to "upward ejection", especially in low-altitude flight. Therefore, fighters that use "downward ejection" ejection seats are extremely rare cases, including the F-104 "Star" fighter in the 1950s. It had to choose "downward ejection" at first because the F-104 flew too fast. It was the first mass-produced 2x supersonic fighter. In addition, its T-shaped vertical tail was designed to be very tall. If the ejection seat was ejected upward during supersonic flight, it would be "caught up" and collided with the vertical tail before it flew high enough.
It is not just a short-term application on the F-104 fighter. "Downward ejection" is still a "last resort" ejection life-saving solution on large platforms such as bombers. For example, on the representative US Air Force B-52 bomber, the seats of the two radar navigators are on the lower deck, so the ejection seat can only choose to eject downward. According to the public B-52G flight manual from the 1980s, it is clearly stated that the minimum altitude for "downward ejection" is 600 meters, and there are additional conditions. This data only applies to horizontal flight. It is acceptable for downward ejection in a dive state, but it is conservative for downward ejection in a climb state. There is no doubt that the survival rate of the two navigators in the B-52 crew is relatively disadvantaged during the ejection rescue, but it is still slightly more optimistic than the crew on the British Air Force’s "fire Soviet Tu-95 bomber" at the time. After all, the "later god" left the crew with only manual parachute for emergency escape.
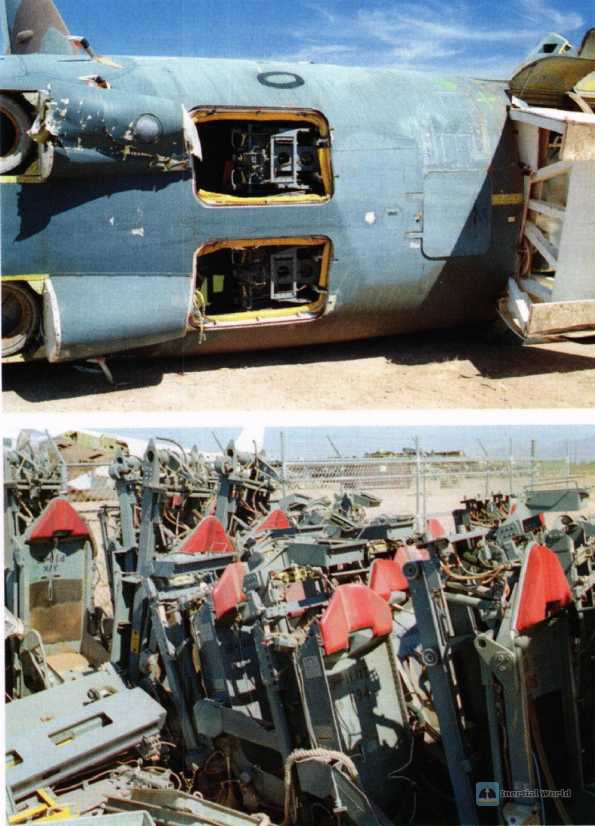
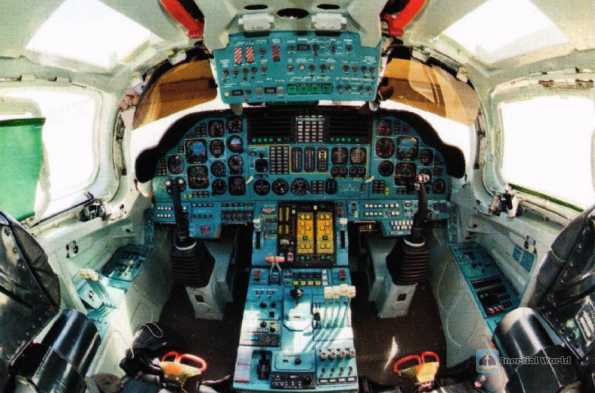
(To be continued)